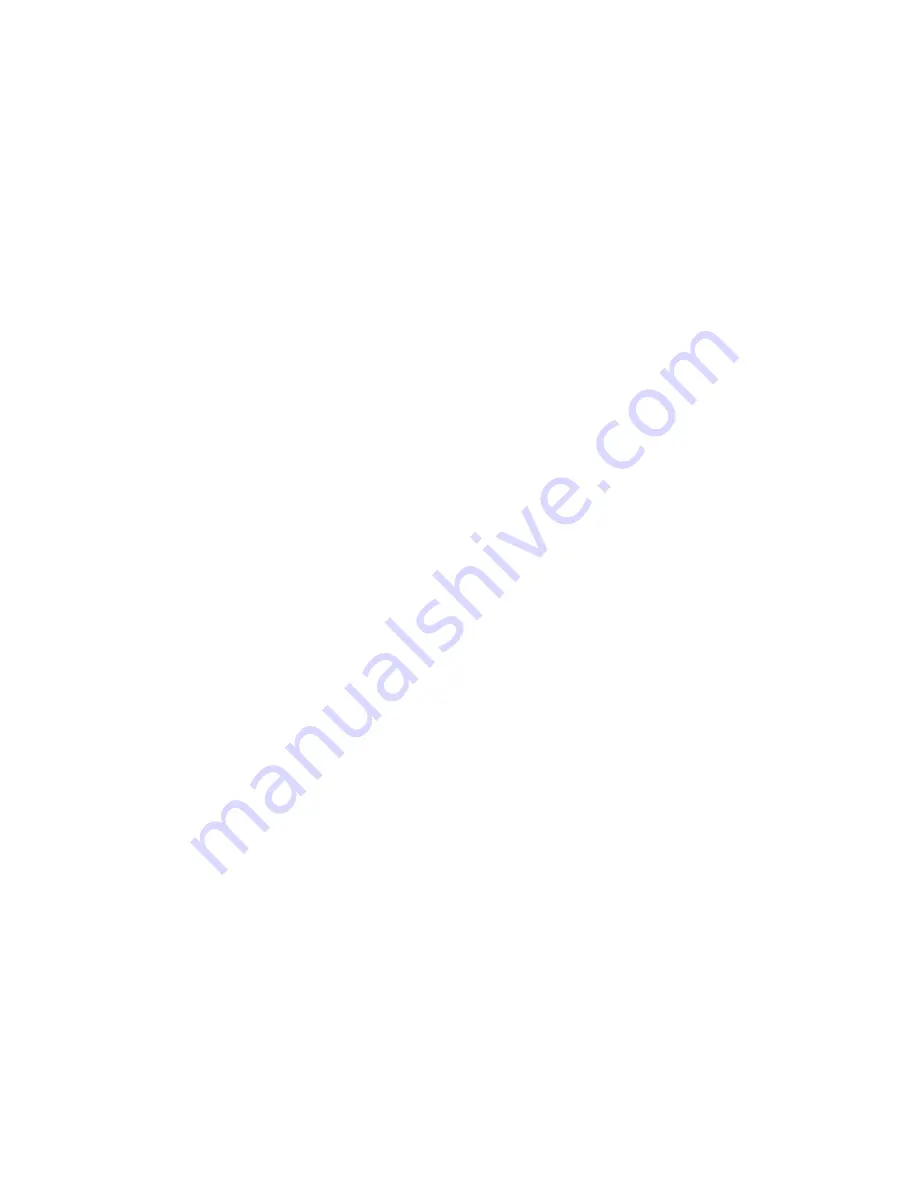
SECTION VII
ROUTINE MAINTENANCE .................................................................................. 35
A. Cleaning ................................................................................................................................... 35
B. Adjustments ............................................................................................................................. 36
C. Lubrication ............................................................................................................................... 36
SECTION VIII
TROUBLESHOOTING ........................................................................................... 37
SECTION IX
PROCEDURE FOR FUNCTIONAL CHECK OF REPLACEMENT
COMPONENTS ....................................................................................................... 44
Optional Exhaust Duct Kit .............................................................................................................. 46
Optional Gas Piping Kit .................................................................................................................. 46