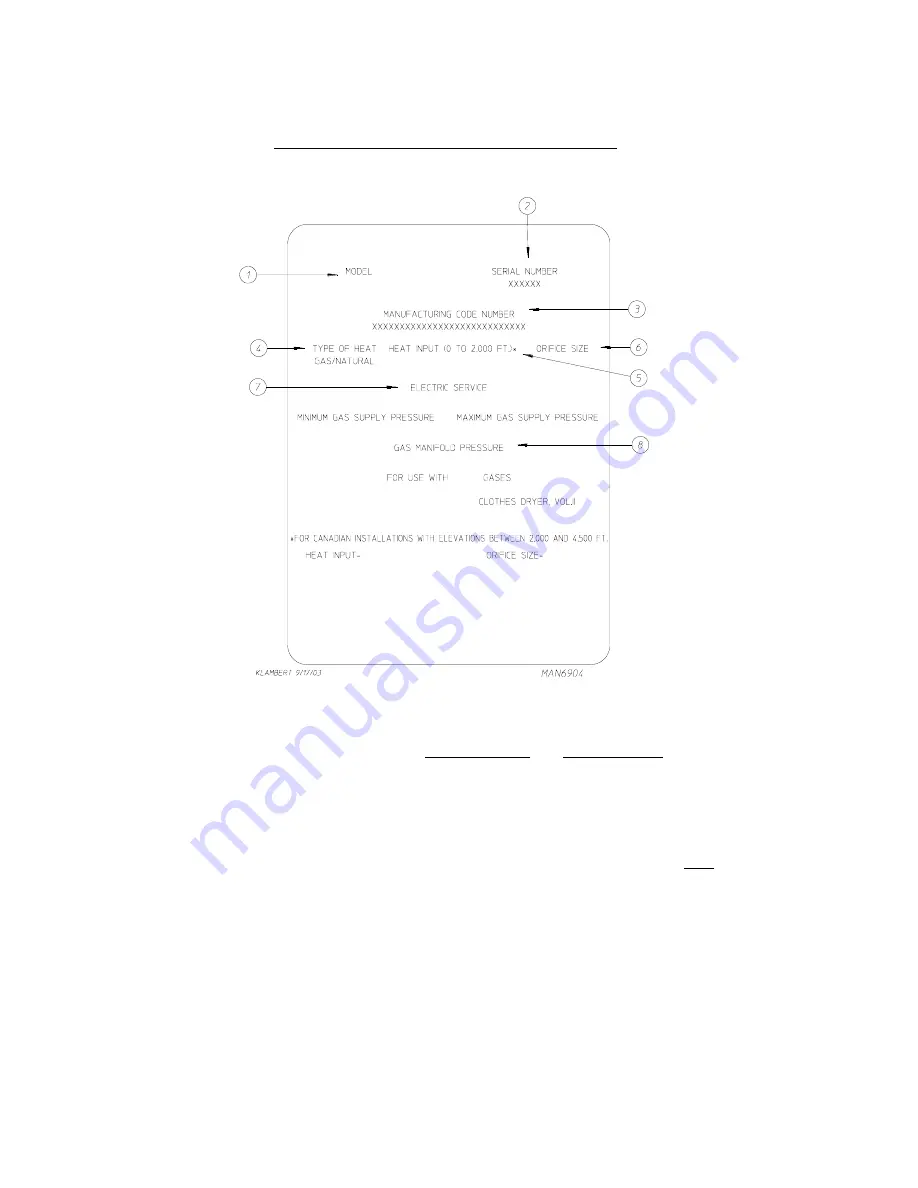
32
SECTION VII
DATA LABEL INFORMATION
When contacting the
Maytag Co
., certain information is required to ensure proper service/parts information.
This information is on the data label affixed to the left side panel area behind the top control (access) door.
When contacting the
Maytag Co.
, please have the
model number
and
serial number
available.
1.
MODEL NUMBER
– Describes the size of the dryer and the type of heat (gas, electric, or steam).
2.
SERIAL NUMBER
– Allows the manufacturer to gather information on your particular dryer.
3.
MANUFACTURING CODE NUMBER
– The number issued by the manufacturer
,
which describes
ALL
possible options
on your particular model.
4.
TYPE OF HEAT
– This describes the type of heat for your particular dryer, gas (either natural gas or liquid propane [L.P.]
gas), electric, or steam.
5.
HEAT INPUT
(for GAS DRYERS) – This describes the heat input in British Thermal Units per Hour (Btu/hr).
6.
ORIFICE SIZE
(for GAS DRYERS) – Gives the number drill size used.
7.
ELECTRIC SERVICE
– This describes the electric service for your particular model.
8.
GAS MANIFOLD PRESSURE
(for GAS DRYERS) – This describes the manifold pressure taken at the gas valve tap.