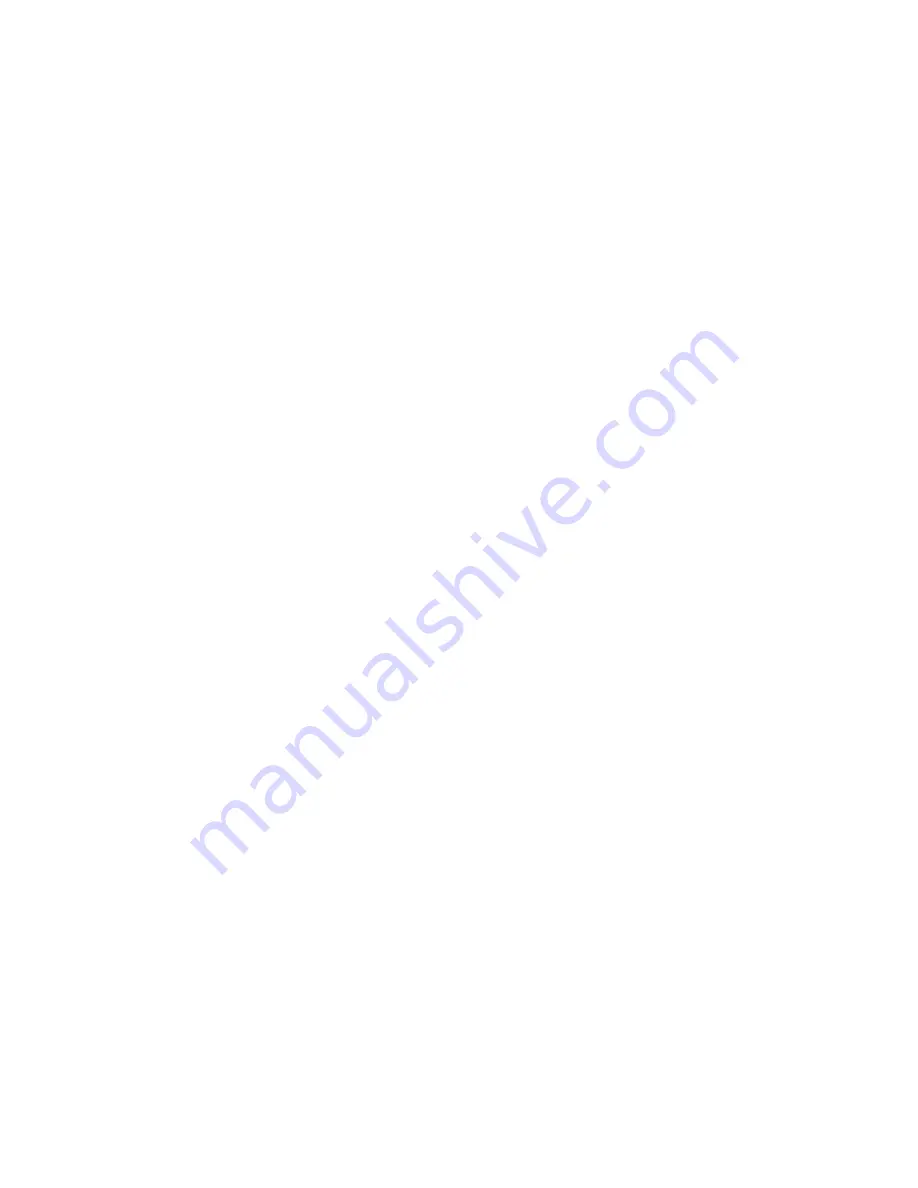
©2003 Maytag Appliances Company
25
16022675
System Diagnosis
Symptoms of Low or High Ambient
Temperature Installation
Lower ambient air temperature reduces the condensing
temperature and therefore reduces the temperature of
the liquid entering the evaporator. The increase in
refrigeration effect due to operation in a lower ambient
results in a decrease in power consumption and run
time. At lower ambients there is a reduction in cabinet
heat leak which is partially responsibile for lower power
consumption and run time.
An increase in refrigeration effect cannot be expected
below a certain minimum ambient temperature. This
temperature varies with the type and design of the
product.
Generally speaking, ambient temperatures cannot be
lower than 55° F. without affecting operating efficiency.
Conversely, the higher the ambient temperature the
higher the head pressure must be to raise the high side
refrigerant temperature above that of the condensing
medium. Therefore, head pressure will be higher as the
ambient temperature raises. Refrigerators installed in
ambient temperatures lower than 55° F. will not perform
as well because the pressures within the system are
generally reduced and unbalanced. This means that the
lower head pressure forces less liquid refrigerant
through the capillary line. The result is the symptoms of
a refrigerant shortage. The lower the ambient
temperature the more pronounced this condition
becomes.
When a point where the ambient temperature is below
the cut-in of the Temperature Control is reached, the
compressor won't run.
Heat Load
A greater heat load can result from the addition of more
than normal supply of foods, such as after doing the
weekly shopping. Other items contributing to an
additional heat load would be excessive door openings,
poor door sealing, interior light remaining on, etc.
An increase in heat being absorbed by the refrigerant in
the evaporator will affect the temperature and pressure
of the gas returning to the compressor. Compartment
temperatures, power consumption, discharge, and
suction pressures are all affected by heat load.
Pressures will be higher than normal under heavy heat
load.