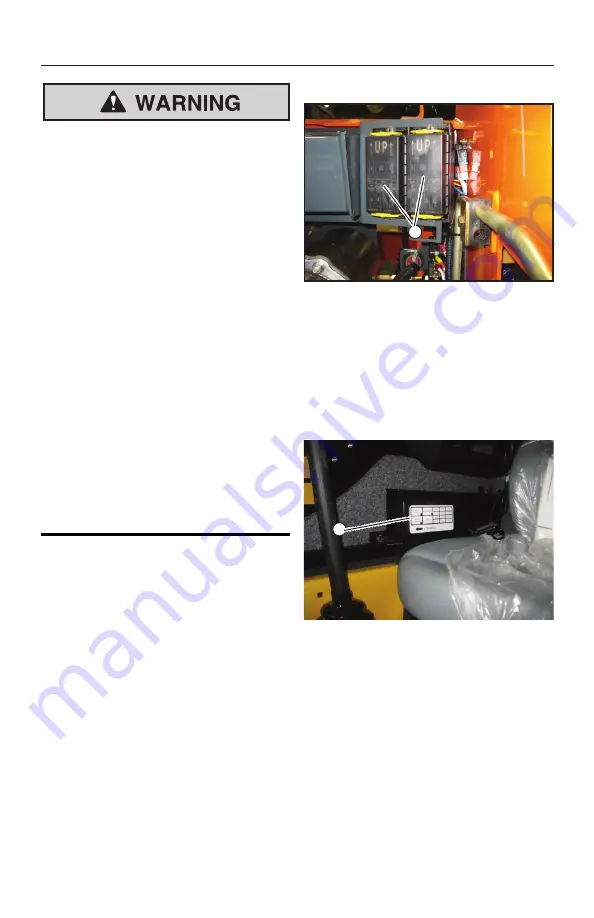
MAINTENANCE
50950436
/
H0521
122
Printed in U.S.A.
Never lay a metal object on top of a
battery, because a short circuit can
result. Battery acid is harmful to skin
and fabrics. If acid spills, follow these
first-aid tips:
• If battery acid spills on any clothing,
remove it immediately.
• If acid contacts skin, rinse the
affected area with running water for 10
to 15 minutes.
• If acid contacts eyes, flood eyes with
running water for 10 to 15 minutes. See
a doctor at once. Never use any medi-
cation or eye drops unless prescribed
by the doctor.
• To neutralize acid spilled on the floor,
use one of the following mixtures:
• 0.5 kg (1 lbs.) of baking soda
in 4 L (4 qts.) of water.
• 0.5 L (0.5 qts.) of household
ammonia in 4 L (4 qts.) of water.
The battery on the loader is a 12-volt, wet-cell
battery . To access the battery, open the rear
door and lift the engine cover .
The battery top must be kept clean . Clean it
with an alkaline solution (ammonia or baking
soda and water) . After foaming has stopped,
flush the battery top with clean water. If the
terminals and cable connection clamps are
corroded or have a build-up, disconnect the
cables and clean the terminals and clamps with
the same alkaline solution .
Using a Booster Battery
(Jump-Starting)
Use only the proper jump-starting procedure
according to “Jump-Starting” on page 94.
Fuses and Relays
Fig. 78 -
Q
Fuse Panels in the Engine
Compartment
The fuse panels (Q, Fig . 78) are located in
the engine compartment near the chassis right
riser and behind a panel in the ROPS/FOPS (S,
Fig . 79) at the operator’s right elbow area . The
plastic covers are either etched or have a decal
with the type of fuses and relays that can be
found under that particular fuse/relay cover .
Fig. 79 -
S
Fuse Panel in the ROPS/FOPS
Summary of Contents for MUSTANG 1050RT
Page 63: ...Indicators and Controls 50950436 H0521 60 Printed in U S A ...
Page 109: ...50950436 H0521 106 Printed in U S A ...
Page 127: ...MAINTENANCE 50950436 H0521 124 Printed in U S A Maintenance Log Date Hours Service Procedure ...
Page 128: ...MAINTENANCE Printed in U S A 125 50950436 H0521 Maintenance Log Date Hours Service Procedure ...
Page 129: ...MAINTENANCE 50950436 H0521 126 Printed in U S A Maintenance Log Date Hours Service Procedure ...
Page 130: ...MAINTENANCE Printed in U S A 127 50950436 H0521 Maintenance Log Date Hours Service Procedure ...
Page 131: ...MAINTENANCE 50950436 H0521 128 Printed in U S A ...
Page 142: ...Troubleshooting Printed in U S A 139 50950436 H0521 Error Codes ...
Page 143: ...Troubleshooting 50950436 H0521 140 Printed in U S A ...
Page 144: ...Troubleshooting Printed in U S A 141 50950436 H0521 ...
Page 145: ...Troubleshooting 50950436 H0521 142 Printed in U S A ...
Page 146: ...Troubleshooting Printed in U S A 143 50950436 H0521 ...