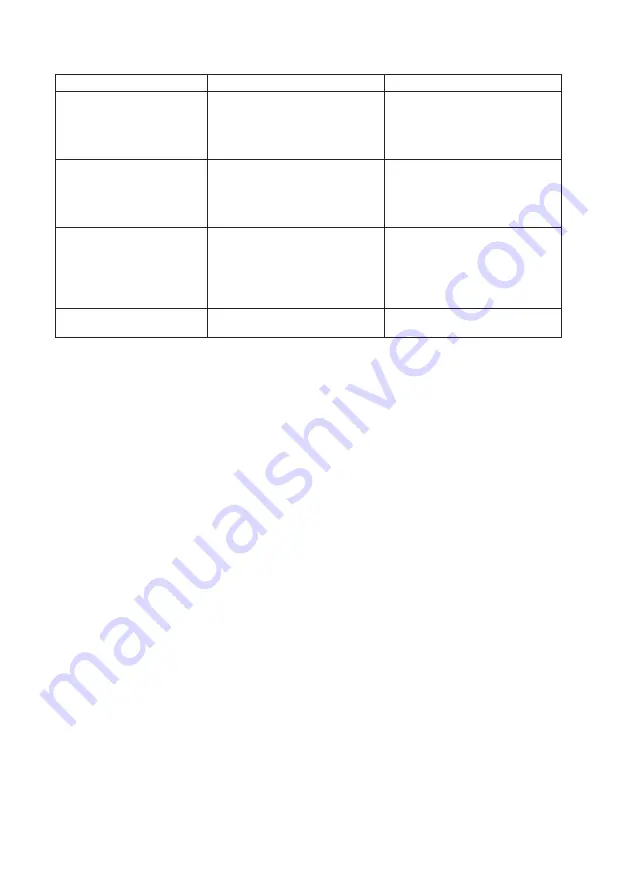
E5
TROUBLE SHOOTING
If the pump has anything wrong, please contact dealer us
We don’t recommend customer repair the pump themselves.
STORAGE AND MAINTENANCE
Pumps are delivered in appropriate carton boxes. Packaging material should be properly
disposed.
Handling and storage of the new pump do not require any special procedures.
However after the pump has been used, empty the used oil in the suction tube into an
appropriate container. This is done by overturning the pump.
The dust in compressed air can slow down and even block the motor cylinder. The following
steps may prevent this from happening:
1. Let in 50 gram of Vaseline oil or other lubricator from the air inlet hole weekly, operate the
pump for several minutes after having lubricator.
2. Turn on the pump for several minutes until moving parts is fully lubricated.
3. You may repeat the above operation if necessary.
4. The above steps should be carried out on a weekly base.
For the pumps that are attached with compressed air treatment equipment, please empty the
water retained in the reservoir of the filter-purger frequently.
For the pumps that are attached with a lubricator, please pay close attention to the lubricator’s
oil level and refill with SAE 20, SAE 30 or antifreeze oil for extreme conditions when necessary.
NOTE:
The user should perform only routine maintenance operations (such as filters, silencers,
cleaning…) with the pump in order not to damage it or compromise its safety.
Contact our sales or service center when the pump needs further maintenance.
Problem
The pump continues to operate
after the gun trigger has been
released.
Reduction of the oil delivery.
or reduced pressure in the
oil delivery.
Air loss through the air
exhaust.
Oil leaks through the air
exhaust.
Solution
Cause
1. The is a oil leak at some point of
the circuit.
2. Valve sets (part No.39, 40, 41)
close incorrectly due to dirt or
wearing.
1. Silencer (53) dirtied.
2. Blocked at some point of the oil
circuit.
3. Ball valve set (35, 36) closes
incorrectly due to dirt or wearing.
1. The sliding valve (4) does not
close properly.
2. Broken press piece (5).
3. Damaged O-ring (21, 21).
4. Damaged piston (50).
5. Broken spring (18).
Seal set (45, 46, 47) damaged.
1. Check and tighten unions. Repair
the leak.
2. Substitute damaged elements.
1. Clean or recharge silencer.
2. Use clean oil.
3. Substitute damaged elements.
1. Disassemble and clean.
Substitute in case of damage.
2. Substitute damaged elements.
Substitute damaged elements.
Summary of Contents for OKTR585-1-001
Page 9: ...E7 EXPLODED AND PARTS LIST 5 1 OIL PUMP...
Page 23: ......