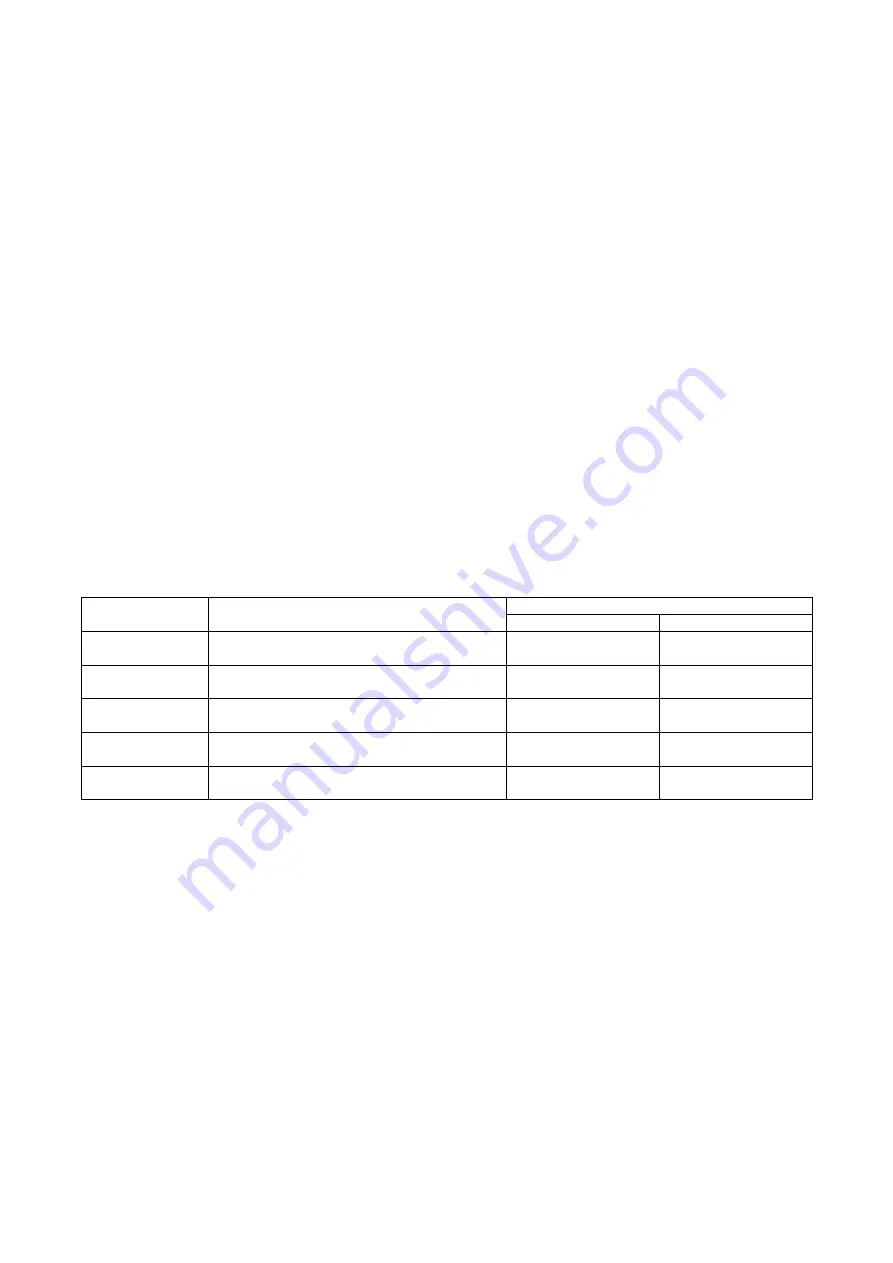
18
SC100/200 Series Function Block Application Manual EM-6460-C
4.2.5 PID CONTROL
PID control transfer function is expressed with the following formula:
100 1 (1 − 1 /
m
)
T
D
s
G
(
s
) = –––— ×
{
1 + –––– + ––––––––––––—
}
PB
T
I
s
(1 +
T
D
s
/
m
)
where
PB
= Proportional band
T
I
= Integral time
T
D
= Derivative time
m
= Derivative gain (= 8)
s
= Laplace operator
The first term on the right side represents the proportional control function, which provides an output proportional to devia-
tion.
The second term represents the integral control function, which provides an output proportional to an integration of deviation.
The third term represents the derivative control function, which provides an output proportional to a rate-of-change of devia-
tion.
Respective time constants for the integral and the derivative are completely independent from each other in the above equa-
tion, therefore each control strategy can be achieved without interference.
•
Control direction (ITEM 40)
Used to determine the relation between the increasing/decreasing of deviation (= PV − SP) and the manipulated output.
Direct action:
The output increases when the deviation increases.
Reverse action: The output decreases when the deviation increases.
Relations between control valve action and control direction
CONTROL LOOP
VALVE LOCATION / CONTROL OBJECT
CONTROL DIRECTION
DIRECT ACTION VALVE
REVERSE ACTION VALVE
Temperature control
Heating
Cooling
Direct
Reverse
Reverse
Direct
Pressure control
Upstream control (release valve)
Downstream control
Reverse
Direct
Direct
Reverse
Flow control
Valve connected in series with a sensing element
Return valve (pump bypass valve)
Direct
Reverse
Reverse
Direct
Level control
Tank inlet
Tank outlet
Direct
Reverse
Reverse
Direct
pH control
Alkali
Acid
Direct
Reverse
Reverse
Direct
Remark: Control valve action
Direct action: Opening 100% at 4 mA (Air to Close)
Reverse action: Opening 0% at 4 mA (Air to Open)
•
Derivative method (ITEM 41)
Choose either PV derivative or deviation derivative according to the user’s application needs. In general, PV derivative set-
ting, in which the derivative action is inactive at a setpoint change, does not give unnecessary disturbance to the process.
However, the deviation derivative setting may produce a better control result when the secondary loop in cascade control is
set with derivative action.
•
Proportional band (ITEM 42)
Choose between 1 and 1000%.
•
Integral time (ITEM 43)
Choose between 0.00 to 100.00 minutes. The integral action is cancelled when ‘0.00’ is set.
•
Derivative time (ITEM 44)
Choose between 0.00 to 10.00 minutes. The derivative action is cancelled when ‘0’.00 is set.