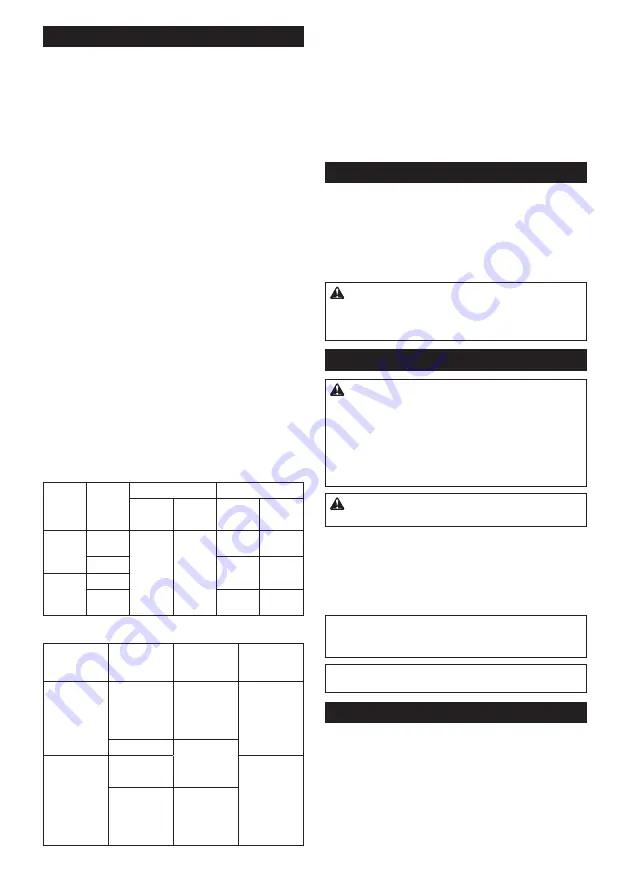
14 ENGLISH
Cutting crown and cove moldings
Crown and cove moldings can be cut on a compound
miter saw with the moldings laid flat on the turn base.
There are two common types of crown moldings and
one type of cove moldings; 52/38° wall angle crown
molding, 45° wall angle crown molding and 45° wall
angle cove molding.
►
Fig.29:
1.
52/38° type crown molding
2.
45° type
crown molding
3.
45° type cove molding
There are crown and cove molding joints which are
made to fit "Inside" 90° corners ((a) and (b) in the figure)
and "Outside" 90° corners ((c) and (d) in the figure.)
►
Fig.30:
1.
Inside corner
2.
Outside corner
►
Fig.31:
1.
Inside corner
2.
Outside corner
Measuring
Measure the wall width, and adjust the width of the
workpiece according to it. Always make sure that width
of the workpiece's wall contact edge is the same as wall
length.
►
Fig.32:
1.
Workpiece
2.
Wall width
3.
Width of the
workpiece
4.
Wall contact edge
Always use several pieces for test cuts to check the
saw angles.
When cutting crown and cove moldings, set the bevel
angle and miter angle as indicated in the table (A) and
position the moldings on the top surface of the saw
base as indicated in the table (B).
In the case of left bevel cut
►
Fig.33:
1.
Inside corner
2.
Outside corner
Table (A)
–
Molding
position
in the
figure
Bevel angle
Miter angle
52/38°
type
45° type
52/38°
type
45° type
For
inside
corner
(a)
Left
33.9°
Left 30°
Right
31.6°
Right
35.3°
(b)
Left
31.6°
Left
35.3°
For
outside
corner
(c)
(d)
Right
31.6°
Right
35.3°
Table (B)
–
Molding
position in
the figure
Molding
edge against
guide fence
Finished
piece
For inside
corner
(a)
Ceiling
contact edge
should be
against guide
fence.
Finished
piece will be
on the Left
side of blade.
(b)
Wall contact
edge should
be against
guide fence.
For outside
corner
(c)
Finished
piece will be
on the Right
side of blade.
(d)
Ceiling
contact edge
should be
against guide
fence.
Example:
In the case of cutting 52/38° type crown molding for
position (a) in the above figure:
•
Tilt and secure bevel angle setting to 33.9° LEFT.
•
Adjust and secure miter angle setting to 31.6° RIGHT.
•
Lay crown molding with its broad back (hidden) surface
down on the turn base with its CEILING CONTACT
EDGE against the guide fence on the saw.
•
The finished piece to be used will always be on the
LEFT side of the blade after the cut has been made.
Cutting aluminum extrusion
►
Fig.34:
1.
Vise
2.
Spacer block
3.
Guide fence
4.
Aluminum extrusion
5.
Spacer block
When securing aluminum extrusions, use spacer blocks
or pieces of scrap as shown in the figure to prevent
deformation of the aluminum. Use a cutting lubricant
when cutting the aluminum extrusion to prevent build-up
of the aluminum material on the blade.
CAUTION:
Never attempt to cut thick or round
aluminum extrusions.
Thick aluminum extrusions
may come loose during operation and round alumi-
num extrusions cannot be secured firmly with this tool.
Wood facing
WARNING:
Use screws to attach the wood facing
to the guide fence. The screws should be installed so
that the screw heads are below the surface of the wood
facing so that they will not interfere with the position-
ing of the material being cut.
Misalignment of the material
being cut can case unexpected movement during the
cutting operation which may result in a loss of control and
serious personal injury.
CAUTION:
Use the straight wood of even
thickness as the wood facing.
Use of wood facing helps to assure splinter-free cuts
in workpieces. Attach a wood facing to the guide fence
using the holes in the guide fence.
See the figure concerning the dimensions for a sug
-
gested wood facing.
►
Fig.35:
1.
Holes
NOTICE:
When the wood facing is attached, do
not turn the turn base with the handle lowered.
The blade and/or the wood facing will be damaged.
NOTE:
The maximum cutting width will be smaller by
the width of wood facing.
Cutting repetitive lengths
When cutting several pieces of stock to the same
length, ranging from 240 mm to 380 mm, use the set
plate (optional accessory). Install the set plate on the
holder (optional accessory) as shown in the figure.
►
Fig.36:
1.
Set plate
2.
Holder
3.
Screw
Align the cutting line on your workpiece with either the left or
right side of the groove in the kerf board, and while holding
the workpiece, move the set plate flush against the end of the
workpiece. Then secure the set plate with the screw.
Summary of Contents for 0088381821995
Page 2: ...2 Fig 1 1 Fig 2 1 Fig 3 1 2 3 Fig 4 1 Fig 5 1 Fig 6 1 Fig 7 1 Fig 8 ...
Page 3: ...3 1 Fig 9 1 Fig 10 2 1 3 130mm Fig 11 1 2 Fig 12 1 Fig 13 1 Fig 14 1 2 Fig 15 1 2 Fig 16 ...
Page 4: ...4 1 Fig 17 1 2 Fig 18 1 2 3 4 Fig 19 1 2 3 4 5 6 Fig 20 1 Fig 21 Fig 22 1 Fig 23 1 Fig 24 ...
Page 7: ...7 1 Fig 41 1 2 3 Fig 42 1 Fig 43 1 2 Fig 44 Fig 45 1 2 Fig 46 ...