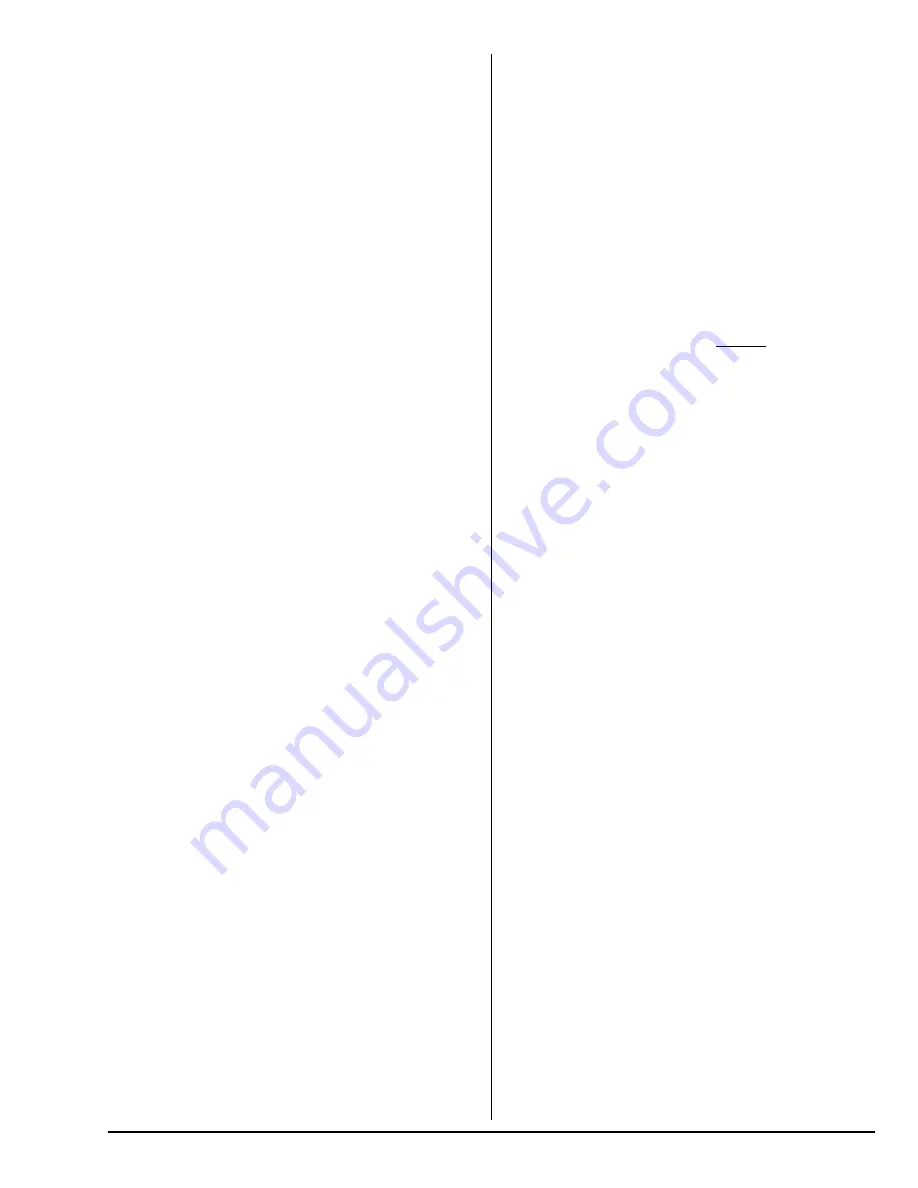
113257-4
23
NOTE:
Lint drawer must be all the way in place to activate
safety switch otherwise the dryer will not start.
Rotate the tumbler by hand to be sure it moves freely.
Check bolts, nuts, screws, terminals, and fittings for security.
STEAM MODELS – check to ensure air supply (80 psi [5.51
bar, 551 kPa]) is on all dryers equipped with standard
pneumatic steam damper system.
STEAM MODELS – check to ensure all steam shutoff valves
are open.
STEAM MODELS with Standard Pneumatic Damper – check
steam damper operation.
STEAM MODELS with Optional Steam Solenoid Valve –
Check steam solenoid valve connections.
Check tumbler bearing setscrews to ensure they are all tight.
Preoperational Test __________________
All dryers are thoroughly tested and inspected before leaving
the factory. However, a preoperational test should be
performed before the dryer is publicly used. It is possible
that adjustments have changed in transit or due to marginal
location (installation) conditions. Installer must instruct the
user on how to correctly operate the dryer before leaving.
Turn on electric power to the dryer.
Make sure the main door is closed and the lint drawer is
securely in place.
Refer to the Operating Instructions for starting your particular
model dryer.
Check to ensure that the tumbler starts in the clockwise
direction. Additionally, check the direction of the blower motor
(impellor/fan) to ensure that the blower motor (impellor/fan)
rotates in the clockwise direction as viewed from the front. If
it is, the phasing is correct. If the phasing is incorrect, reverse
two of the leads at L1, L2, or L3 of the power supply
connections made to the dryer.
IMPORTANT:
Dryer blower motor/pulley that drives the
impellor/fan when viewed from the back of the dryer must
turn in the counterclockwise direction, otherwise the dryer
efficiency will be drastically reduced and premature
component failure can result.
Heat Circuit Operational Test
Gas Models
When the dryer is first started (during initial start-up), the
burner has a tendency not to ignite on the first attempt. This
is because the gas supply piping is filled with air, so it may
take a few minutes for this air to be purged from the lines.
The dryer is equipped with a DSI system, which has internal
diagnostics. If ignition is not established after three attempts,
the heat circuit DSI module will LOCKOUT until it is manually
reset. To reset the DSI system, open and close the main
door and restart the dryer (press the “START” key).
NOTE:
During the purging period, check to be sure that all
gas shutoff valves are open.
Once ignition is established, a gas pressure test should be
taken at the gas valve pressure tap of each dryer to ensure
that the water column pressure is correct and consistent.
NOTE:
Water column pressure requirements (measured at
the gas valve pressure tap):
Natural Gas ............... 3.5 in WC (8.7 mb, 0.87 kPa).
L.P. Gas ................. 10.5 in WC (26.1 mb, 2.61 kPa).
IMPORTANT:
There is no regulator provided in an L.P.
dryer. The water column pressure must be regulated at
the source (L.P. tank) or an external regulator must be
added to each dryer.
Steam Models
Check to ensure that the (standard) steam damper or
(optional) steam solenoid valve is functioning properly.
The steam damper should not “slam” (open or closed) when
it reaches the end of (piston) travel. Additionally, the steam
damper should not bind and/or stop during travel. If either of
these conditions occur, the flow control must be adjusted.
Refer to the bottom illustration on
instructions.
Make a complete operational check of all safety related
circuits (i.e., lint drawer switch and sail switch on gas models).
NOTE:
To check for proper sail switch operation, open the
main door and while holding main door switch plunger in,
start the dryer. The dryer should start but the heat circuit
should not be activated (on). If the heat (burner) does
activate, shut the dryer off and make the necessary
adjustments.
Reversing tumbler dryers should never be operated with less
than a 79 lb (35.4 kg) load (dry weight), since the load’s weight
affects tumbler coast time during a direction reversal
command. It is important that the tumbler come to a complete
stop prior to starting in opposite direction.
Microprocessor Controller (Computer)
Dryer Models
Spin and dwell (stop) times are not adjustable in the Automatic
Mode and have been preprogrammed into the microprocessor
controller (computer) for 150-seconds spin time in the forward
direction and 120-seconds in the reverse direction with a
5-second dwell (stop) time.
Spin and dwell (stop) times are adjustable in the Manual
(timed) Mode.
Tumbler Coating
The tumbler is treated with a protective coating. We suggest
dampening old garments or cloth material with a solution of
water and nonflammable mild detergent and tumbling them
in the tumbler to remove this coating.
Each dryer should be operated through one complete cycle
to ensure that no further adjustments are necessary and that
all components are functioning properly.
Make a complete operational check of all operating controls.
Each microprocessor controller (computer) has been
preprogrammed by the factory with the most commonly used
parameter (program) selections. If computer changes are
required, refer to the computer programming manual, which
was shipped with the dryer.
Summary of Contents for MAXI120
Page 30: ...Part No 113257 4 10 07 14...