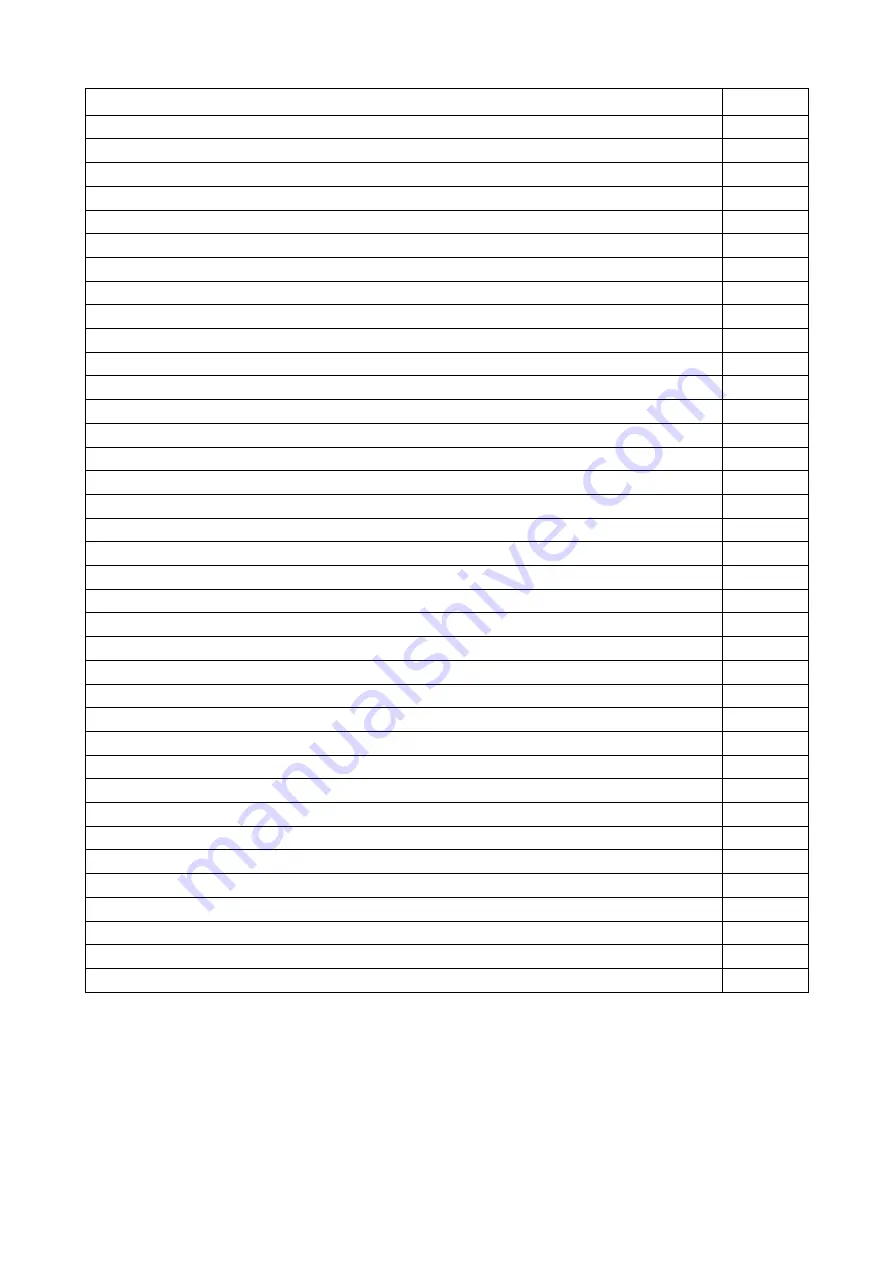
0-5
ITEM
Page
10. MAINTENANCE PROCEDURES
4-16
10.1 INITIAL 500 HOUR MAINTENANCE
4-16
10.2 CHECKING BEFORE OPERATION
4-16
10.3 IRREGULAR MAINTENANCE
4-17
10.4 MAINTENANCE EVERY 50 HOURS
4-36
10.5 MAINTENANCE EVERY 100 HOURS
4-38
10.6 MAINTENANCE EVERY 250 HOURS
4-39
10.7 MAINTENANCE EVERY 500 HOURS
4-41
10.8 MAINTENANCE EVERY 1000 HOURS
4-46
10.9 MAINTENANCE EVERY 1500 HOURS
4-48
10.10 MAINTENANCE EVERY 2000 HOURS
4-49
SPECIFICATIONS
5- 1
1. SPECIFICATION LIST
5- 2
2. SPECIFICATION DIMENSIONAL DRAWING
5- 3
3. RATED TOTAL LOAD CHART
5- 4
4. WORKING RADIUS AND LIFTING HEIGHT
5- 7
SEARCHER HOOK
6- 1
1. SEARCHER HOOK EACH SECTION
6- 2
2. MOMENT LIMITER DISPLAY UNIT
6- 3
3. OPERATION
6- 5
4. INSPECTION AND MAINTENANCE
6- 8
4.1 LEGAL INSPECTION
6- 8
4.2 CONSUMABLES
6- 8
4.3 INSPECTION AND MAINTENANCE LIST
6- 8
4.4 MAINTENANCE PROCEDURES
6- 9
4.4.1 INSPECTION OF BEFORE OPERATION
6- 9
5. WORKING RADIUS AND RATED TOTAL LOAD
6-11
5.1 WORKING RADIUS AND LIFTING HEIGHT FOR SEARCHER HOOK
6-11
5.2 RATED TOTAL LOAD CHART FOR SEARCHER HOOK
6-12
Summary of Contents for LC383M-5
Page 2: ......
Page 8: ...0 6...
Page 22: ...1 14...
Page 56: ...2 34 SAFETY LABEL LOCATIONS ON CHASSIS...
Page 61: ...2 39 14 Warning for lifting position 584 3437800 15 Caution for lifting machine 541 3472400...
Page 198: ...3 134...
Page 235: ...4 37...
Page 250: ...4 52...
Page 253: ...5 3 2 SPECIFICATION DIMENSIONAL DRAWING...
Page 258: ...5 8 2 WORKING RADIUS AND LIFTING HEIGHT AT WIRE ROPE 2 FALLS...