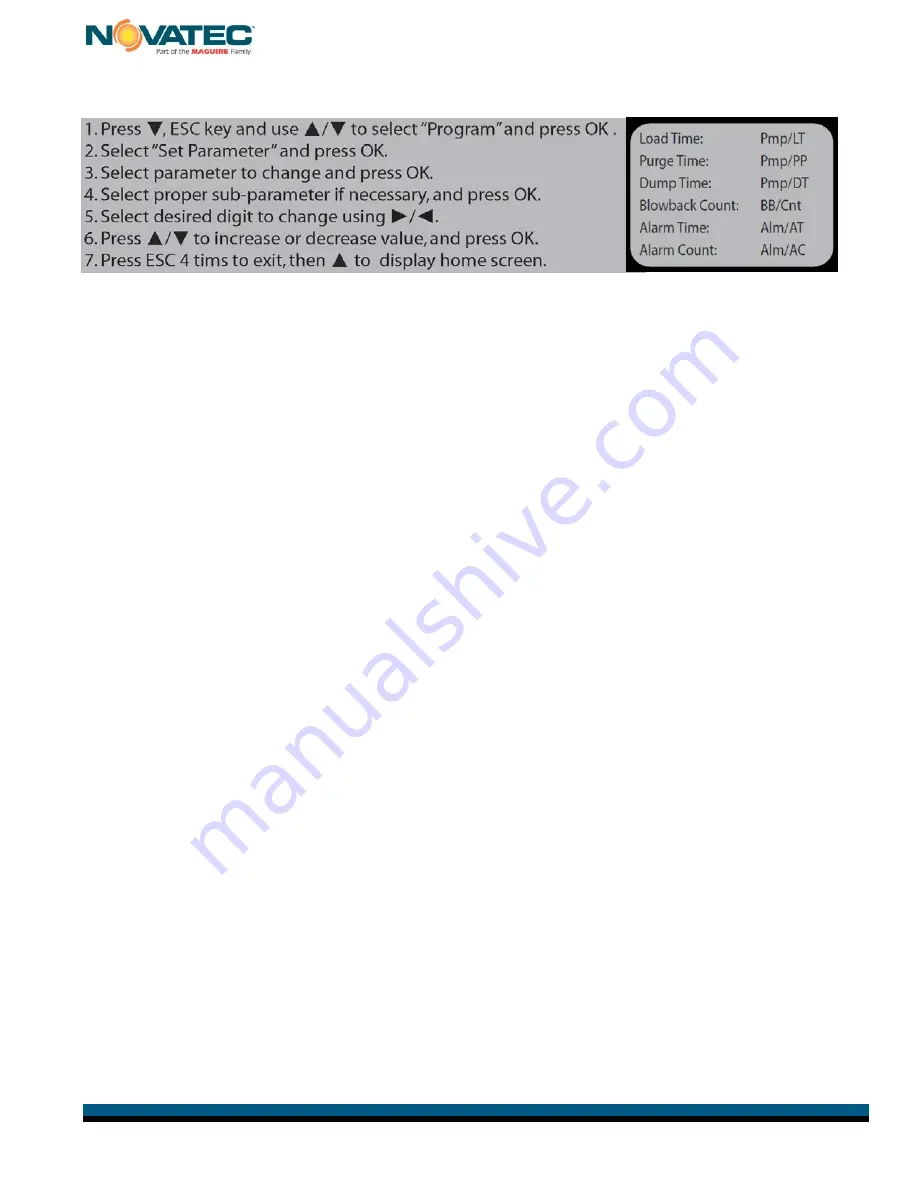
VL-VLP IM 19 JUNE 2017 © 2017 NOVATEC, Inc. All Rights Reserved
Page 11
8.1 TO CHANGE LOADING PARAMETERS
8.2 PARAMETERS EXPLANATION
Motor-on Time (Pmp/LT)
, measured in seconds, is the amount of time the vacuum motor
will run to load material into the loader’s vacuum chamber. Too little time will result in
insufficient loading and will shorten motor life with too many start/stop cycles. Too much
time will pack the loader full of material, prematurely blinding the filter and possibly clogging
the conveying line. This setting should be adjusted over the course of several normal
loading cycles to ‘just fill’ (but not overfill) the loader’s vacuum chamber. NOTE: VLP series
powder loaders include an extended body to house the cartridge filter(s). Loaded material
should not be allowed to be filled up into this extended hopper area. It is intended only as a
housing for the filter cartridges(s), not a hopper for collecting loaded material.
Dump Alarm Time (Alm/AT),
measured in seconds, is the pause time between the
completion of Motor On Time and movement of the discharge flapper. This time setting
drives the No-Load alarm feature by determining if material was actually loaded and
dumped, but prevents false alarms from slow moving material discharge. This setting may
be increased if nuisance alarms occur from slow moving material (IE: fluffy regrind) that is
typically slow to evacuate the loader.
It may be decreased if the No-Load alarm is too slow to respond to your material supply
needs
(IE: frequent shortages of material flow).
Dump Alarm Count (Alm/AC),
This number represents how many consecutive “no-load”
alarms will cause the alarm horn to sound.
Dump Time (Pmp/DT)
, measured in seconds, is the setting for how long the loader will
remain at rest after loading, to allow material to evacuate the loader. This setting may be
increased in case the material is very slow moving and/or to provide an extended OFF period
for the loader (IE: if the loader is used to off-load a granulator).
Blowback Count (BB/Cnt)
, is the number of blowback pulses that occur following loading
for the compressed air system to clean the filter(s). Compressed is blown down through the
filters in the opposite direction of the vacuum loading air, blasting collected fines and dust
from the filter media and into the loaded material. Typically, more blasts will clean the filters
better and extend the time between manual filter cleaning and provide more efficient loading.
However, compressed air is expensive and too many blasts waste this resource. Also,
blasts that extend beyond the dump sequence may actually be strong enough to create
dusting issues around the loader.