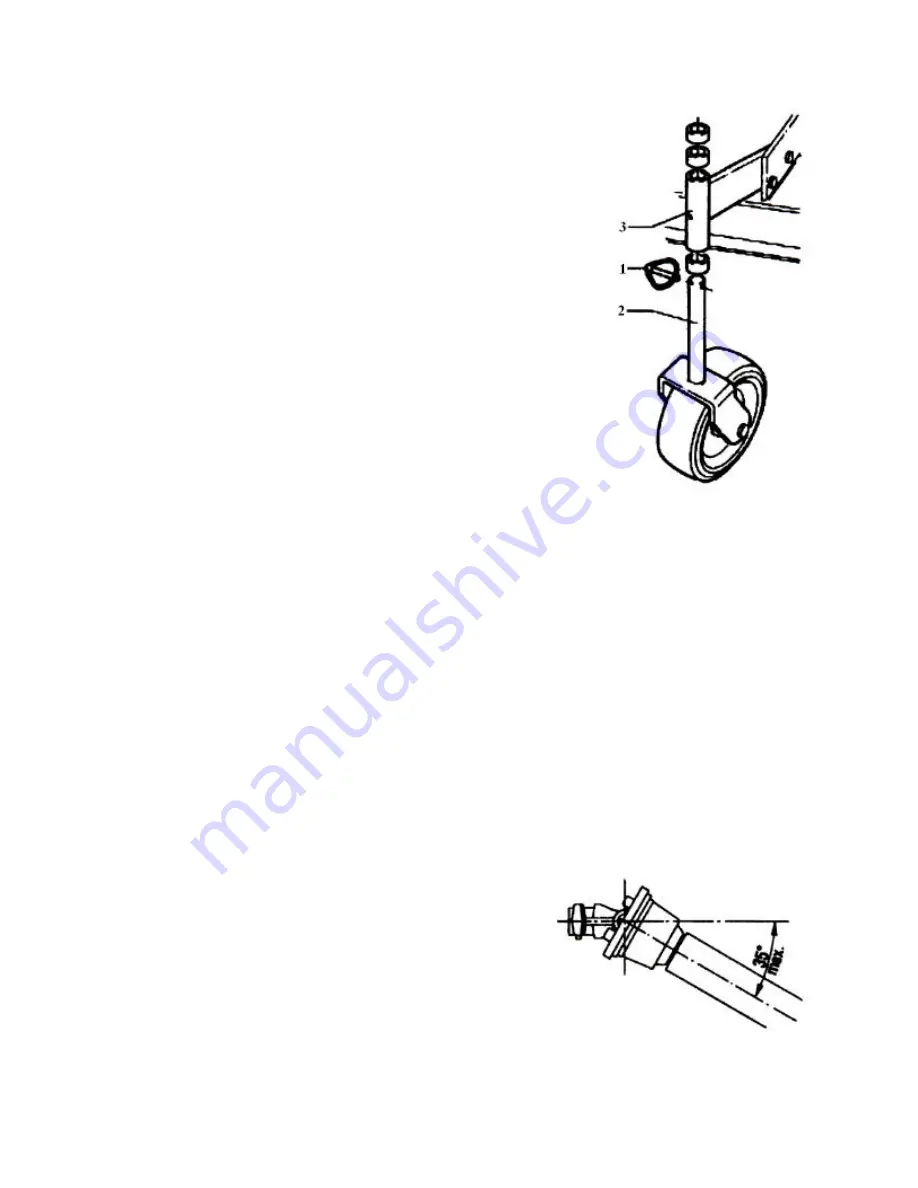
14
Using the Mower
Before working always check that all the safety shields listed in page 6 are installed, correctly mounted and
efficient. Failing this, stop the mower and replace or repair the damaged shields. Never continue work until all
the shields installed by the manufacturer are efficient. Contact your nearest after-sales service centre if
necessary. Always become familiar with mower use before working with the implement. Make sure that you
know how to quickly stop the work operations.
Step 1: Lower the machine until the four wheels are resting on the ground.
Step 2: If any further adjustments are necessary, carry out the work as described in the paragraph – Adjusting
the Cutting Height
Step 3: Accelerate the tractor by depressing the accelerator pedal to about half its travel and then engage the
PTO.
Step 4: Advance with the tractor, setting the PTO to the required rpm rate (usually 540 or 1000 rpm). The
travelling speed of the tractor must be selected according to the grass to be cut, its quantity and the cutting finish
required. Optimum work speeds will be between 3 and 8 Km/hour (2/5 mph).
Adjusting the Cutting Height – Fig 6.1
To alter the cutting height, proceed as follows:
•
Remove the split pin 1
•
Slide out the wheel axle 2;
•
Slide the spacers supplied with each wheel or parts of these
spacers onto the wheel axis 2 according to the height
required.
•
Mount the wheel axis 2 onto the wheel support 3, slide any
remaining spacers on and lock them in place with the split
pins 1 (see fig. 6.1). The spacers are all different-sized to
enable the height to be altered as accurately as possible.
The more spacers are placed below the wheel support "3",
the further away the blades will be from the ground (until
reaching the maximum cutting height).
IMPORTANT:
However the spacers are laid out, the wheel axle must
have the minimum clearance.
CAUTION:
Always check that the driveline is unable to touch the
implement when the mower is raised from the ground.
Important:
•
The cutting finish will better if the tractor travels slowly while
operating. Always raise the implement from the ground during
manoeuvres, round bends and when reversing. After having
worked for a few meters, stop and check whether the desired
result is being obtained. Make any adjustments as may be
necessary and then continue with the job.
•
Never reverse with the implement unless this is strictly
necessary. In such cases, disengage the pto and carefully
check to see whether there are any obstructions at the rear.
•
Never lift the implement more than 250 mm from the ground with the pto engaged or the driveline
could break and risk injury to the operator. The maximum tilt the driveline can bear with the PTO
engaged is 35° (
Fig. 6.2)
.
Fig. 6.1
Fig. 6.2