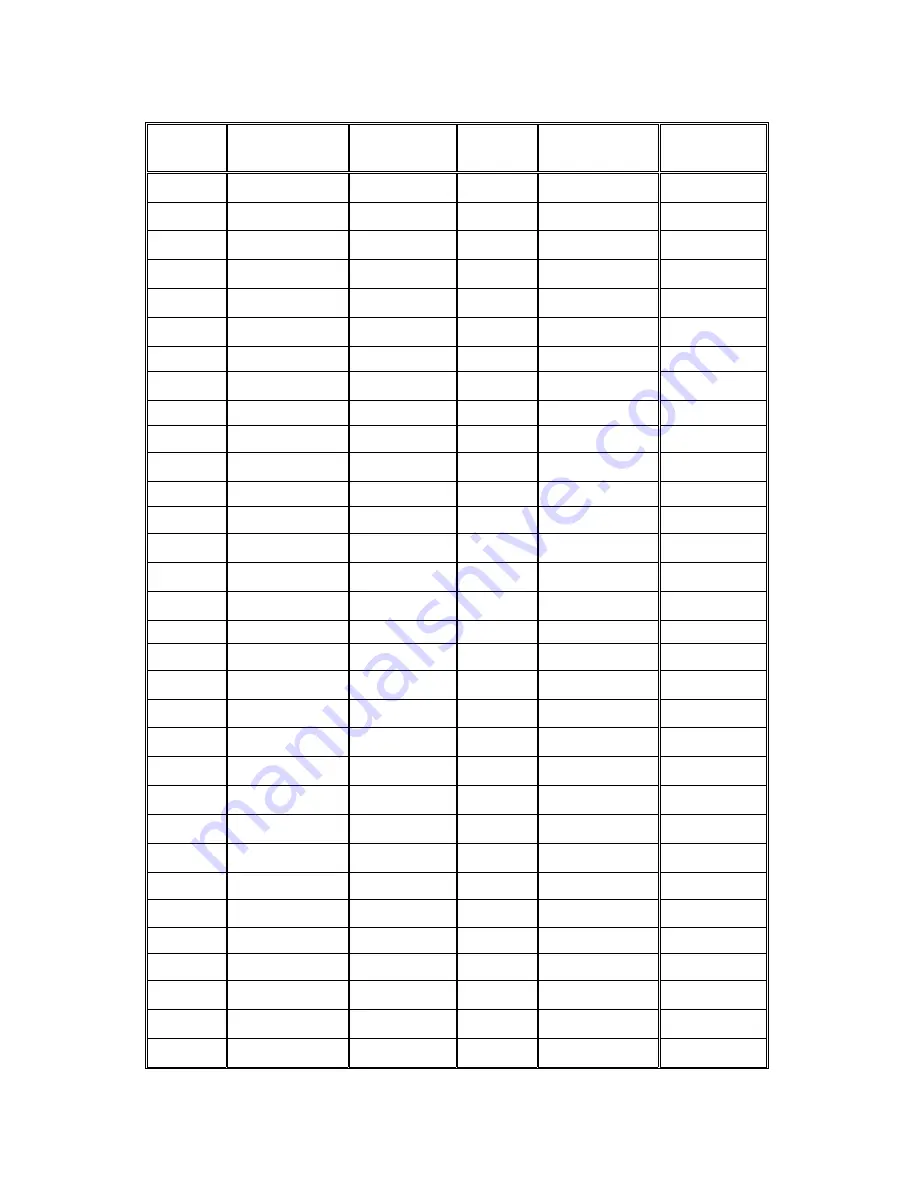
Flex 8RS System Instruction Manual
December 2012
26 of 36
5. SYSTEM CHANNELS TABLE
Channel
Frequency
Dip-switch
Setting
Channel
Frequency
Dip-switch
Setting
01
433.000MHZ 000000
32
433.775MHZ 100000
01
433.000MHZ 000001
33
433.800MHZ 100001
02
433.025MHZ 000010
34
433.825MHZ 100010
03
433.050MHZ 000011
35
433.850MHZ 100011
04
433.075MHZ 000100
36
433.875MHZ 100100
05
433.100MHZ 000101
37
433.900MHZ 100101
06
433.125MHZ 000110
38
433.925MHZ 100110
07
433.150MHZ 000111
39
433.950MHZ 100111
08
433.175MHZ 001000
40
433.975MHZ 101000
09
433.200MHZ 001001
41
434.000MHZ 101001
10
433.225MHZ 001010
42
434.025MHZ 101010
11
433.250MHZ 001011
43
434.050MHZ 101011
12
433.275MHZ 001100
44
434.075MHZ 101100
13
433.300MHZ 001101
45
434.100MHZ 101101
14
433.325MHZ 001110
46
434.125MHZ 101110
15
433.350MHZ 001111
47
434.150MHZ 101111
16
433.375MHZ 010000
48
434.175MHZ 110000
17
433.400MHZ 010001
49
434.200MHZ 110001
18
433.425MHZ 010010
50
434.225MHZ 110010
19
433.450MHZ 010011
51
434.250MHZ 110011
20
433.475MHZ 010100
52
434.275MHZ 110100
21
433.500MHZ 010101
53
434.300MHZ 110101
22
433.525MHZ 010110
54
434.325MHZ 110110
23
433.550MHZ 010111
55
434.350MHZ 110111
24
433.575MHZ 011000
56
434.375MHZ 111000
25
433.600MHZ 011001
57
434.400MHZ 111001
26
433.625MHZ 011010
58
434.425MHZ 111010
27
433.650MHZ 011011
59
434.450MHZ 111011
28
433.675MHZ 011100
60
434.475MHZ 111100
29
433.700MHZ 011101
61
434.500MHZ 111101
30
433.725MHZ 011110
62
434.525MHZ 111110
31
433.750MHZ 011111
I-CHIP
111111*
* When set to all “1” the priority goes to the channel assigned inside the I-CHIP.