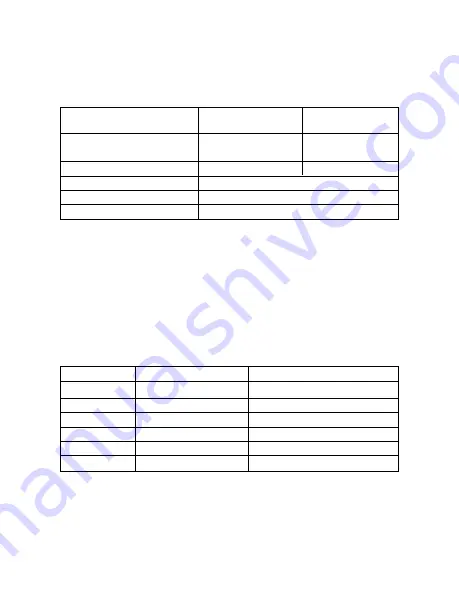
3
3..3
3 C
CO
ON
NS
ST
TA
AN
NT
T D
DE
ES
SC
CR
RIIP
PT
TIIO
ON
NS
S..
C
Co
on
ns
stta
an
ntt
P
Pa
as
ss
sw
wo
orrd
d /
/ IIn
niittiia
alliiz
za
attiio
on
n
Factory Setting: 1
n
n 0
0 1
1
The following table describes data which can be set or read when n
n 0
0 1
1 is set.
Programmable Accessible
Setting
Constants
Constants
0
n01
n02 to n69
(constant setting disabled)
1
n02 to n60
n01 to n69
2 to 7
Not Used
8
Initialize constants for 2-Wire sequence
9
initialize constants for 3-Wire sequence
NOTE: When either “ 8 ” or “ 9 ” is entered (initialization settings), the definitions
of inputs at terminals SF and SR are changed. Constants n
n 0
0 6
6 ,
n
n 0
0 7
7 , and
n
n 0
0 8
8 (Multi-function Input – Terminal S1, S2 & S3) settings are also changed,
according to the requirements of the control configuration (see Figures 1-5 and 1-6).
All other constants are returned to FACTORY SETTINGS; constant n
n 0
0 1
1 setting then
returns to “ 1 ”.
C
Co
on
ns
stta
an
ntt
O
Op
pe
erra
attiio
on
n M
Mo
od
de
e S
Se
elle
ec
cttiio
on
n
Factory Setting: 0
n
n 0
0 2
2
The setting of n
n 0
0 2
2 determines where the run command and speed reference will be
accepted.
Setting
Run/Stop Command From:
Speed Reference From:
0
Digital Operator
Digital Operator
1
External terminal
Digital Operator
2
Digital Operator
External terminal (Voltage input)
3
External terminal
External terminal (Voltage input)
4
Digital Operator
External terminal (Current input)
5
External terminal
External terminal (Current input)
On the next two pages are illustrations of control input required by each n
n 0
0 2
2
setting.
23
for more: efesotomasyon - Yaskawa drive