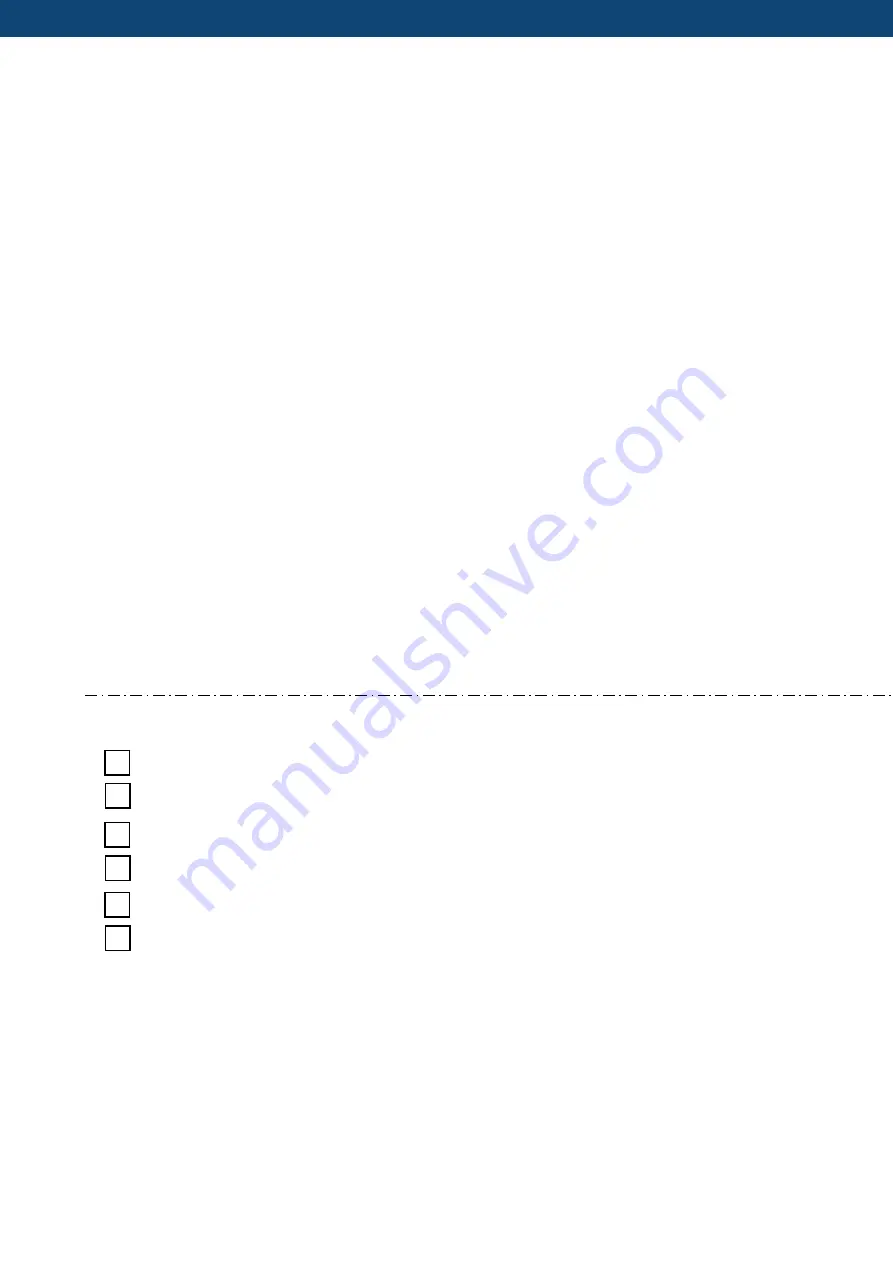
40
Flow Rates
OPTIMUM FLOW RATE DIFFERENTIAL FROM INLET TO OUTLET IS BETWEEN 2-3
DEGREES
Each Pool Heat Pump has a minimum flow rate requirement please check the specification table to ensure the
circulation pump in use is adequately sized.
Calibrating the flow rate
By using the running status function on the touch controller, it is easy to calibrate the check valves installed
for optimum flow rates through the heat pump.
Madimack Heat Pumps have a built-in flow switch which will deactivate the heating function if not enough
water flow is detected. The Heat Pump has a large range operation up to a seven-degree differential. If the
temperature differential is above 7 degrees, the built-in flow switch or E6 Error will be displayed indicating
not enough flow detected.
Recommended procedure
1.
Open all isolating valves
2.
Fully close the by-pass and switch the unit on to max temp.
3.
Wait 3-4 minutes until heat pump is at 100% Capacity
4.
Check inlet and outlet temperature through on-screen controller (Check “Running status check” in the
previous section to obtain C0 and C1 values)
5.
Open the by-pass valve to increase temperature differential (The difference between C0 and C1
values)
6.
Close the by-pass valve to decrease temperature differential (The difference between C0 and C1
values)
7.
Once optimum temperature difference (2-3 C) achieved lock position of by-pass if possible.
Checklist:
Unit has been installed level
Minimum ventilation requirements are correct to standards show in appendix K
Condensation drain pipe has been connected and drains away from unit
Rubber feet have been placed underneath unit
Warranty registration details have been filled out in section L
Temperature differential has been calibrated between 2-3
Summary of Contents for ECO
Page 1: ...1...
Page 2: ...INDEX...
Page 5: ...5 Safety Precautions b...
Page 8: ...8 About your heat pump c...
Page 13: ...13 Installation Guidance d...
Page 26: ...26 Operation Guidance e...
Page 30: ...30...
Page 31: ...31 2...
Page 32: ...32...
Page 33: ...33...
Page 34: ...34...
Page 35: ...35 Testing f...
Page 39: ...39 g Commissioning...
Page 41: ...41 Maintenance h...
Page 43: ...43 Troubleshooting for common faults i...
Page 51: ...51...