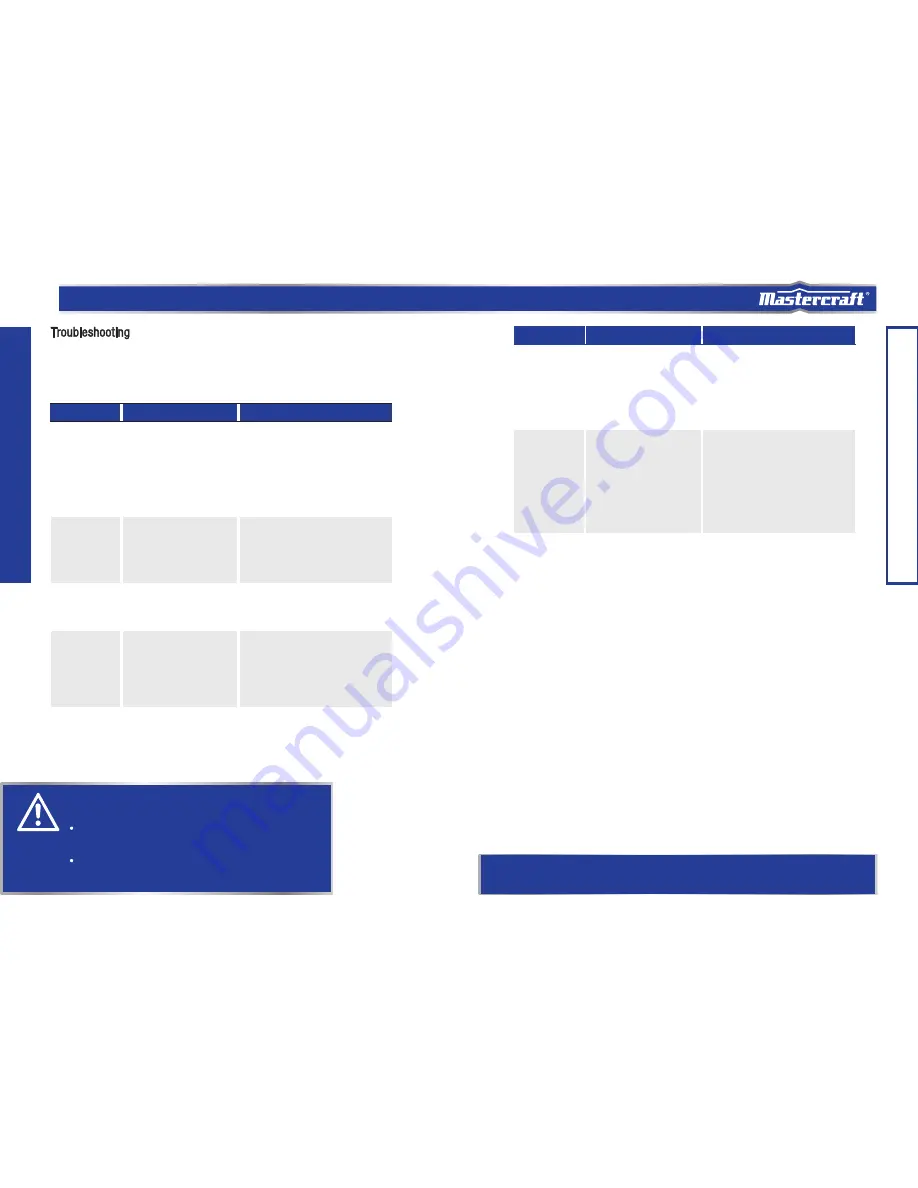
21
20
Note:
For further repair information, please call 1-800-689-9928.
DANGER!
Potential hazard that will result in serious injury or death .
The following chart lists common issues and solutions. Please read it carefully and
follow all instructions carefully.
Air leakage at the
top of the tool or in
the trigger area.
The tool does not
operate properly - it
does not drive the
nails or operates
sluggishly.
The tool skips nails.
The tool jams.
Air leakage between
the bottom and the
cylinder cap.
Air leakage near the
bottom of the tool.
O-rings in the trigger valve are
damaged.
The trigger valve heads are
damaged.
Trigger valve stem, seal, or
O-rings are damaged.
The screws are loose.
The O-rings or the bumper are
worn or damaged.
The screws are loose.
The O-rings or the seals are worn
or damaged.
1.
2.
3.
1.
2.
3.
4.
1.
2.
3.
1.
2.
Tighten the screws.
Inspect and replace the O-rings or the seals.
1.
2.
Tighten the screws.
Inspect and replace the O-rings or the
bumper.
1.
2.
1.
2.
Inspect and replace the O-ring.
Inspect and replace trigger valve heads.
Inspect and replace the trigger valve stem,
seal, or O-ring.
Disconnect the tool from the air supply before making any adjustments.
If any of the following symptoms appear while the tool is in use,
turn it off and disconnect it from the air supply immediately.
Failure to comply will lead to serious injury or death.
Repairs must be performed by a qualified service technician
only.
PROBLEM
POSSIBLE CAUSES
SOLUTIONS
PROBLEM
POSSIBLE CAUSES
SOLUTIONS
The nails are being
driven too deep.
The bumper is worn.
The air pressure is too high.
The depth adjustment knob is not
adjusted properly.
1.
2.
3.
1.
2.
3.
Replace the bumper.
Adjust the air pressure.
Adjust the depth setting by turning the depth
adjustment knob counterclockwise (see
section “Adjusting nail depth” for more
detailed instructions).
The air supply is inadequate.
Lubrication is inadequate.
The O-rings or seals are worn or
damaged.
The exhaust deflector in the
cylinder head is blocked.
1.
2.
3.
4.
5.
1.
2.
3.
4.
1.
2.
3.
4.
The bumper is worn or the spring
is damaged.
There is dirt in the front plate.
Nails cannot move freely in the
magazine due to dirt or wear.
The O-ring on the piston is worn
or dry or lubrication is insufficient.
The cylinder cover seal Is leaking.
Improper nails are used, or nails are
damaged.
The driver guide is damaged or worn.
The magazine screw is loose.
There is dirt in magazine.
1.
2.
3.
4.
Verify that the air supply is adequate.
Pour up to 6 drops of oil into the air inlet.
Inspect and replace O-rings or seals.
Replace the damaged internal parts.
1.
2.
3.
4.
5.
Replace the bumper or spring.
Clean the drive channel on the front plate.
Clean the magazine.
Replace the O-ring.
Replace the sealing washer.
Use proper nails.
(see section “Clearing a jammed nail.”)
Inspect and replace the driver.
Tighten the magazine.
Open and clean the magazine.
TROUBLESHOOTING
TROUBLESHOOTING
model no. 058-8691-0 | contact us 1-800-689-9928