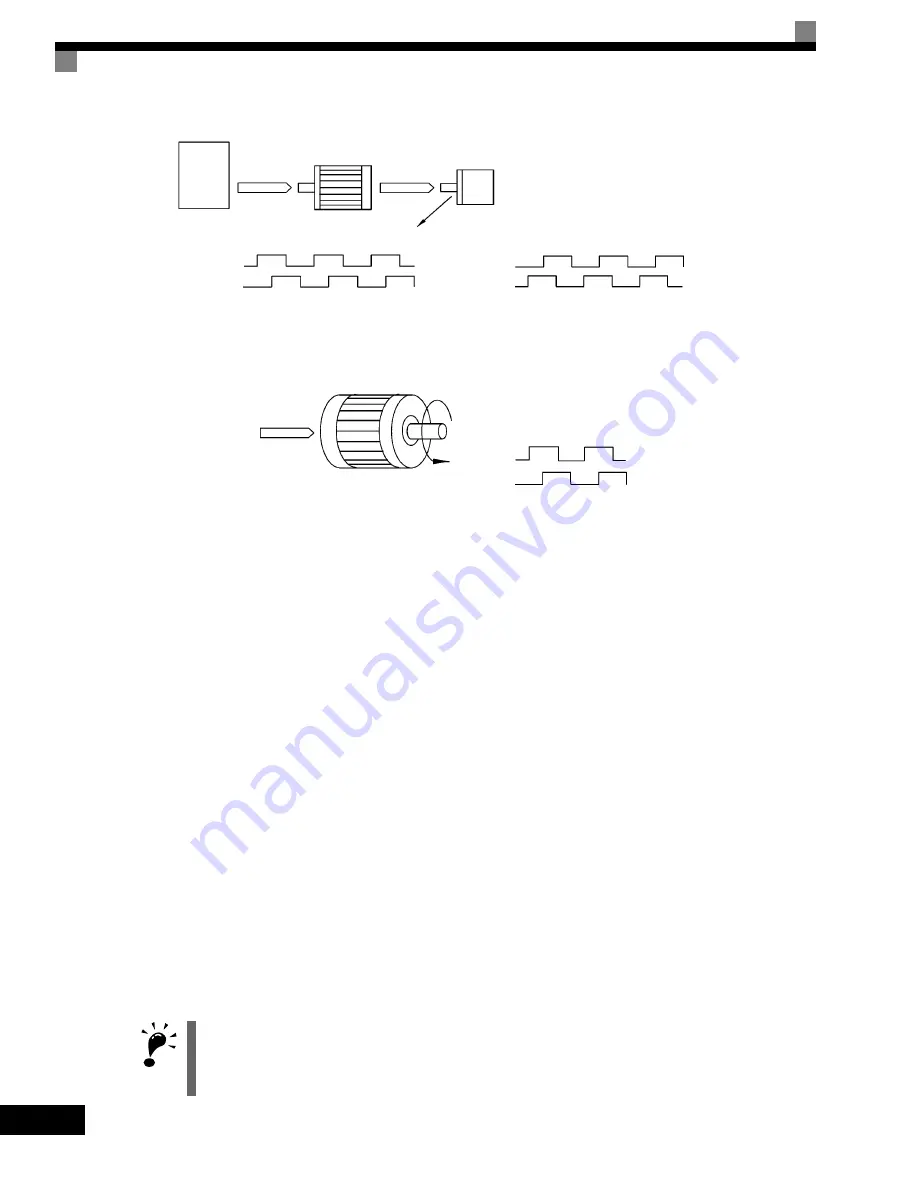
6
-154
Fig 6.75 PG Rotation Direction Setting
Generally, PG is A-phase driven when rotation is clockwise (CW) see from the input axis. Also, motor rota-
tion is counter-clockwise (CCW) seen from the output side when forward commands are output. Conse-
quently, when motor rotation is forward, PG is normally A-phase driven when a load is applied, and B-phase
driven when a load is not applied.
Setting Number of Gear Teeth Between PG and Motor
Set the number of PG gear teeth in F1-12 and F1-13. If there are gears between the motor and PG, you can
operate the motor by setting the number of gear teeth.
When the number of gear teeth has been set, the number of motor rotations within the Drive is calculated
using the following formula.
No. of motor rotations (min
1
.) = No. of input pulses from PC
60 / F1-01
F1-13 (No. of gear teeth on load
side) / F1-12 (No. of gear teeth on motor side)
Matching Motor Speed During Acceleration and Deceleration to Frequency Reference
You can select whether to enable or disable integral operation during acceleration and deceleration when using
flux vector control.
To match the motor speed as closely as possible to the frequency reference even during acceleration and decel-
eration, set F1-07 to 1.
IMPORTANT
If F1-01 is set to 1, overshoot or undershoot may occur easily immediately after acceleration and decelera-
tion. To minimize the possibility of overshoot or undershoot occurring, set F1-01 to 0.
Drive
Forward
command
Motor
PG (encoder)
Pulse output
A-phase driven when set value = 0
B-phase driven when set value = 1
A-phase
A-phase
B-phase
B-phase
Example: Forward rotation of standard
Magnetek
motor (PG used: Samtack (KK))
Forward
command
Motor output axis rotates
counter-clockwise during
Drive forward command.
Rotation
(CCW)
A-phase
B-phase
Magnetek
standard PG used is A-phase driven (CCW) when motor rotation is forward.