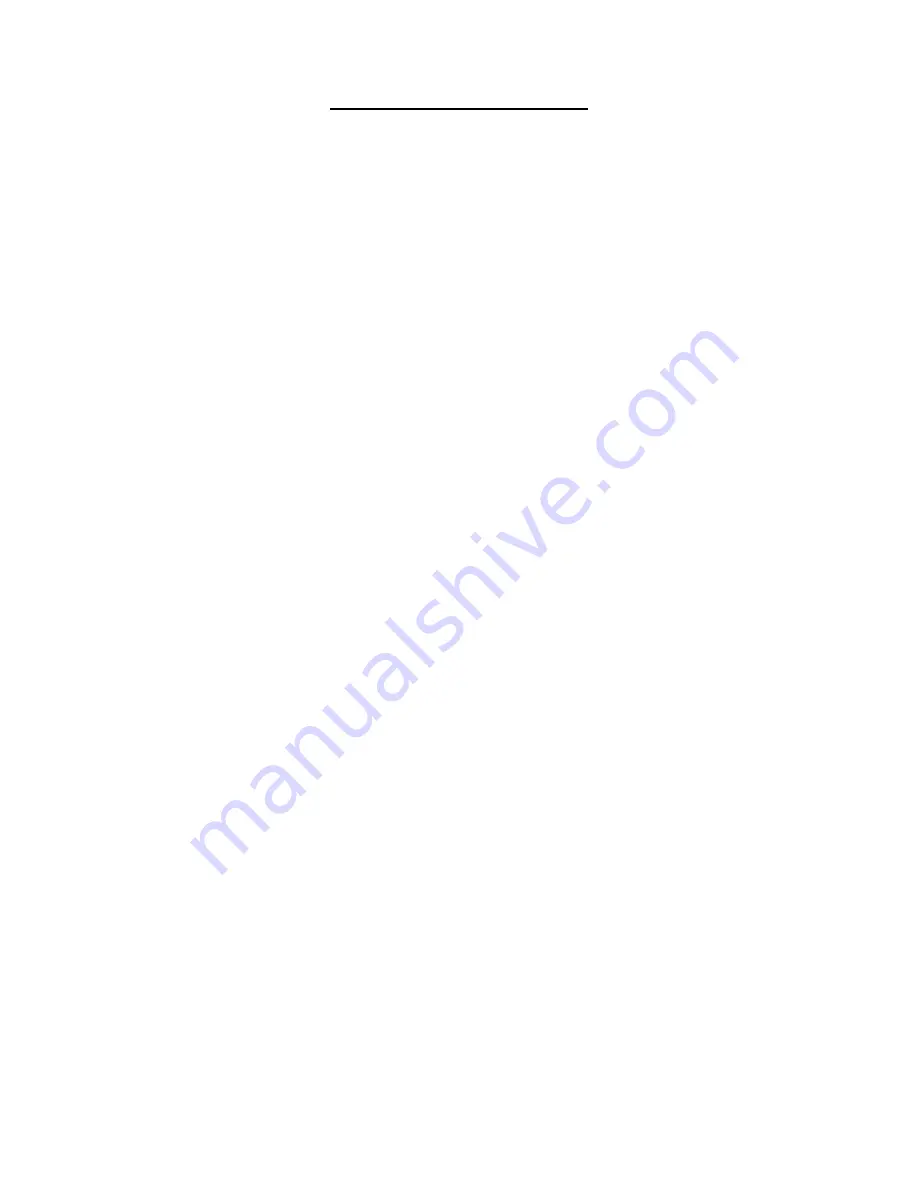
Max-Ox™ MX-900B Operators Manual, Rev. 0
Page 5 of 54
MX-900B Operators Manual
Codes and Insurance Notice
The Max-Ox™ MX-900B Commercial Wood-chip Fired Hydronic Boiler is
a mechanical draft, direct-vented,
NON-PRESSURIZED VESSEL,
solid
fuel burning appliance. It must be installed in accordance with this Manual,
NFPA 211, Federal, State, and Local codes, and your Insurance
Underwriter’s requirements.
Local building code enforcement officials and fire inspectors are given
authority to determine if specific installations of solid fuel burning
appliances are safe. These professionals use recommended guidelines from
various nationally recognized organizations, such as the National Fire
Protection Association (NFPA), and the National Electrical Manufacturer’s
Association (NEMA).
Please be sure to follow the requirements of the Authority Having
Jurisdiction over your specific installation.
Your Insurance Underwriter may also have specific guidelines with respect
to installation and inspection requirements for your solid fuel burning
appliance.