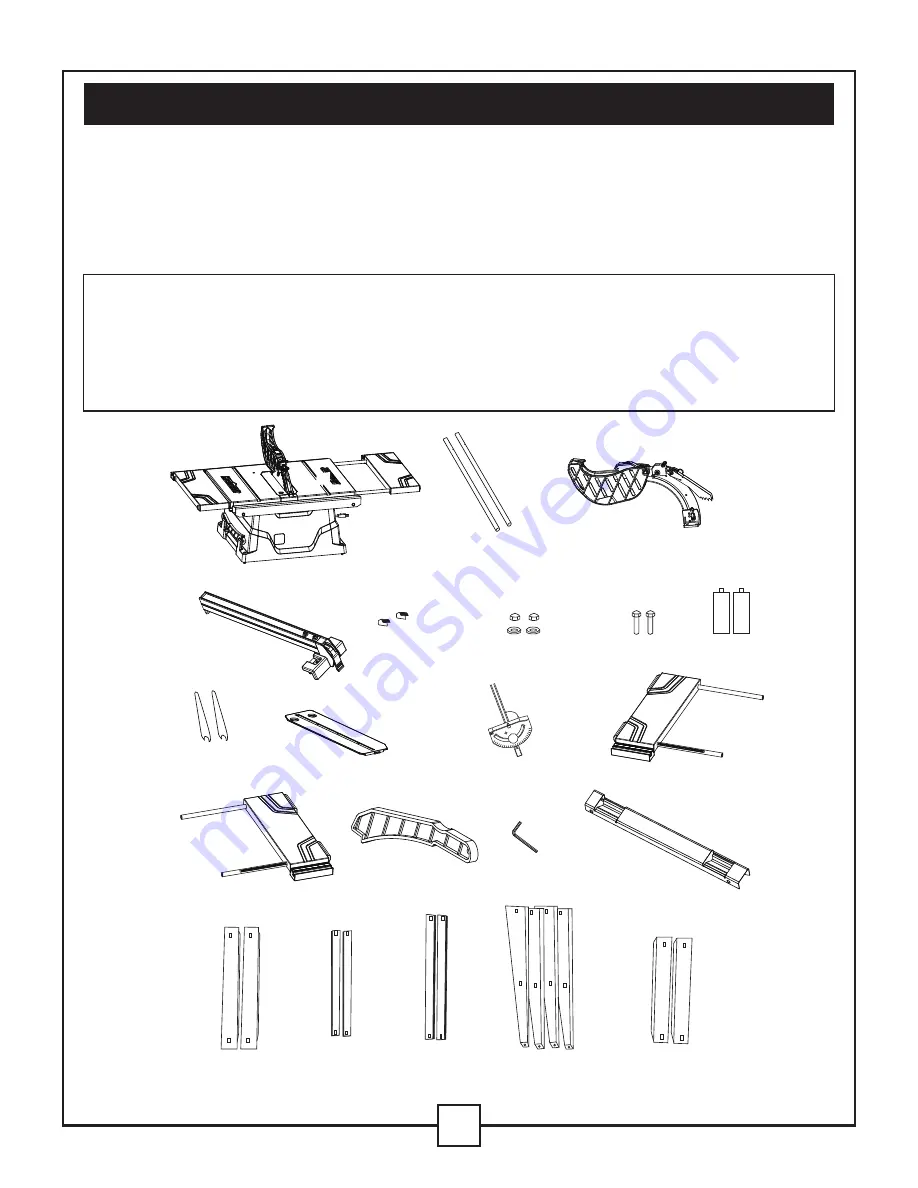
9
V. Assembly and adjustments
UNPACKING
1. Carefully remove the table saw from the carton.
2. Separate the parts.
3. Lay out all of the parts, and check them against the parts listed below. Examine all of the parts
carefully.
WARNING:
• IF
ANY PART
IS MISSING OR DAMAGED, DO NO
T
PLUG IN
THE TABLE SA
W UNTI
L
YOU H
A
VE REPLACED
THE MISSING OR DAMAGED
PARTS. CALL THE T
OL
L
FREE
HELPLINE
AT
1-800-689-9928 FOR MORE INFORM
A
TION.
•
T
O
A
VOID INJU
RY,
THE STYROFOAM BLOCK SHOULD BE REMOVED BETWEEN
THE MO
T
OR
AND
THE TABLE.
Table saw assembly
Rear table extension
tubes
Rip fence
Locating seats
Blade
wrenches
Dado table insert
Right table
extension fence
Push sticker
Hex key
Rear table
extension
Long top leg
brackets
Short bottom
leg brackets
Long bottom
leg brackets
Stand legs
Short top leg
brackets
Mitre gauge
Left table
extension fence
Flat washers
and dome nuts
Hex bolts Batteries
Blade guard and
splitter
30
45
60
75
75
90
60
45
30