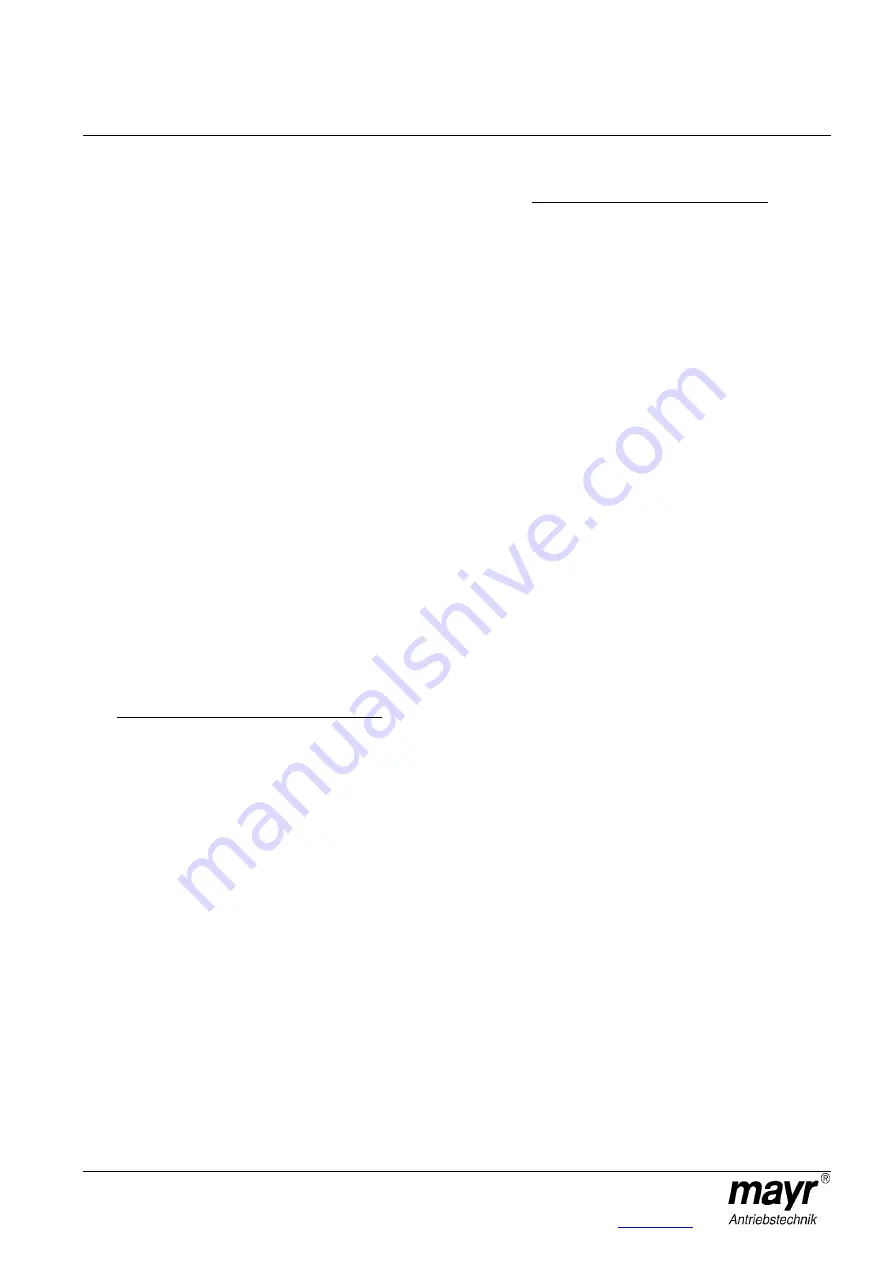
Installation- and Operational Instructions
for ROBA-stop
®
-M Brakes
Type 891. _ _ _ . _ Sizes 2 – 500
(B.8.1.GB)
16/11/2005 TK/KE/RJ
Chr. Mayr GmbH + Co. KG
Tel.: 08341 / 804-0
Eichenstraße 1
Fax: 08341 / 804-421
D-87665 Mauerstetten
http://www.mayr.de
Page 9 of 17
Germany
eMail:
4. Installation conditions
The eccentricity of the motor shaft against the mounting pitch
circle must not exceed 0,2 mm.
The positioning tolerance of the threads for the cap screws (8)
must not exceed 0,2 mm.
The axial eccentricity deviation of the screw-on surface to the
shaft must not exceed the permitted axial eccentricity
tolerance of: 0,08 mm for sizes 2 to 8, 0,1 mm for sizes 16 to
250, and 0,125 mm for size 500, according to DIN 42955
The relevant diameter is the pitch circle diameter for holding
the brakes.
Larger deviations can lead to a lower torque, permanent wear
on the rotor (4) and to overheating.
The tolerances of the hub bore (1) and the shaft are to be
chosen so that the hub gearing teeth (1) are not widened.
Widening the gearing leads to the rotor (4) jamming on the hub
(1), and therefore to brake malfunction.
Recommended hub–shaft tolerance H7/k6.
Do not exceed the maximum permitted join temperature of
200 °C.
The rotor (4) and the brake surfaces must be free of oil and
grease.
You must make use of a suitable counter friction surface (steel
or cast iron). Sharp-edged interruptions of the friction surface
must be avoided. Recommended surface quality in the area of
the contact surfaces Ra = 1,6 µm.
Friction surfaces made out of grey cast iron should be
polished with fine sandpaper (grain = 400)
No friction-value increasing surface manipulation is allowed.
The key connection should be designed according to the
requirements based on the shaft diameter, transmittable
torque and operational conditions. To do this, the relevant data
must be known to the user. The user can also carry out the
design according to the valid basis calculation DIN 6892.
The quality of the hub is to be calculated as follows:
for sizes 2 and 4 with Re = 230 N/mm
2
and
for sizes 8 to 500 with Re = 300 N/mm
2
The length of the key should cover the whole hub.
Please note the usual permitted tensions for mechanical
engineering when measuring the dimensions of the key
connections. Before machine start-up, please check that the
key is inserted correctly and that the brake is mounted with the
correct tightening torque (see Table 2).
5. Installation (Figs. 1 and 2)
5.1. Install the hub (1) onto the shaft and bring it into the correct
position with the length of the key over the entire hub, and
secure it axially (e.g. with a locking ring).
5.2. If necessary (dependent on type), put the friction disc (5) or the
flange plates (12/13) over the shaft until it is lined up against
the machine wall (observe the bore alignments in the friction
disc (5) or flange plates (12/13) and the threaded bores in the
machine wall).
5.3. Measure the rotor thickness and compare with the values in
Tables 4/5. Push the rotor (4) by hand onto the hub (1) (the
rotor collar should be facing away from the machine wall, the
friction disc (5), or the flange plates (12/13).
The whole length of the rotor gearing must lie on the hub (1).
Please make sure that the gearing runs easily.
Do not cause damage!
5.4. If necessary, install the hand release (see Point 8).
5.5. If necessary (dependent on type), insert the O-ring (11) in the
axial recess of the coil carrier (2).
5.6. Push the rest of the brake over the hub (1) and the rotor collar
(4) (the fixing bores should be aligned with the bores in the
friction disc (5), flange plates (12/13) or machine wall).
The shoulder screws (10 / Fig. 1) prevent the individual parts
falling apart.
They do not affect the brake function and must NOT be
removed on installation.
5.7. Secure the complete brake all round using the cap screws (8)
and the manufacturer-side flat sealing rings (9 / dependent on
type). Use a torque wrench and the tightening torque (see
Table 2).