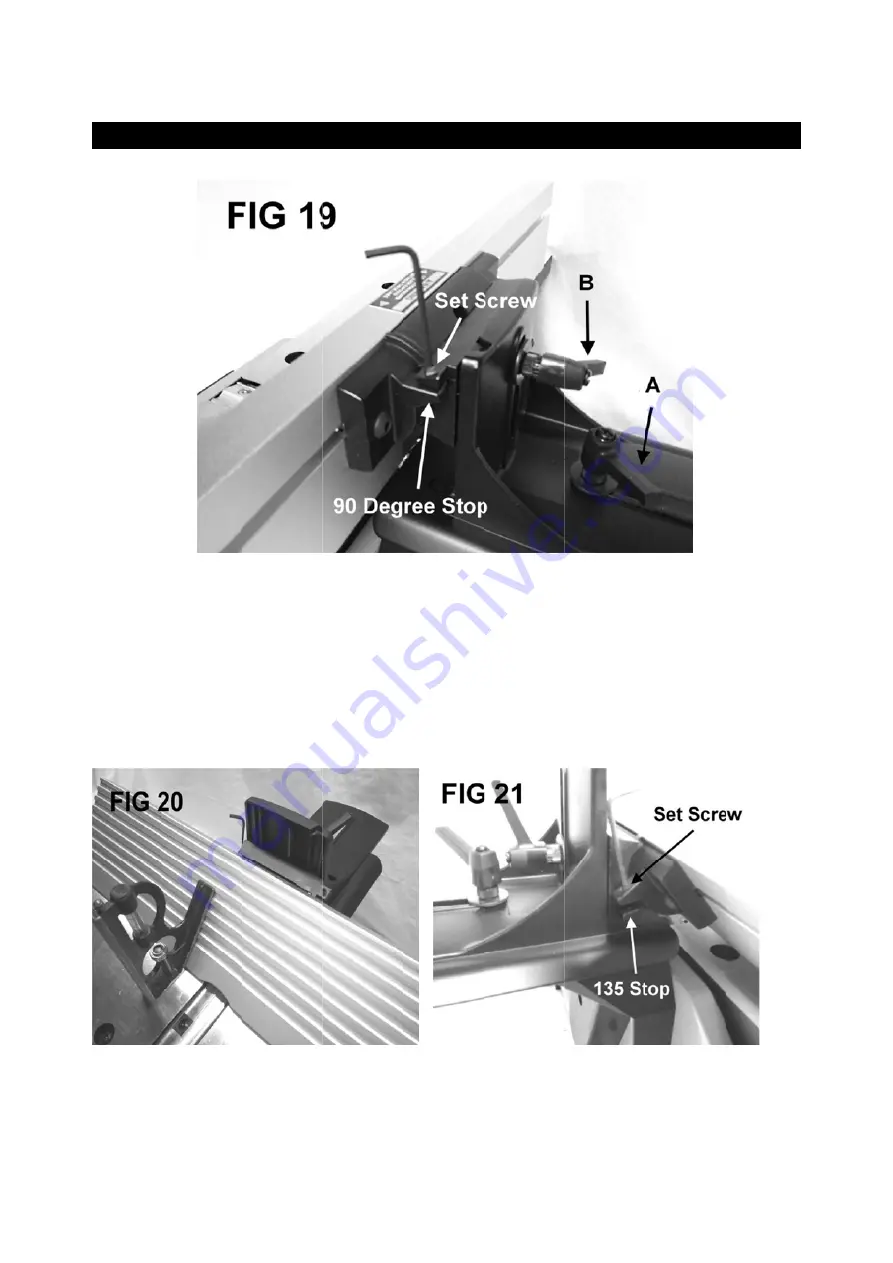
2. To set t
back co
shims u
screw a
necess
remove
You can
NOTE: Th
settings.
the 135 deg
ompletely an
under fence
against the
ary, use a fl
e the shims,
n now use f
hese positiv
ASSEM
gree stop, sl
nd re-tighte
e, and use th
stop. NOTE
lashlight to
and check
fence lever
ve stops ena
MBLY &
lightly loose
en lever “A”.
he provided
E: The set s
locate it. Se
for 45 degr
“B” to lock t
able you to
ADJUST
en lever “B”
. Place a 45
d 2.5mm He
screw is set
ee FIG 20 a
rees. If not
the fence at
quickly pos
TMENT
and loosen
5 degree an
ex Wrench t
deep into t
nd FIG 21.
at 45, repea
t the angle
sition the ta
S (cont.
n fence leve
ngle against
to adjust the
he angled h
Once adjus
at above pro
you choose
ble to the 9
.)
er “A”. Slide
t the fence,
e 135 degre
hole at the f
sted, tighten
rocedure.
e.
0 and 135 d
the fence
insert
ee set
factory. If
n lever “B”,
degree
Summary of Contents for MI-81190
Page 1: ...MODEL NO MI 81190 OPERATING MANUAL...
Page 11: ......
Page 32: ...TR ROUBLE ESHOOT TING GUIDE c cont...
Page 33: ...TR ROUBLE ESHOOT TING GUIDE c cont...
Page 41: ...PARTS...