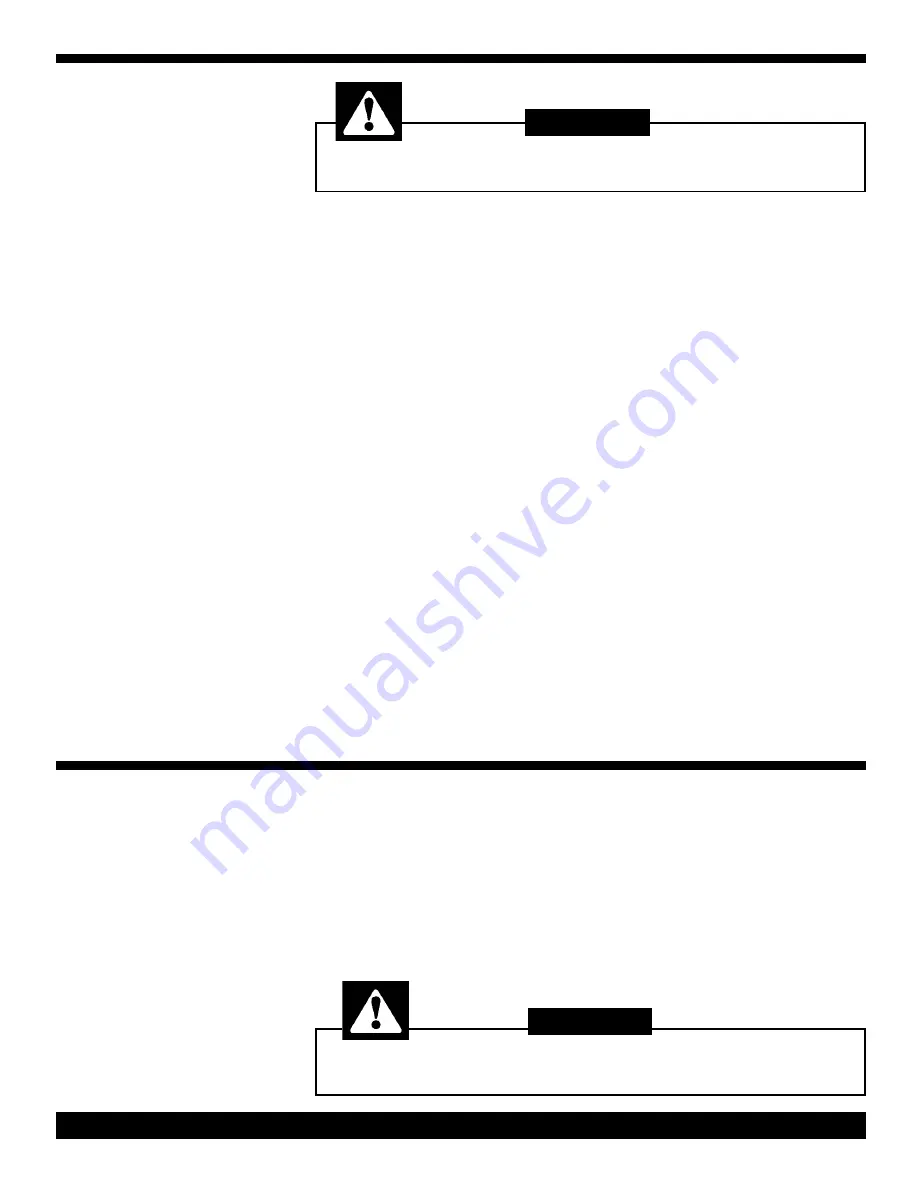
This burnisher can be used in conjunc-
tion with any of the ultra high speed
chemical systems. It is mandatory, how-
ever, that the floor be prepared as direct-
ed by the chemical manufacturer. This
will eliminate a possibility of damage to
floor due to the burnishers high speed.
The burnisher is pre-set at the factory for
use with a 1" thick buffing pad
(1 shpd
w/unit)
. The rougher hair surface is pre-
ferred for high luster floor finishing.
1)
Before operating this burnisher,
check to see that the buffing pad is
properly centered on driver and that
center pad lock is tight on pad.
2)
When operating the burnisher it
MUST
be kept moving, as holding
machine stationary while running will
result in damage to floor and floor finish.
3)
Begin operating the burnisher at the
closest point to your electrical outlet and
work away from the outlet. This will pre-
vent running over the electric cord.
4)
Operate the burnisher in a straight-
line path and avoid continuous operation
in one spot.
5)
Never leave burnisher resting on buff-
ing pad for an extended period of time.
This will cause buffing pad to lose its
normal shape, causing wobbling or
vibration and pad must be replaced.
Also, replace pad if glazed, clogged, torn
or shredded.
6)
The rear wheels on the burnisher are
factory-set for low amp rating and high
luster burnishing with buffing pad. See
instruction sheet.
7)
A carbon brush wear indicator warn-
ing light is located on the motor canopy.
When lit, motor carbon brushes must
be replaced within 20 hours running
time to prevent damage to motor. See
instruction sheet.
If burnisher wobbles, vibrates or pulls,
follow these instructions:
1)
This burnisher is factory adjusted and
set to operate between 13.2 and 14
amps.
2)
Never leave burnisher resting on floor
pad overnight. This will cause the pad to
lose its normal shape, causing wobbling
and vibration. Check pad for unevenness
and change is necessary.
3)
Before turning burnisher on, run tip
of finger between outside of pad and
floor. The outer ring face should be in full
contact with the floor in order for high
speed buffing to be most effective. If
necessary change pad.
4)
If steps 2 and 3 do not correct the
problem, a certified technician should
reset rear wheels, of the burnisher as
follows:
Untighten the allen bolts #422924,
located in the back of the burnisher on
the outrigger. The body is raised when
the bolt is turned to the right and low-
ered when turned to the left.
If the Burnisher Has:
Forward Pull:
Raise left side only
Backward Push:
Raise right side only
Right Pull:
Lower Both sides
equally
Left Pull:
Raise both sides
equally
After adjustments have been made the
technician must check the amp draw
keeping it within the 13.2 - 14 amp,
factory specifications. Failure to do so
may cause the unit to draw excessive
current and damage the burnisher.
O
PERATING
I
NSTRUCTIONS
This burnisher is NOT a low speed floor machine.
DO NOT use the burnisher for stripping or sanding of floors.
C
AUTION
:
To avoid fire, DO NO use with a flammable or combustible
liquid to clean a floor.
W
ARNING
:
C
ARBON
W
EAR
W
ARNING
L
IGHT
This burnisher is equipped with a carbon
brush wear indicator warning light, locat-
ed in the motor canopy facing the opera-
tor. The instructions on the top surface
of the motor canopy read as follows:
When the lamp is lit, the Motor Carbon
Brushes must be replaced within 20
hours of service to prevent damage to the
motor.
Carbon Brushes Part Nos:
Imperial Motor
: Part No 386790 (4)
Ohio Motor*
: Part No 380083 (3)
& 316954 (1)
*
Burnishers with Ohio Motors have "X" after
the serial number.
Note:
After replacing the second set of car-
bon brushes, the commutator of the armature
may need to be undercut and the mica slotted.
This should be done by an experienced motor
repair shop.
P
AGE
4