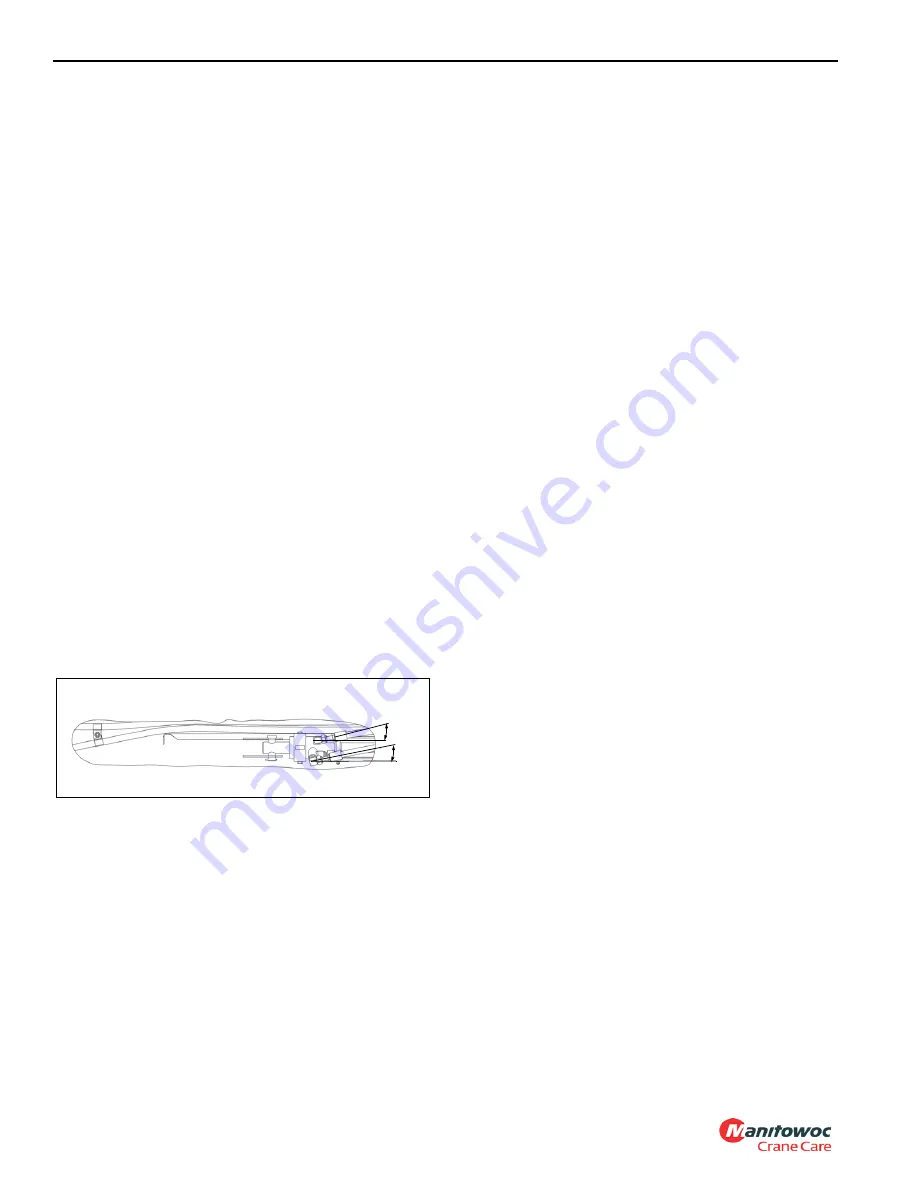
UNDERCARRIAGE
RT770E
8-34
Published 11/26/2014, Control # 447-05
Extension Cylinder
Description
Two outrigger extension cylinders are utilized within each
outrigger box assembly. The extension cylinders provide the
force for the outrigger beam’s horizontal movement. The
cylinder weighs approximately 51 kg (112 lb).
Maintenance
NOTE:
Refer to Cylinders in
for Disassembly and Assembly of the cylinder.
Removal
1.
Remove the outrigger beam. Refer to
page 8-30 in this section.
2.
Remove the cotter pin and clevis pin securing the rod
end of the extension cylinder to the outrigger beam.
3.
Pull the extension cylinder from the outrigger beam until
the hydraulic hoses on the rod end of the cylinder can be
accessed. Tag and disconnect the hoses from the rod
end of the cylinder. Cap or plug all openings.
4.
Remove the cylinder.
Installation
1.
Place the cylinder in the beam.
NOTE:
Keep hydraulic fittings and hoses close to angles
shown and as low as possible to prevent rubbing
with the beam top plate and side plate, and for
proper tracking during beam extension and
retraction Figure 8-32.
2.
Position the extension cylinder so the hydraulic ports on
the rod end of the cylinder can be accessed. Connect
the hydraulic hoses to the ports as tagged during
removal. Verify the piston side of the extension cylinder
is connected to the solenoid valve bank to prevent
damage.
3.
Push the cylinder into the outrigger beam. Align the
cylinder rod with the clevis in the beam. Apply anti-seeze
to the clevis pin and secure in place with the clevis pin
and cotter pin.
4.
Install the outrigger beam. Refer to
page 8-30. Verify no jack cylinder hose will be trapped
by full outrigger beam retraction.
Functional Check
1.
Activate the hydraulic system; extend and retract the
outrigger.
2.
Observe the operation of the outrigger beam. If hydraulic
lines are reversed, stop immediately and connect lines
properly per instructions. Verify no jack cylinder hose is
trapped by full outrigger beam retraction; if any is, stop
immediately and install lines properly to avoid trapping.
3.
Check the hydraulic connections and hoses for any
evidence of leakage. Make repairs as needed.
Outrigger Monitoring System (Optional—
Standard in North America)
Description
The Outrigger Monitoring System (OMS) aids the operator in
accurately programming the Rated Capacity Limiter (RCL)
by automatically identifying the horizontal position of each
outrigger beam. The OMS uses four sensors, one per
outrigger beam, to indicate when an outrigger beam is
positioned to one of three pre-defined locations, including
fully retracted, mid-extend, and fully extended.
If the crane is setup on outriggers and “On Outriggers” is
chosen when programming the RCL, then the OMS indicates
to the RCL the horizontal position of each of the four
outrigger beams. Based on this information, the RCL will
d e f a u l t t o t h e m o s t c o n s e r v a t i v e o u t r i g g e r b e a m
configuration; that is, if three outriggers are fully extended
and one is retracted, the RCL will select retracted as the
outrigger configuration. A confirmation of this outrigger
configuration is all that is needed. Refer to the
Rated
Capacity Limiter Operator ’s Handbook
for detailed
instructions.
Removal
1.
Extend the outrigger beam slightly for improved access
and shut down the engine.
2.
Remove the outer access cover plate from the outrigger
box.
3.
Remove the OMS string potentiometer connector
Figure 8-33 from the attaching point on the outrigger
beam.
NOTE:
Avoid free-release of cable to prevent damage to
the OMS string potentiometer.
4.
Disconnect electrical harness connector and secure to
avoid damage.
5.
Loosen top mounting hardware enough to disengage
OMS string potentiometer from the slotted top mounting
hole.
6.
Completely remove the lower mounting hardware.
FIGURE 8-32
10
°
15
°
7554-2
Summary of Contents for Grove RT770E
Page 3: ...Service Maintenance Manual Grove RT770E ...
Page 4: ......
Page 40: ...INTRODUCTION RT770E SERVICE MANUAL 1 26 Published 11 26 2014 Control 447 05 THIS PAGE BLANK ...
Page 124: ...HYDRAULIC SYSTEM RT770E 2 84 Published 11 26 2014 Control 447 05 THIS PAGE BLANK ...
Page 149: ...4 5 Published 11 26 2014 Control 447 05 RT770E SERVICE MANUAL BOOM 4 GROVE FIGURE 4 2 ...
Page 150: ...BOOM RT770E SERVICE MANUAL 4 6 Published 11 26 2014 Control 447 05 FIGURE 4 2 continued ...
Page 152: ...BOOM RT770E SERVICE MANUAL 4 8 Published 11 26 2014 Control 447 05 FIGURE 4 2 continued ...
Page 154: ...BOOM RT770E SERVICE MANUAL 4 10 Published 11 26 2014 Control 447 05 FIGURE 4 2 continued ...
Page 224: ...5 24 Published 11 26 2014 Control 447 05 HOIST AND COUNTERWEIGHT RT770E This Page Blank ...
Page 276: ...POWER TRAIN RT770E 7 30 Published 11 26 2014 Control 447 05 THIS PAGE BLANK ...
Page 300: ...UNDERCARRIAGE RT770E 8 24 Published 11 26 2014 Control 447 05 FIGURE 8 28 ...
Page 348: ...LUBRICATION RT770E 9 36 Published 11 26 2014 Control 447 05 FIGURE 9 14 102 8130 2 ...
Page 356: ......
Page 357: ......