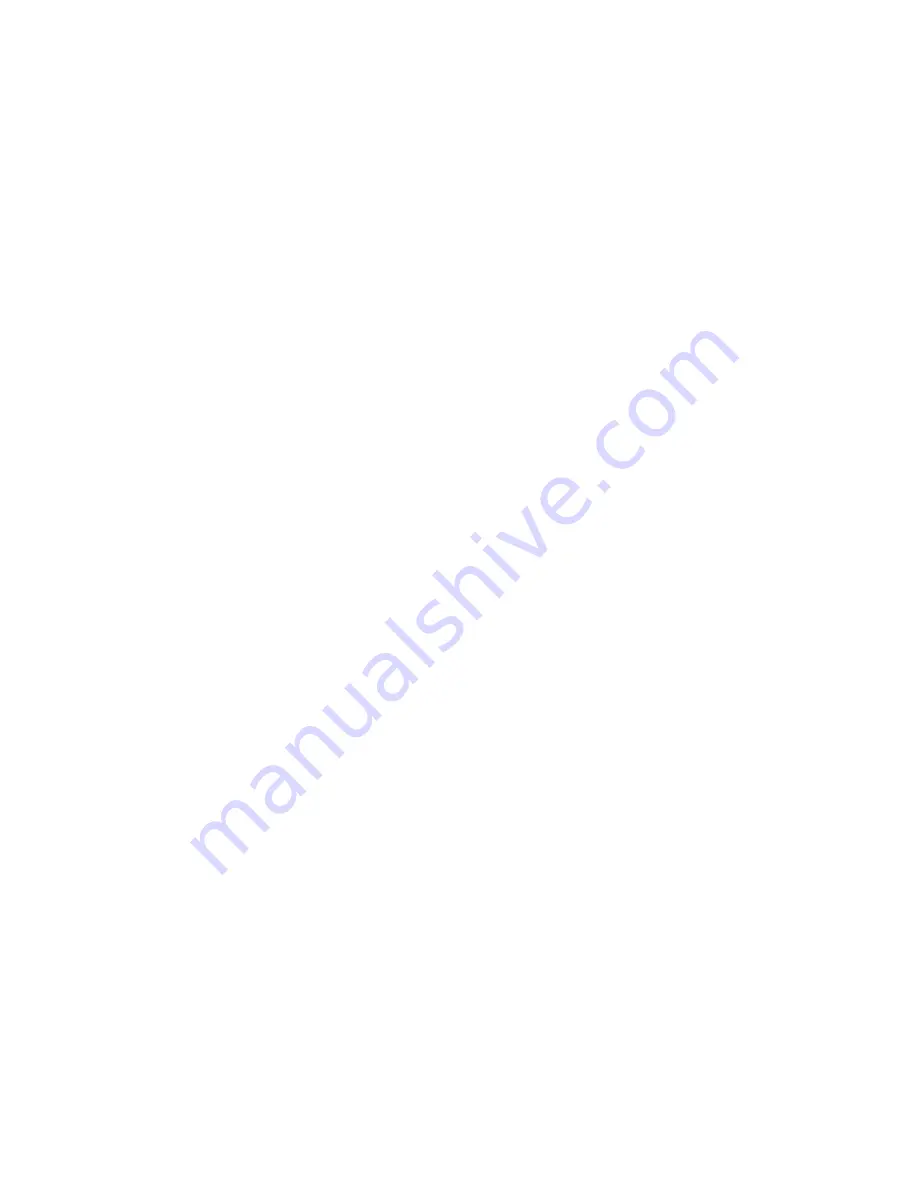
6
Tailstock barrel Steel barrel bored with No.2 Morse taper to mount various tooling,
centers, drill chuck, reamers etc. the barrel has a travel of 50mm, this
travel allows the mounted tool or centre to be brought into controlled
contact with the work piece.
Mounting feet
Shaped in the casting of the lathe bed, the two feet have 14mm slots cut
into them to enable the fitting of two 12mm bolts to effect the rigid
fastening of lathe onto it’s stand? A work bench?
Lathe bed
V rail and flat rail bed, precision machined to provide an accurate
mounting for the headstock and a precision guide for the movement of
the saddle. It also mounts the tailstock in an accurate relationship to the
main axis of the lathe.
Saddle
Main casting that is precision machined to marry with the lathe bed. It
moves parallel to the mail axis. It mounts the traverse slide. It also
mounts its control handle and the auto feed or thread cutting engaging
lever.
Saddle control
This engineers wheel / control handle is mounted on a shaft that goes
through the apron of the saddle; there is a pinion mounted on the end of
shaft that is permanently engaged with the fixed rack on the lathe bed.
This enables the saddle to be moved back and forth along the lathe bed.
N.B. Remember this handle is PERMANENTLY engaged to the rack and
during thread cutting or auto feeding will turn with the movement of the
saddle.
Auto feed lever This lever engages the saddle to the leadscrew to enable the auto feed
or the thread cutting function of the lathe. Move the lever down to
engage the feed. As there is no synchronising dial indicator fitted for
thread cutting – to ensure correct “pick-up” during thread cutting, leave
the auto feed lever engaged. Disengage the tool clear of the work. Stop
the spindle, electrically reverse the drive system and drive tool back
clear of the working piece – stop the spindle: switch back to normal –
and set the new cutting depth and restart the machine; repeat this
procedure until the thread is cut.
Traverse slide
Mounted on a ‘V’ machined slide on the saddle. The accuracy of the fit of
the ‘V’ slide is maintained by the ‘gybe’ strips set in the offside of the
traverse slide.
Traverse slide
control handle
A ’U’ handle, mounted on a shaft that is anchored into a housing cast at
the front of the traverse slide, the shaft is threaded and is engaged in a
fixed thread follower on the slide, enabling the traverse slide to be driven
back and forth across the saddle perpendicular to the main axis. There is
a graduated ring (thimble) on the neck of the handle to allow the
movement of the slide to be measured.
Compound
slide
The compound slide is mounted on a machined ‘V’ slide with a circular
base, that is then mounted and located on the top of the traverse slide
by a central pivot. Through the circular block, near the edge, are two
diametrically opposed nuts and bolts; the bolt shanks extend through two
concentric slots machined in the traverse slide that allow the compound
slide mount to turn about the central pivot. The nuts on the ends of the
bolts (in machined recesses under the front and back edge of the slide)
also lock the compound slide along its selected axis (+ or – 45 degrees
from the main axis).
The compound slide fits over this ‘vee’ slide mount; the accuracy of the