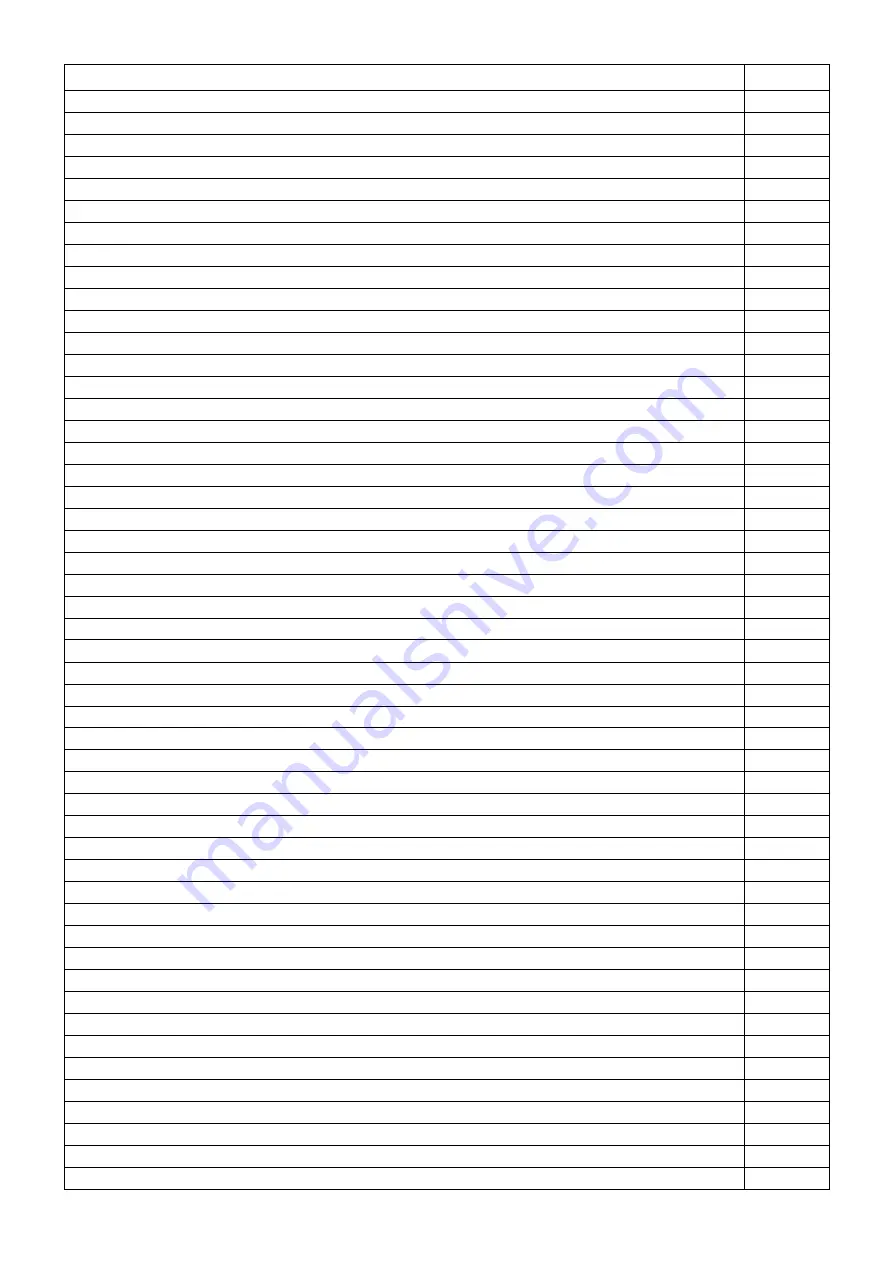
0-3
Item
Page
9.3 PRECAUTIONS FOR USE
2-86
9.3.1 INSTALLATION
2-86
9.3.2 PIPING
2-86
9.3.3 LUBRICATING OIL FOR GEARS
2-87
9.3.4 GENERAL PRECAUTIONS
2-87
10. CRANE CONTROL VALVE
2-88
10.1 EXTERIOR VIEW AND SPECIFICATIONS
2-88
10.2 HYDRAULIC CIRCUIT DIAGRAM
2-89
10.3 RGB BLOCK
2-90
10.4 ACCELERATOR BLOCK
2-92
10.5 FUNCTION BLOCK (DERRICK, WINCH, TELESCOPIC, SLEWING)
2-92
10.6 SOLENOID VALVE FUNCTIONING PRINCIPLE
2-93
11. OUTRIGGER CONTROL VALVE
2-96
11.1 EXTERIOR VIEW AND SPECIFICATIONS
2-96
11.2 INNER PARTS
2-98
12. OUTRIGGER SELECT VALVE
2-100
12.1 EXTERIOR VIEW AND SPECIFICATIONS
2-100
12.2 INNER PARTS
2-101
13. CRANE CIRCUIT CONFLUENCE VALVE
2-102
13.1 EXTERIOR VIEW and SPECIFICATIONS
2-102
13.2 INNER PARTS
2-103
13.3 INSPECTION AND ADJUSTMENT
2-104
13.4 TROUBLE SHOOTING
2-104
14. TRAVELING SPEED SELECT VALVE
2-106
14.1 EXTERIOR VIEW AND SPECIFICATIONS
2-106
14.2 INSPECTION AND ADJUSTMENT
2-107
14.3 TROUBLE SHOOTING
2-107
15. ROTARY JOINT
2-108
15.1 EXTERIOR VIEW AND SPECIFICATIONS
2-108
15.2 INNER PARTS
2-109
16. HOOK BLOCK
2-110
16.1 HOOK BLOCK INSPECTION
2-112
17. BOOM
2-114
18. TELESCOPIC AND DERRICK CYLINDER
2-118
18.1 TELESCOPIC CYLINDER
2-118
18.2 TELESCOPIC CYLINDER HYDRAULIC CIRCUIT SYSTEM
2-120
18.3 COUNTER BALANCE VALVE (FOR TELESCOPIC AND DERRICK CYLINDER)
2-121
18.3.1 STRUCTURE
2-121
18.3.2 TROUBLE SHOOTING
2-121
18.3.3 FUNCTION
2-122
18.4 SEQUENCE VALVE (FOR TELESCOPIC CYLINDER)
2-123
18.4.1 FUNCTION
2-123
18.5 MECHANICAL CHECK VALVE (FOR TELESCOPIC CYLINDER)
2-124
18.6 LEFT SIDE DERRICK CYLINDER
2-126
18.7 RIGHT SIDE DERRICK CYLINDER
2-128
19. WINCH
2-130
19.1 WINCH EXTERIOR VIEW
2-130
19.2 WINCH UNIT EXTERIOR VIEW
2-132
19.2.1 OUTLINE OF WINCH UNIT
2-133
19.3 HYDRAULIC OIL MOTOR
2-134
Summary of Contents for MC405C-3
Page 2: ......
Page 10: ...1 2 1 SPECIFICATION DIMENSIONAL DRAWING...
Page 11: ...1 3 2 DIMENSIONAL DRAWING OF OUTRIGGER WIDTH...
Page 15: ...1 7 4 WORKING RADIUS AND LIFTING HEIGHT...
Page 16: ...1 8 5 WORKING RADIUS AND LIFTING HEIGHT PICK CARRY...
Page 21: ...1 13 8 POWER TRAIN DRAWING 21 5MPa 220kgf cm2...
Page 22: ...1 14 This Page Intentionally Left Blank...
Page 24: ...2 2 This Page Intentionally Left Blank...
Page 25: ...2 3 1 HYDRAULIC CIRCUIT DIAGRAM 21 5MPa 220kgf cm2 21 5MPa 220kgf cm2...
Page 26: ...2 4 This Page IntentionallyLeftBlank...
Page 27: ...2 5 1 1 HYDRAULIC UNITS LAYOUT DIAGRAM...
Page 28: ...2 6...
Page 29: ...2 7 This Page Intentionally Left Blank...
Page 32: ...2 10 2 2 CRANE FIXED PARTS crane control valve rotary joint slewing motor...
Page 36: ...2 14 2 3 TRAVEL LINE travel control valve terminal assembly travel motor...
Page 38: ...2 16 2 4 OUTRIGGER LINES...
Page 39: ...2 17...
Page 50: ...2 28 2 5 PUMP LINE P line...
Page 54: ...2 32 2 6 TANK DRAIN LINE T Dr line...
Page 59: ...2 37 This Page Intentionally Left Blank...
Page 60: ...2 38 2 7 PILOT LINE...
Page 63: ...2 41 This Page Intentionally Left Blank...
Page 64: ...2 42 2 8 ELECTRIC POWERED LINE...
Page 66: ...2 44 3 TANK 3 1 HYDRAULIC TANK...
Page 68: ...2 46 3 2 FUEL TANK...
Page 73: ...2 51 This Page Intentionally Left Blank...
Page 74: ...2 52 6 ENGINE ASSEMBLY 6 1 ENGINE ASSEMBLY 3TNV88F EPMB Yanmar...
Page 76: ...2 54 6 3 NAME OF EACH SECTION...
Page 81: ...2 59 This Page Intentionally Left Blank...
Page 90: ...2 68 6 10 FUEL PIPING...
Page 95: ...2 73 This Page Intentionally Left Blank...
Page 111: ...2 89 10 2 HYDRAULIC CIRCUIT DIAGRAM 21 5 MPa 220 kgf cm2...
Page 112: ...2 90 10 3 RGB BLOCK...
Page 114: ...2 92 10 4 ACCELERATOR BLOCK 10 5 FUNCTION BLOCK DERRICK WINCH TELESCOPIC SLEWING...
Page 117: ...2 95 This Page Intentionally Left Blank...
Page 121: ...2 99 This Page Intentionally Left Blank...
Page 127: ...2 105 This Page Intentionally Left Blank...
Page 130: ...2 108 15 ROTARY JOINT 15 1 EXTERIOR VIEW AND SPECIFICATIONS...
Page 132: ...2 110 16 HOOK BLOCK...
Page 135: ...2 113 This Page Intentionally Left Blank...
Page 136: ...2 114 17 BOOM...
Page 139: ...2 117 This Page Intentionally Left Blank...
Page 140: ...2 118 18 TELESCOPIC AND DERRICK CYLINDER 18 1 TELESCOPIC CYLINDER...
Page 142: ...2 120 18 2 TELESCOPIC CYLINDER HYDRAULIC CIRCUIT SYSTEM...
Page 144: ...2 122 18 3 3 FUNCTION 1 When Neutral 2 When Extended 3 When Retracted...
Page 147: ...2 125 This Page Intentionally Left Blank...
Page 148: ...2 126 18 6 LEFT SIDE DERRICK CYLINDER...
Page 150: ...2 128 18 7 RIGHT SIDE DERRICK CYLINDER...
Page 152: ...2 130 19 WINCH 19 1 WINCH EXTERIOR VIEW...
Page 159: ...2 137 This Page Intentionally Left Blank...
Page 163: ...2 141 This Page Intentionally Left Blank...
Page 166: ...2 144 20 SLEWING SYSTEM 20 1 EXTERIOR VIEW...
Page 171: ...2 149 This Page Intentionally Left Blank...
Page 172: ...2 150 21 OUTRIGGER 21 1 FRONT OUTRIGGER...
Page 174: ...2 152 21 2 REAR OUTRIGGER...
Page 176: ...2 154 22 OUTRIGGER CYLINDER 22 1 OUTRIGGER SLIDE CYLINDER...
Page 178: ...2 156 22 2 SINGLE CHECK VALVE FOR OUTRIGGER SLIDE CYLINDER...
Page 180: ...2 158 22 3 FRONT OUTRIGGER CYLINDER...
Page 182: ...2 160 22 4 REAR OUTRIGGER CYLINDER...
Page 185: ...2 163 This Page Intentionally Left Blank...
Page 186: ...2 164 23 ASSEMBLY AND DISASSEMBLY OF BOOM...
Page 193: ...2 171 24 ELECTRIC CIRCUIT DIAGRAM 1 2...
Page 194: ...2 172 ELECTRIC CIRCUIT DIAGRAM ENGINE 2 2...
Page 195: ...2 173 25 ELECTRICAL WIRING SYSTEM DIAGRAM...
Page 196: ...2 174 This Page IntentionallyLeftBlank...
Page 197: ...2 175 This Page Intentionally Left Blank...
Page 198: ...2 176 26 ELECTRIC SYSTEM 26 1 ENGINE HARNESS 104 1212200...
Page 201: ...2 179 This Page Intentionally Left Blank...
Page 202: ...2 180 26 2 REMOTE CONTROLLER VALVE ELECTRIC HARNESS 104 1212300...
Page 204: ...2 182 26 3 MOMENT LIMITER HARNESS 104 1212500...
Page 206: ...2 184 26 4 ELECTRIC HARNESS 104 2213400...
Page 208: ...2 186 26 5 OVER WINDING DETECTOR 104 2111400...
Page 211: ...2 189 This Page Intentionally Left Blank...
Page 212: ...2 190 26 6 TIP OVER WARNING DEVICE 104 3436600 Unit No 16 or after...
Page 214: ...2 192 This Page Intentionally Left Blank...
Page 216: ...3 2 1 MOMENT LIMITER RELATED 1 1 DISPLAY UNIT AND CONVERTER...
Page 218: ...3 4 1 2 FRONT OUTRIGGER EXTENSION DETECTOR...
Page 220: ...3 6 1 3 REAR OUTRIGGER EXTENSION DETECTOR...
Page 222: ...3 8 1 4 BOOM DISPLACEMENT DETECTOR...
Page 224: ...3 10 1 4 1 ANGLE SENSOR...
Page 226: ...3 12 1 4 2 LENGTH SENSOR CODE REEL...
Page 230: ...3 16 1 6 MOMENT LIMITER ACCESSORY...
Page 232: ...3 18 1 7 OVER UN WINDING DETECTOR...
Page 234: ...3 20 1 8 PICK AND CARRY RELATED...
Page 236: ...3 22 2 OUTRIGGER SAFETY DEVICE 2 1 ROTARY POSITION DETECTOR...
Page 238: ...3 24 2 2 GROUND SETTING DETECTOR...
Page 240: ...3 26 2 3 BOOM STOWING POSITION DETECTOR...
Page 243: ...3 29 This Page Intentionally Left Blank...
Page 244: ...3 30 4 EXTERNAL VIEW OF MOMENT LIMITER 4 1 DISPLAY UNIT...
Page 245: ...3 31 4 2 CONVERTER...
Page 246: ...3 32 5 BLOCK DIAGRAM contact...
Page 254: ...3 40 9 DISPLAYS...
Page 291: ...3 77...
Page 311: ...4 19 Chart 1...
Page 312: ...4 20 2 2 CONTROL PRINT CARD LACATIONS 2 2 1 MAIN PRINT CARD UPPER SIDE MC9141 A...
Page 313: ...4 21 2 2 2 MAIN PRINT CARD LCD DISPLAY UPPER SIDE MC9141 A...
Page 314: ...4 22 2 2 3 SUB PRINT CARD LOWER SIDE MC9143 A...
Page 315: ...4 23 2 2 4 SUB PRINT CARD LCD DISPLAY LOWER SIDE MC9143 A...
Page 316: ...4 24 2 3 CONNECTOR PIN ASSIGNMENT Receiver has two connectors for Input Output...
Page 326: ...4 34 This Page Intentionally Left Blank...
Page 328: ...5 2 1 ELECTRIC MOTOR 1 Power unit 2 Electric motor 3 Coupling 4 Hydraulic pump...
Page 330: ...5 4 2 1 STRUCTURAL DRAWING...
Page 353: ...5 27...
Page 354: ...5 28 4 ELECTRIC CIRCUIT DIAGRAM...
Page 355: ...5 29...
Page 356: ...5 30 This Page Intentionally Left Blank...
Page 358: ......