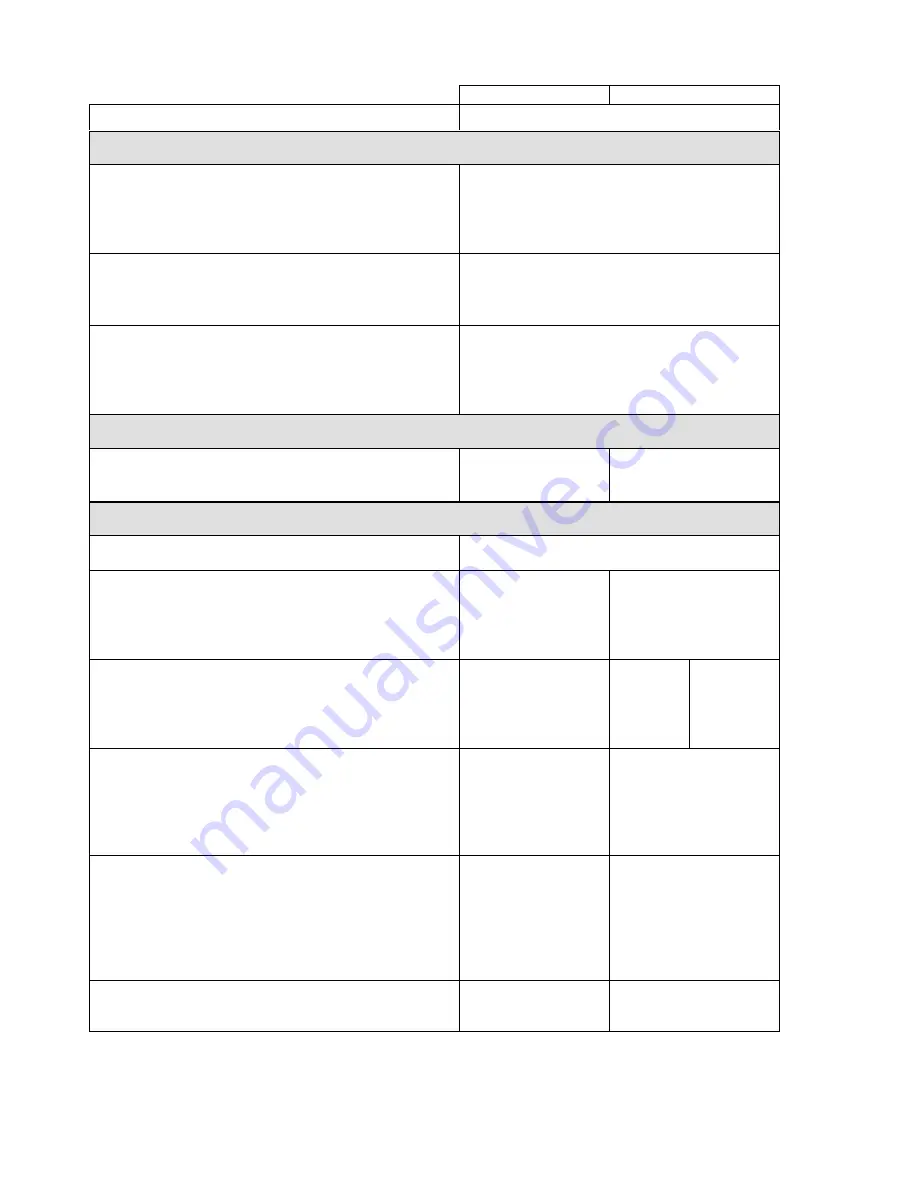
10
INSTALLATION AND MAINTENANCE MANUAL
PUBLICATION DATE 03/02
504 766
3.4. MACHINES 55kg / 125lbs CAPACITY
1-Motor version
2-Motor version
CAPACITY:
55kg / 125lbs
DIMENSIONS
PACKING DIMENSIONS:
width
depth
height
transportation capacity
1430 mm / 56,3“
1750 mm / 68,9“
2105 mm / 82,87“
5,3 m
3
/ 187 ft
3
MACHINE DIMENSIONS:
width
depth
height
1195 mm / 47,04“
1610 mm / 63,4“
1905 mm / 75“
DIMENSIONS OF INNER DRUM:
diameter
depth
drum capacity
door opening
914 mm/ 36“
790 mm / 31,1“
518 dm
3
/ 137 gal
540 mm / 21,3“
WEIGHT
WEIGHT:
netto
brutto
1630 kg / 3594 lbs
1770 kg / 3902 lbs
1626 kg / 3585 lbs
1766 kg / 3894 lbs
ELETRICAL DATA
Permitted deviations of feeding voltage for machines:
±10%, with a maximal standard deviation of the
frequency 1%
Electrical system of the machine:
3x380-480V 50/60Hz
3x200-240V 50/60Hz
3x380-415V 50Hz
3x380V 60Hz
3x440-480V 60Hz
3x220-240V 50Hz
3x208-240V 60Hz
TOTAL INPUT OF THE MACHINE WITH:
electric heating 54 kW
no heating
steam heating
62,7 kW
8,7 kW
8,7 kW
380-440V
3AC:
55,8 kW
8,2 kW
8,2 kW
208-240 V /
480V:
56 kW
8,2 kW
8,2 kW
NOMINAL OUTPUT OF THE MOTOR AT RPM:
washing / distribution
spinning low / high
7,5 kW
7,5 kW
400 V: 1,2 / 1,1 kW
230/480V: 1,4/ 1,2kW
400 V: 5,8 / 4,5 kW
230V: 6,5 / 5 kW
480V: 6,5 / 5,5 kW
INPUT PROTECTION FOR ONE MACHINE:
with electric heating 54 kW (3x230V/60Hz)
with electric heating 54 kW (3x400V/50Hz)
without electric heating (3x400V/ 50 Hz, 3x480 V/ 60 Hz)
with steam heating (3x230 V/60 Hz)
without electric heating (3x230 V / 60 Hz)
with steam heating (3x400 V/50 Hz)
160 A
100 A
32 A
40 A
40 A
32 A
160 A
100 A
25 A
30 A
30 A
25 A
Overload protection of the motor:
eletronic protection
on the frequency
invertor
overcurrent relay
tab. 3.4
*