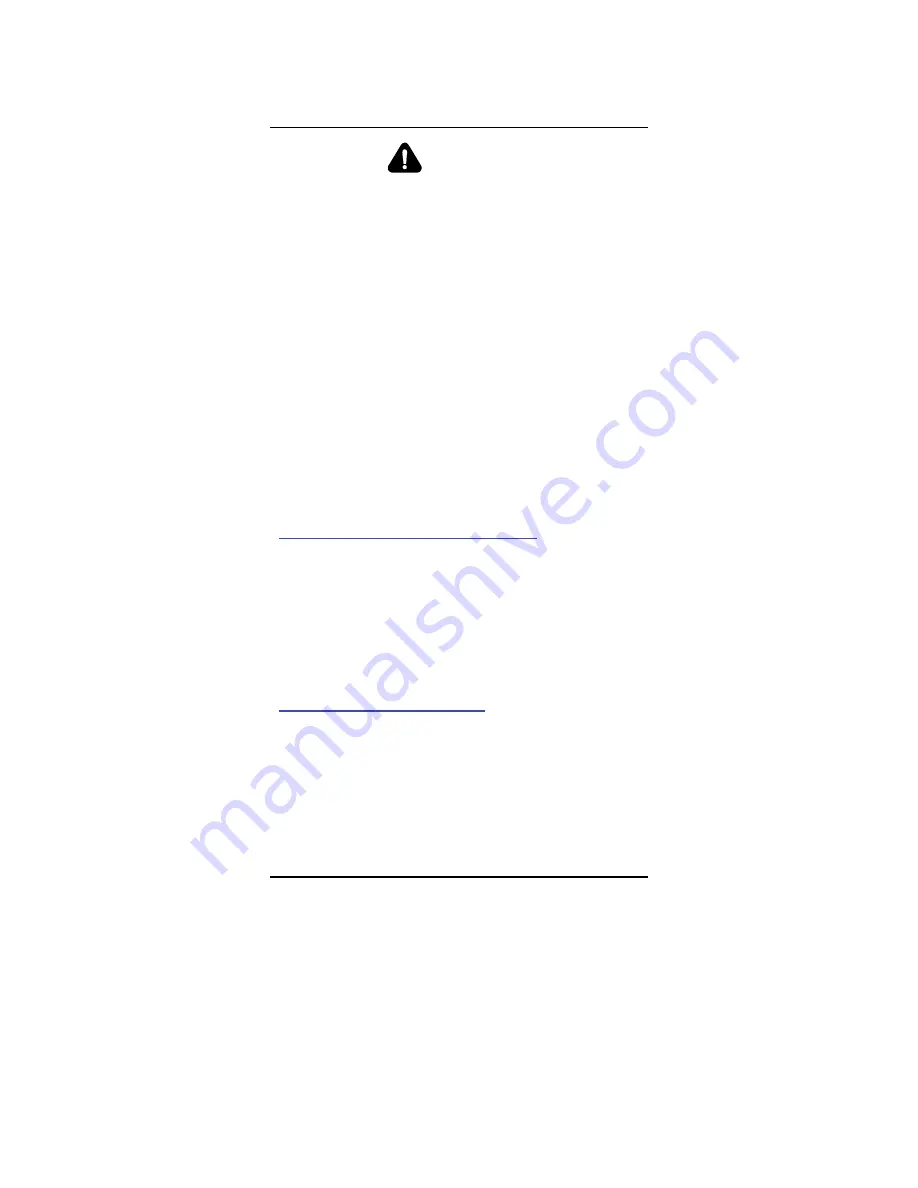
The original language of this publication is English.
WARNING
California Proposition 65
Breathing diesel engine exhaust exposes you
to chemicals known to the State of California
to cause cancer and birth defects or other
reproductive harm.
•
Always start and operate the engine in a
well-ventilated area.
•
If in an enclosed area, vent the exhaust to
the outside.
•
Do not modify or tamper with the exhaust
system.
•
Do not idle the engine except as
necessary.
F o r
m o r e
i n f o r m a t i o n ,
g o
t o
Batteries, battery posts, terminals, and
related accessories can expose you to
c h e m i c a l s , i n c l u d i n g l e a d a n d l e a d
compounds, which are known to the State of
California to cause cancer and birth defects or
other reproductive harm. Wash hands after
handling. For more information, go to
www.P65warnings.ca.gov
California Spark Arrestor
Operation of this equipment may create
sparks that can start fires around dry
vegetation. A spark arrestor may be required.
The owner/operator should contact local fire
agencies for laws or regulations relating to fire
prevention requirements.
r
Reference
Only
Summary of Contents for National Crane 800D
Page 1: ...Operator and Service Manual National Crane 800D F o r R e f e r e n c e O n l y ...
Page 4: ...F o r R e f e r e n c e O n l y ...
Page 252: ...SCHEMATICS 800D 2 Published 5 27 2018 Control 039 06 F o r R e f e r e n c e O n l y ...
Page 255: ...F o r R e f e r e n c e O n l y ...
Page 256: ...F o r R e f e r e n c e O n l y ...