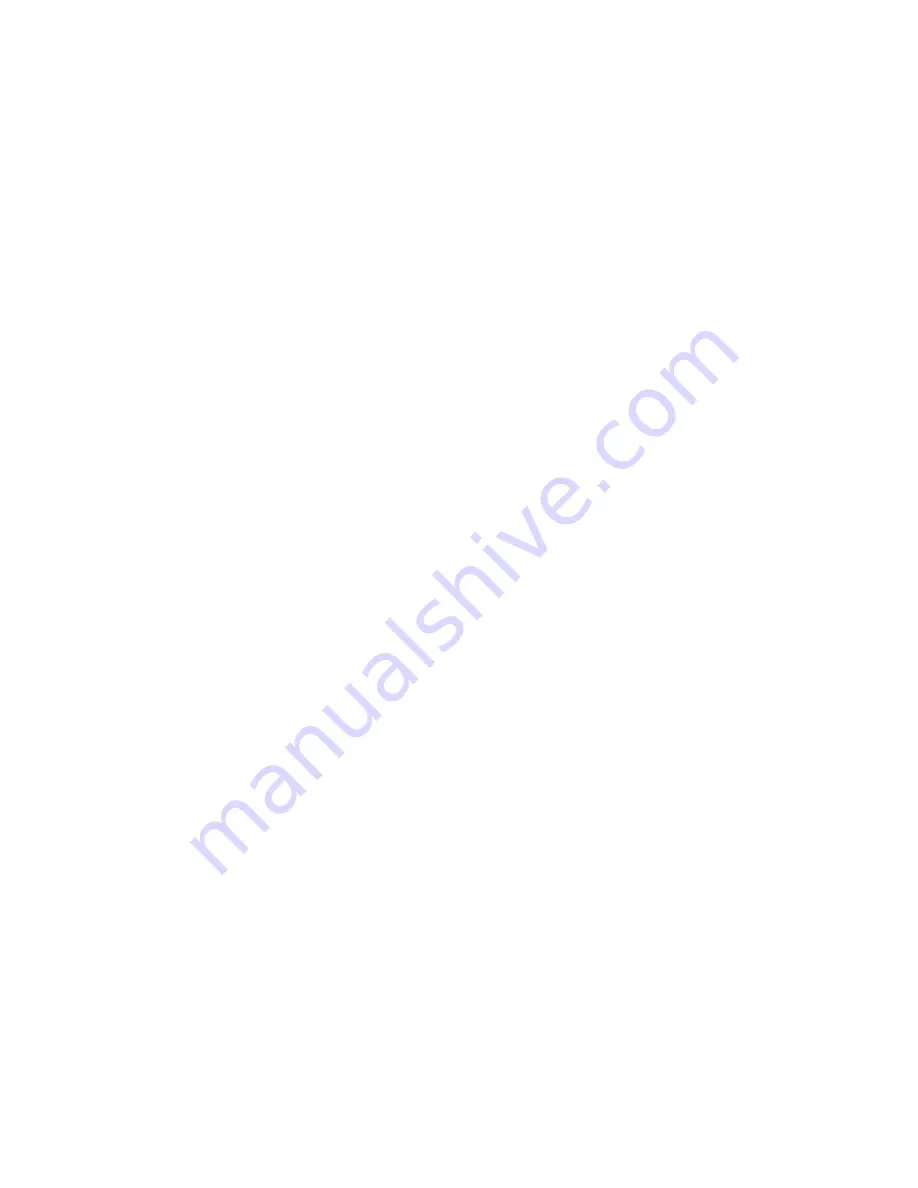
7
3.1 Fundamentals of Manual
Metal Arc (MMA) Welding
Welding Technique
Successful MMA welding depends on the
following factors:
Selection of the correct electrode.
Selection of the correct size of the electrode
for the job.
Correct welding current.
Correct arc length.
Correct angle of electrode to work.
Correct travel speed.
Correct preparation of work to be welded.
Electrode selection
As a general rule, the selection of an electrode
is straight forward, in that it is only a matter of
selecting an electrode of similar composition
to the parent metal. However, for some metals
there is a choice of several electrodes, each
of which has particular properties to suit
specifi c classes of work. Often, one electrode
in the group will be more suitable for general
applications due to its all round qualities.
Electrode size
The size of the electrode generally depends on
the thickness of the section being welded, and
the thicker the section the larger the electrode
required. In the case of light sheet, the electrode
size used is generally slightly larger than the
work being welded. This means that, if 2.0 mm
sheet is being welded, 2.5 mm diameter
electrode is the recommended size.
Welding current
Correct current selection for a particular job
is an important factor in arc welding. With the
current set too low, diffi culty is experienced
in striking and maintaining a stable arc.
The electrode tends to stick to the work,
penetration is poor and beads with a distinct
rounded profi le will be deposited.
Excessive current is accompanied by
overheating of the electrode. It will cause
undercut and burning through of the material,
and will give excessive spatter. Normal current
for a particular job may be considered as the
maximum, which can be used without burning
through the work, over-heating the electrode
or producing a rough spattered surface (i.e. the
current in the middle of the range specifi ed
on the electrode package is considered to be
the optimum).
Arc length
To strike the arc, the electrode should be gently
scraped on the work until the arc is established.
There is a simple rule for the proper arc length;
it should be the shortest arc that gives a good
surface to the weld. An arc too long reduces
penetration, produces spatter and gives a rough
surface fi nish to the weld. An excessively
short arc will cause sticking of the electrode
and rough deposits that are associated with
slag inclusions.
For down hand welding an arc length not
greater than the diameter of the core wire will
be most satisfactory. Overhead welding requires
a very short arc so that a minimum of metal will
be lost.
Electrode angle
The angle that the electrode makes with the
work is important to ensure a smooth, even
transfer of metal.
Correct travel speed
The electrode should be moved along in the
direction of the joint being welded at a speed
that will give the size of run required. At the
3.0 Basic Welding Techniques