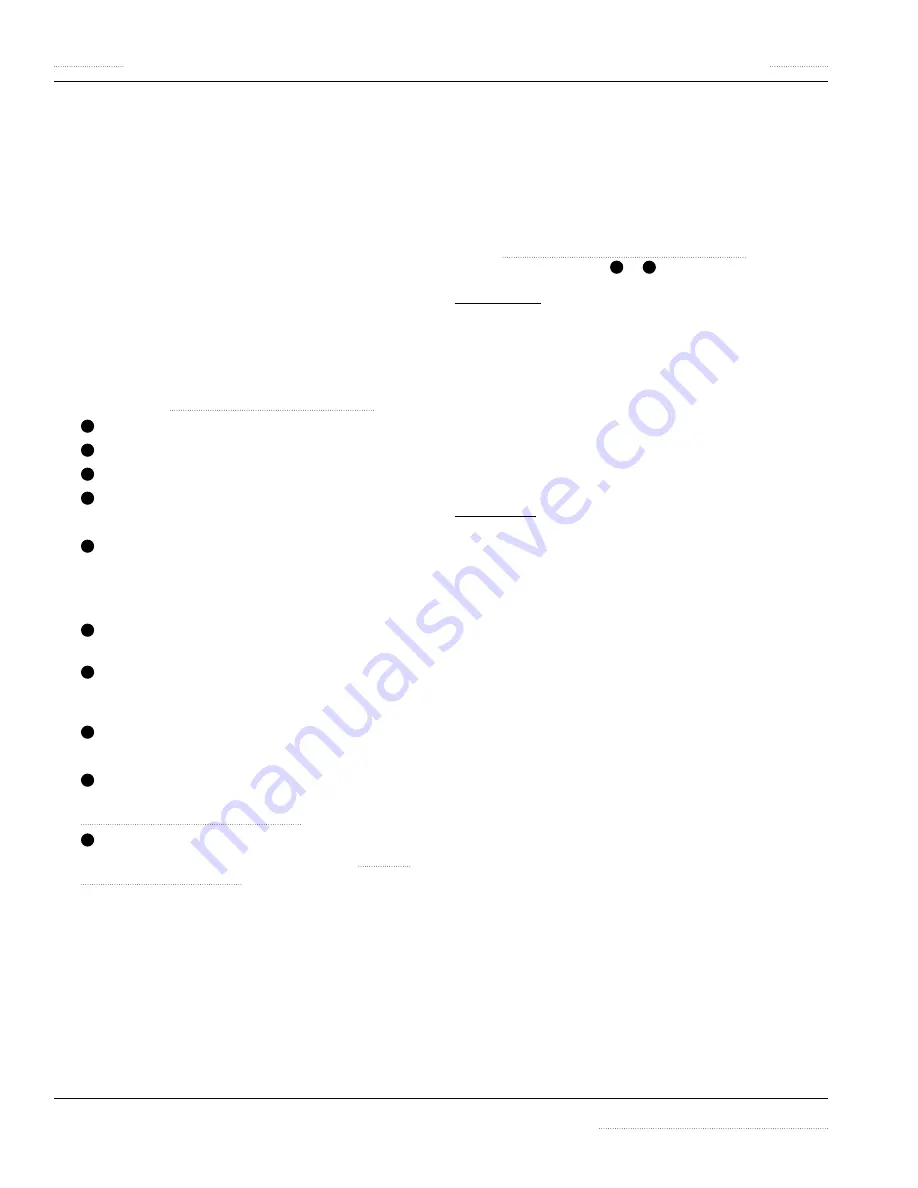
16
Part Number 4520898 Rev 7 11/15
Typical Applications
In this section you will find examples of the most common
installations for the induction appliance.
• Application 1 shows an installation of multiple
appliances. Special attention must be paid to the
ventilation and electrical requirements in this situation.
• In Applications 2 to 4, only a single appliance is
shown for simplicity and to illustrate the key cabinet
requirements.
IMPORTANT DESIGN FEATURES
Note the following key design features in each application
example :
Adequate ventilation:
(See details in Ventilation Methods on page 14)
1
Fresh air intake vent and air filter
2
Fresh air intake duct
3
Louvered opening or ventilation gap
4
Louvered openings or ventilation fan(s)
Safe electrical environment:
5
An enclosed compartment protects the electronic
appliance and wiring from the environment.
Personnel are also protected from the electronics and
the electrical cables.
6
The main power cable is routed separately from
control unit cable.
7
The main power supply plug of the appliance,
or the circuit breaker box for multiple appliance, is
accessible for disconnect.
8
Supply inlet / conduit opening shown.
Water-tight environment:
9
Mating surfaces between the appliance and
coutertop are sealed with silicone (not shown, see
Installation Instructions on page 34).
10
Design and construct ventilation gaps that
could prevent water ingress (not shown, see Cabinet
APPLICATION EXAMPLE 1
• Multiple appliances of the same or different types are
built into the same counter or island suite.
• In this application, it is very important that all
ventilation and electrical requirements are met.
• See Important Design Features on page 16 for the
descriptions of items
1
to
8
in illustration.
VENTILATION
• Heat from the exhaust builds up quickly. Built up of
hot exhaust will cause the electronic equipment to
overheat, to reduce power, or to shutdown.
• Recommendations:
• Install ventilation fan or fans to quickly remove hot
exhaust from the cabinet. (Illustration, item 4)
• Verify in the final installation that the ambient
temperature for the induction components during
operation is below 40
o
C or 104
o
F.
ELECTRICAL:
• NOTE: National and local electrical codes dictate the
electrical requirements for this type of application. For
example, some jurisdictions allow only a single power
supply connection from an installation and some allow
for a maximum of two power supply connections.
Consult your local authority or electrical contractor for
details.
• Illustration: Each appliance is plugged into a receptacle
and each receptacle is connected to a circuit breaker
(item 7). The circuit breakers are connected to a
single power supply. The breaker box is accessible for
disconnection from the power supply.
Summary of Contents for BH/IN 2500
Page 55: ......