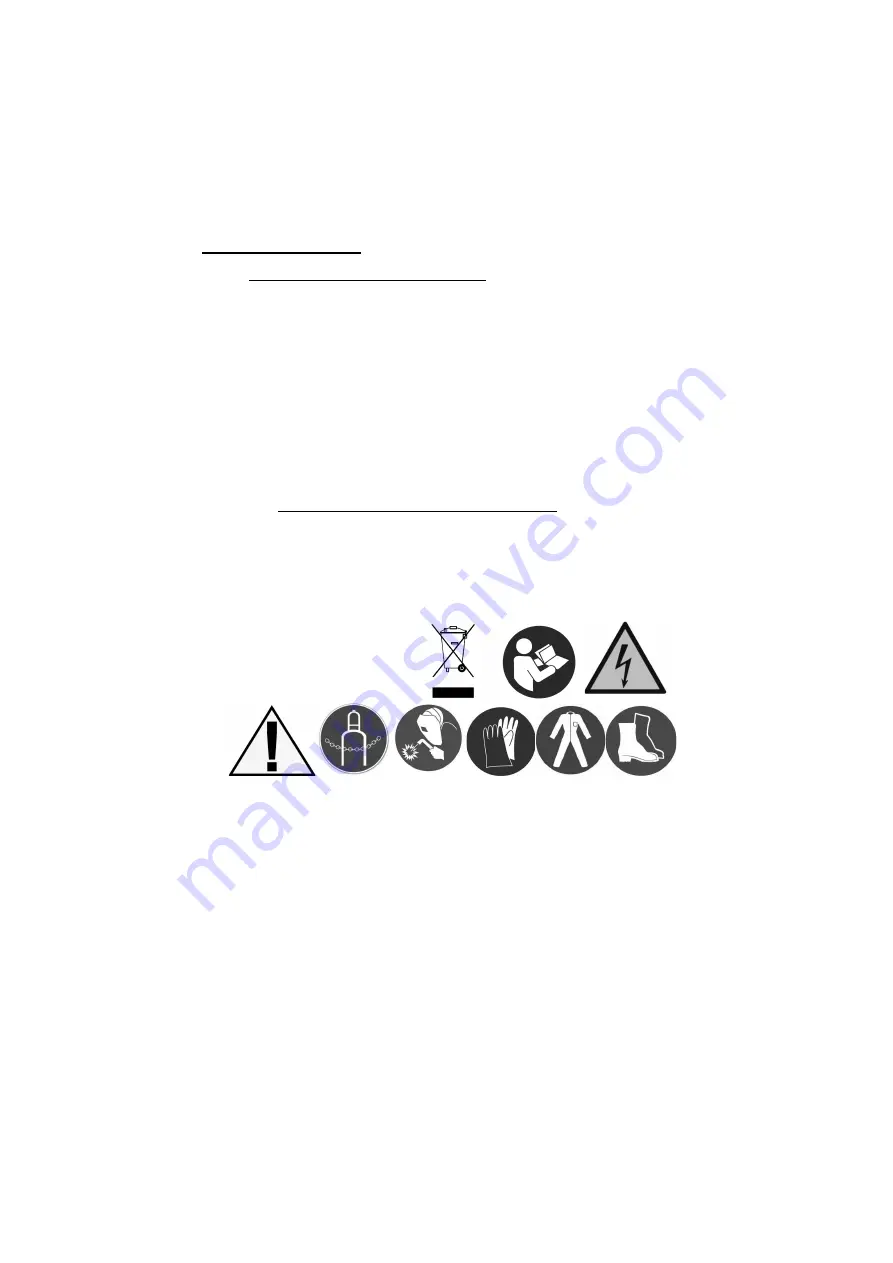
1
MANUAL inverter
semi-automatic WELDING
Model:
MIG 208 Alu Synergy
Drawings devices in the manual may differ from the original colors.
Translation of the original instructions.
with
NOTE: Please use a welder after a very careful reading the manual.
1. In order to ensure safety should be determined by qualified personnel responsible for installation,
maintenance, periodic inspection and repair equipment.
2. In order to ensure safety before working with the machine carefully and with full understanding
refer to the following instructions.
3. After reading the following instructions and keep it in a place accessible to other users of the
device.
Summary of Contents for MIG 208 Alu Synergy
Page 2: ...2 ...
Page 24: ...24 WWW SPAWSC PL WWW MAGNUM WELDING COM Cracow 2017 KR v1 ...