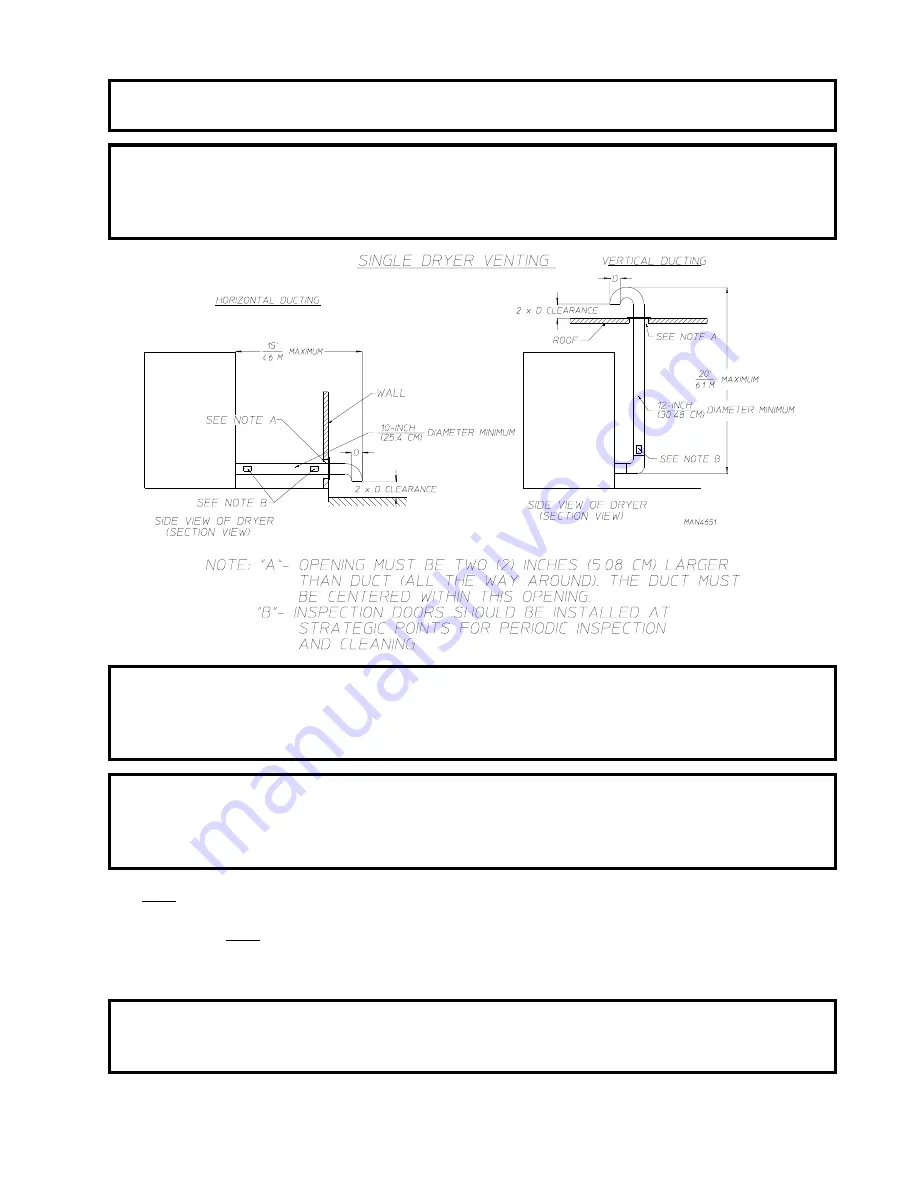
17
IMPORTANT:
Exhaust back pressure measured by a manometer in the exhaust duct
must be
no less
than 0 and
must not exceed
0.3 inches (0.74 mb) of water column.
IMPORTANT:
Minimum duct size for a dryer that is vented vertically is 12-inches (30.48 cm) for a
round duct or an equivalent of 80 square inches (516.1 square centimeters).
THE
DUCT SIZE MUST NOT BE REDUCED ANYWHERE DOWNSTREAM OF
THE DRYER.
IMPORTANT:
For extended ductwork runs, the cross section area of the ductwork can only be
increased to an extent. When the ductwork approaches the maximum limits noted in
this manual, a professional heating, venting, and air conditioning (HVAC) firm
should
be
consulted for proper venting information.
NOTE:
As per the National Fuel Gas Code, “Exhaust ducts for type 2 clothes dryers shall be
constructed of sheet metal or other noncombustible material. Such ducts shall be equivalent in
strength and corrosion resistance to ducts made of galvanized sheet steel not less than
0.0195-inches (26 gauge [0.05 mm]) thick.”
ALL
ductwork
should be
smooth inside with no projections from sheet metal screws or other obstructions,
which will collect lint. When adding ducts, the duct to be added should overlap the duct to which it is to be
connected.
ALL
ductwork joints
must be
taped to prevent moisture and lint from escaping into the
building. Inspection doors
should be
installed at strategic points in the exhaust ductwork for periodic
inspection and cleaning of lint from the ductwork.
NOTE:
When the exhaust ductwork passes through a wall, ceiling, or roof made of combustible
materials, the opening
must be
2-inches (5.08 cm) larger than the duct (all the way around).
The duct
must be
centered within this opening.