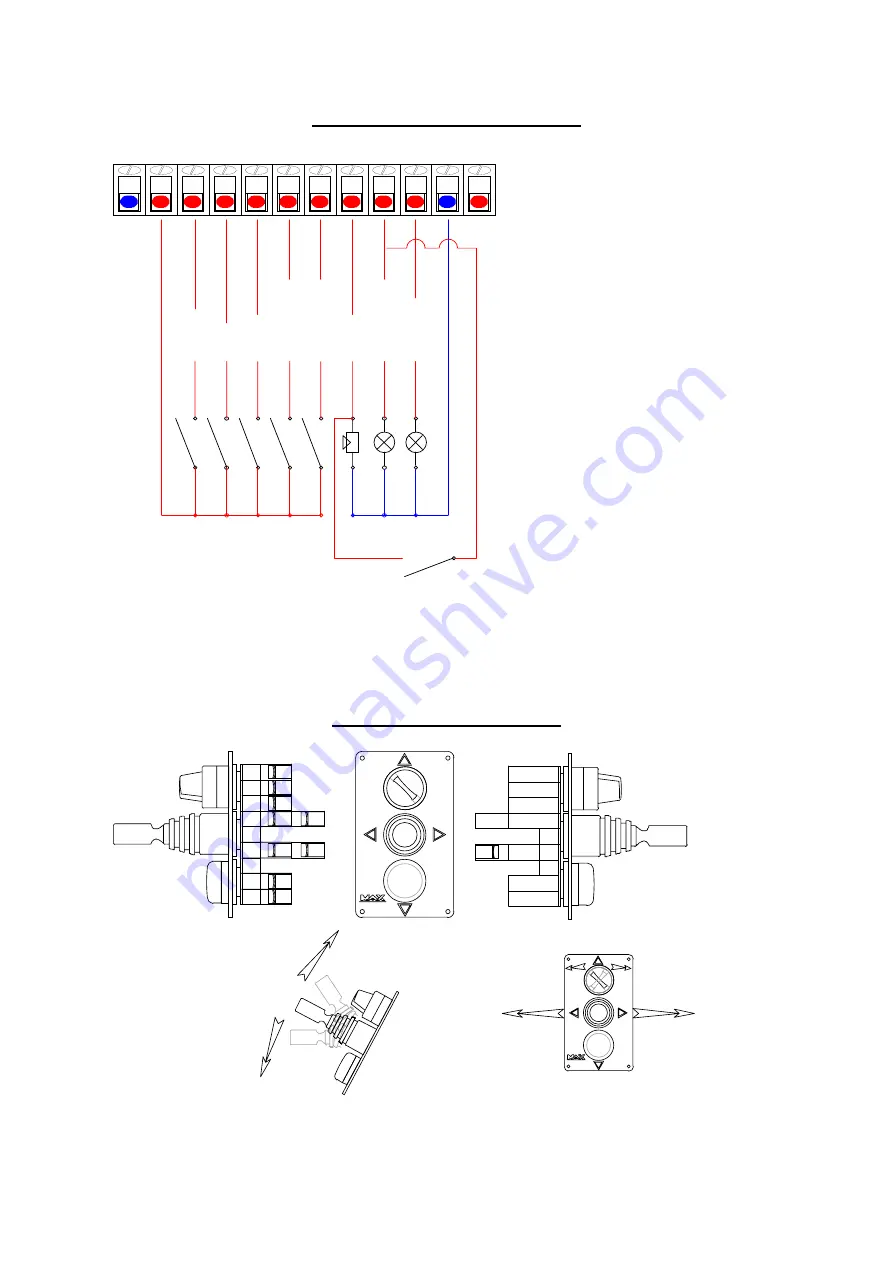
MAX POWER
Foot Switch/Custom Control Panel
ON / OFF
RAISE
LOWER
LEFT THRUST
RIGHT THRUST
ALARM
GREEN LIGHT
RED LIGHT
1
2
12
13
14
15
16
17
18
19
1
2
- + + + + + + + + + - +
All control switches used should be of
N/O momentary push button type with
the exception of the on/ off which should
be of switching type
Any N/O switches or sensors can be used for
complementary alarms at will
Foot switch /custom control panel
Standard R300 Control Panel
12
19
1
2
18
17
15
16
13
14
POWER
POWER
Pushing the joy stick up
raises the thruster .
Pushing the joy stick down
lowers the thruster .
Turning the switch to the
right renders the control
panel active
Turning the switch to the
left disables the control
panel
Pushing the joy stick to
the left moves the yacht
to the left.
Pushing the joy stick to
the right moves the yacht
to the right
The red turn button illuminates
when the thruster is up and
locked .
The green light illuminates
when the thruster is down and
ready to function .
27
INSTALLATION MANUAL RETRACT R 300