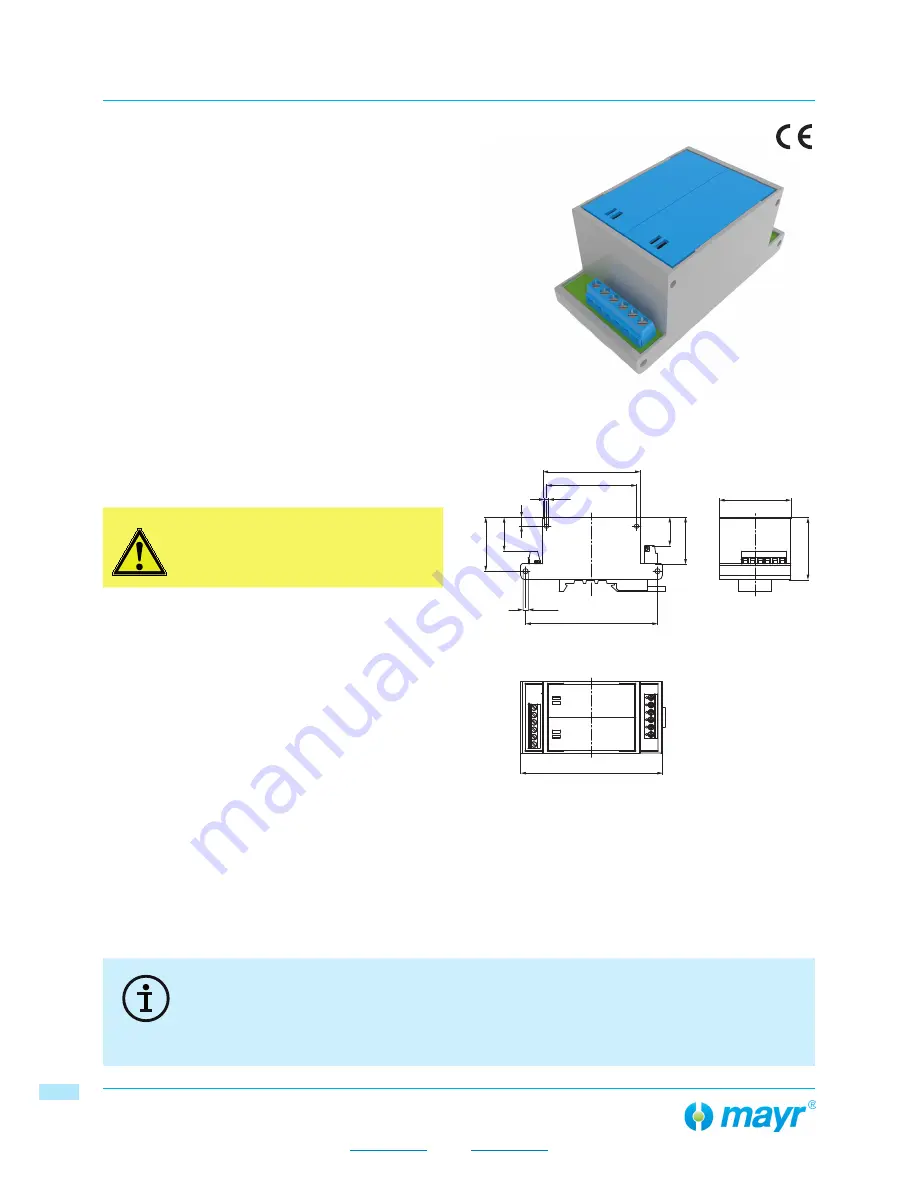
Installation and Operational Instructions for
ROBA
®
-brake-checker plus DC Type 028.600.2
(B.0286002.EN)
your reliable partner
02/10/2018 TF/GF
Page 2 of 10
Chr. Mayr GmbH + Co. KG
Eichenstraße 1, D-87665 Mauerstetten, Germany
Tel.: +49 8341 804-0, Fax: +49 8341 804-421
www.mayr.com
, E-Mail:
22
Function
The ROBA
®
-brake-checker plus DC monitoring module
is intended for use with an input voltage of 24 VDC. The
monitoring module monitors the movement of the armature
disk and emits the determined switching condition via
control terminal (signal output).
Critical conditions (line breakages, wear, excess temperatu-
re) can be recognised and the respective signal can be emit-
ted via control terminal (error output).
It is possible to select between fast and slow disconnection
via the input F/S on the control terminal.
Louder switching noises are generated on the brakes in
case of fast switch-off than in case of slow switch-off.
The movement detection feature of the armature disk is
based on the detection of electromagnetic changes in the
brake. If, due to unfavourable external influences, the secu-
red detection cannot be ensured, it is possible that the
signal and error outputs do not correspond to the expected
state (plausibility).
Dimensions
(mm)
CAUTION
The ROBA
®
-brake-checker with integrated
DC-side disconnection is not suitable for
being the only safety disconnection in
applications!
66
48.4
61
89.4
5.6
31.5
19.3
36.5
22.8
6
42.3
20
96
Ø3
Ø3.5
20
Application
ROBA
®
-brake-checker plus DC monitoring modules are
used to supply permitted ROBA
®
-stop safety brakes.
Motion monitoring of the armature disk for released ROBA-
stop
®
safety brakes is possible.
Monitoring module ROBA
®
-brake-checker DC
•
Consumer operation with overexcitation and/or power
reduction
• Controlled output voltage (on reduction)
• Automatic reduction to holding voltage U
H
• Fast or slow disconnection
• Armature disk motion recognition
(release and drop-out
recognition)
• Preventative function monitoring (wear recognition and
error recognition, functional reserve)
• Continuous drop-out recognition
• Maximum output current I
RMS
= 5 A
• Maximum overexcitation current I
O
= 16 A
• Safe monitoring of the switching times (optional)
The use of the ROBA
®
-brake-checker in combination with brakes of other manufacturers is not intended and
expressly not approved by mayr
®
power transmission.
In these cases, operation is at your own risk,
the guarantee and service and support provided by mayr
®
power transmission no longer apply.
22