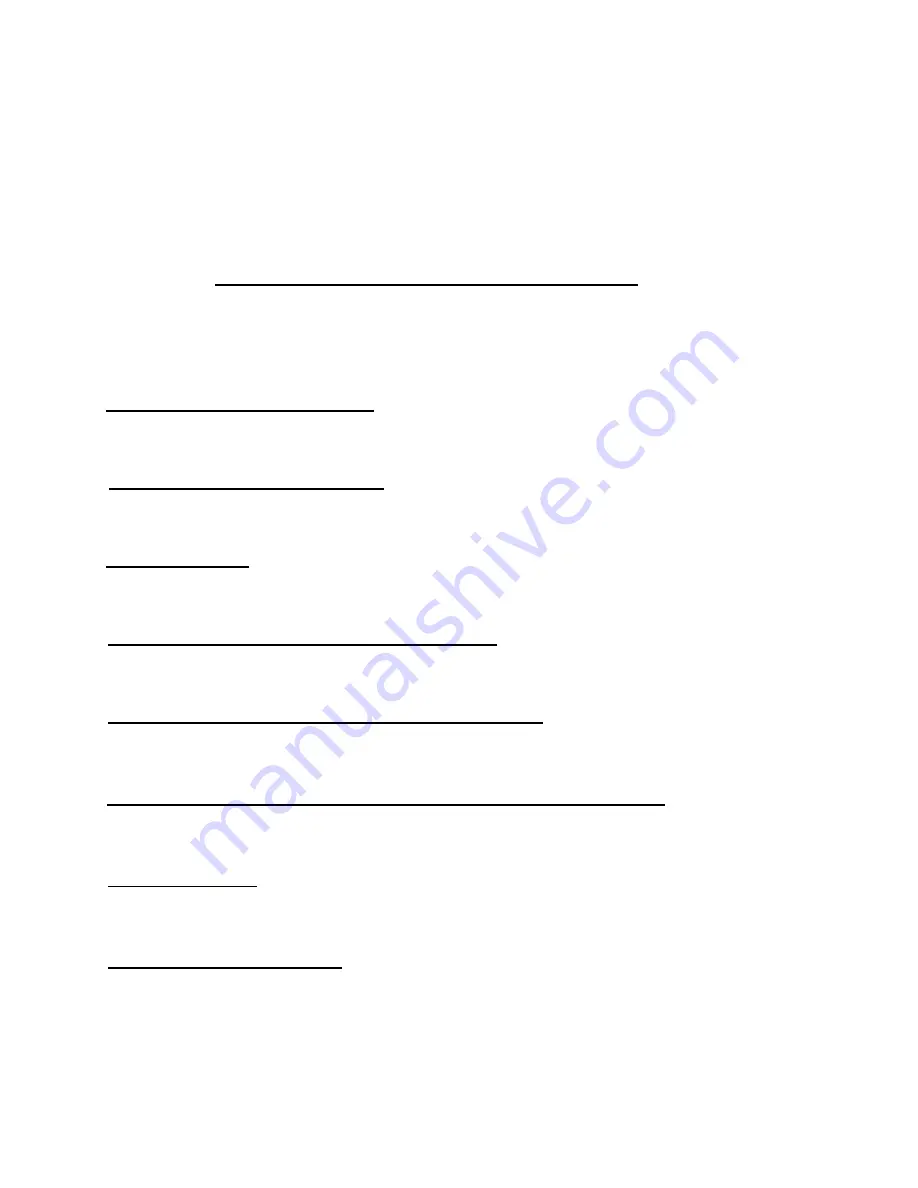
2
#
TABLE OF CONTENTS
#
• Warranty Information
………………………….……….…………………..
3
• Safe Servicing Practices
………………………………………………………
4
• Installation
………………………………………………..………………………..
5
• Important Pre Service Instructions
……………………..……………..
6
• Diagnosis & Technical Troubleshooting
……………………………..
7
• Replacement Procedure, Wiring & Testing of parts
…………..
12
• Quick Check
………………………………………………..………………………..
29
• Contact Information
…………………………………..………………………..
30