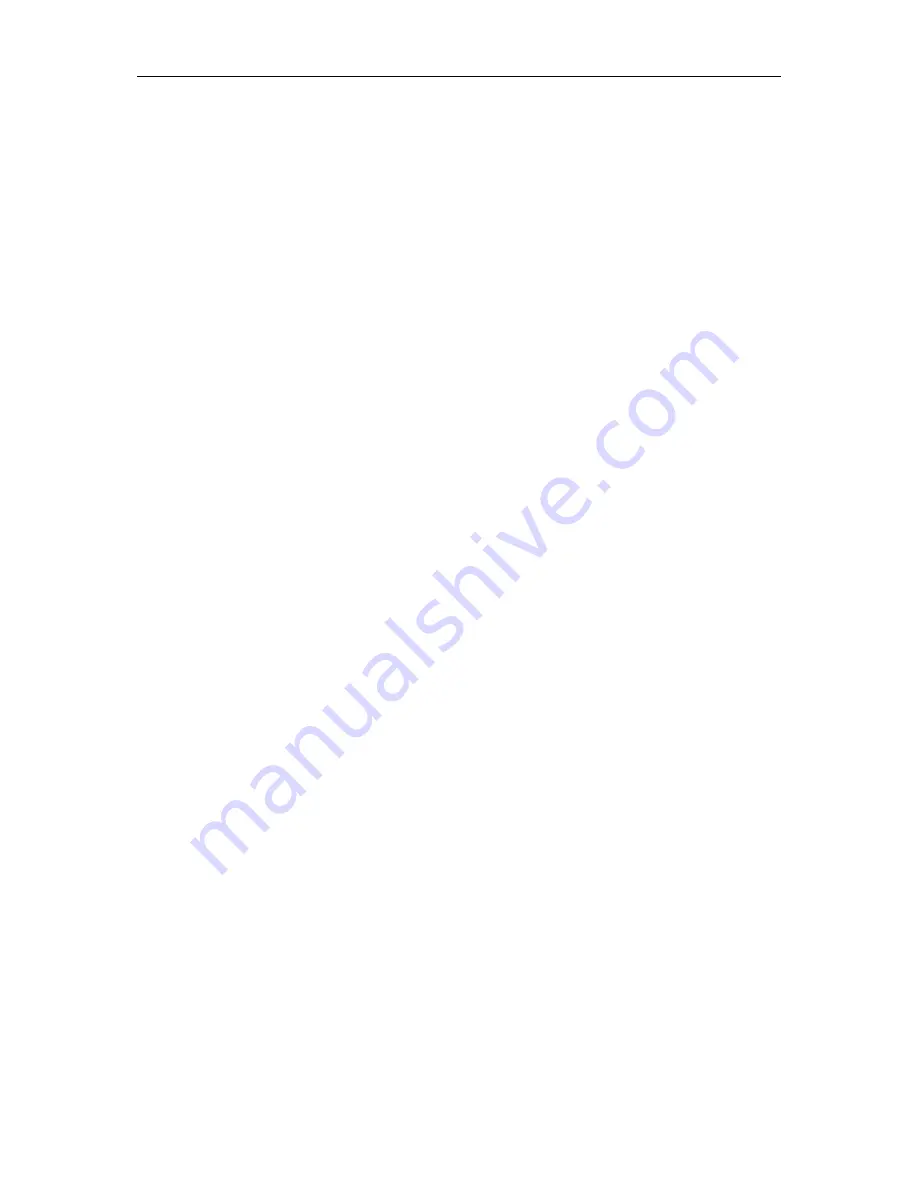
SAFETY
5
§1.3 Knowledge of Electric and Magnetic Fields
Electric current flowing through any conductor causes localized Electric and Magnetic Fields
(EMF). The discussion on the effect of EMF is ongoing all the world. Up to now, no material
evidences show that EMF may have effects on health. However, the research on damage of EMF
is still ongoing. Before any conclusion, we should minimize exposure to EMF as few as possible.
In order to minimize EMF, we should use the following procedures:
Route the electrode and work cables together – Secure them with tape or sleeve.
All cables should be kept as far away from the operator as possible.
Never coil the power or earth cables around operator body.
Connect the work cable to the workpiece as close as possible to the area being welded.
The people with heart-pacemaker should be away from the welding area.