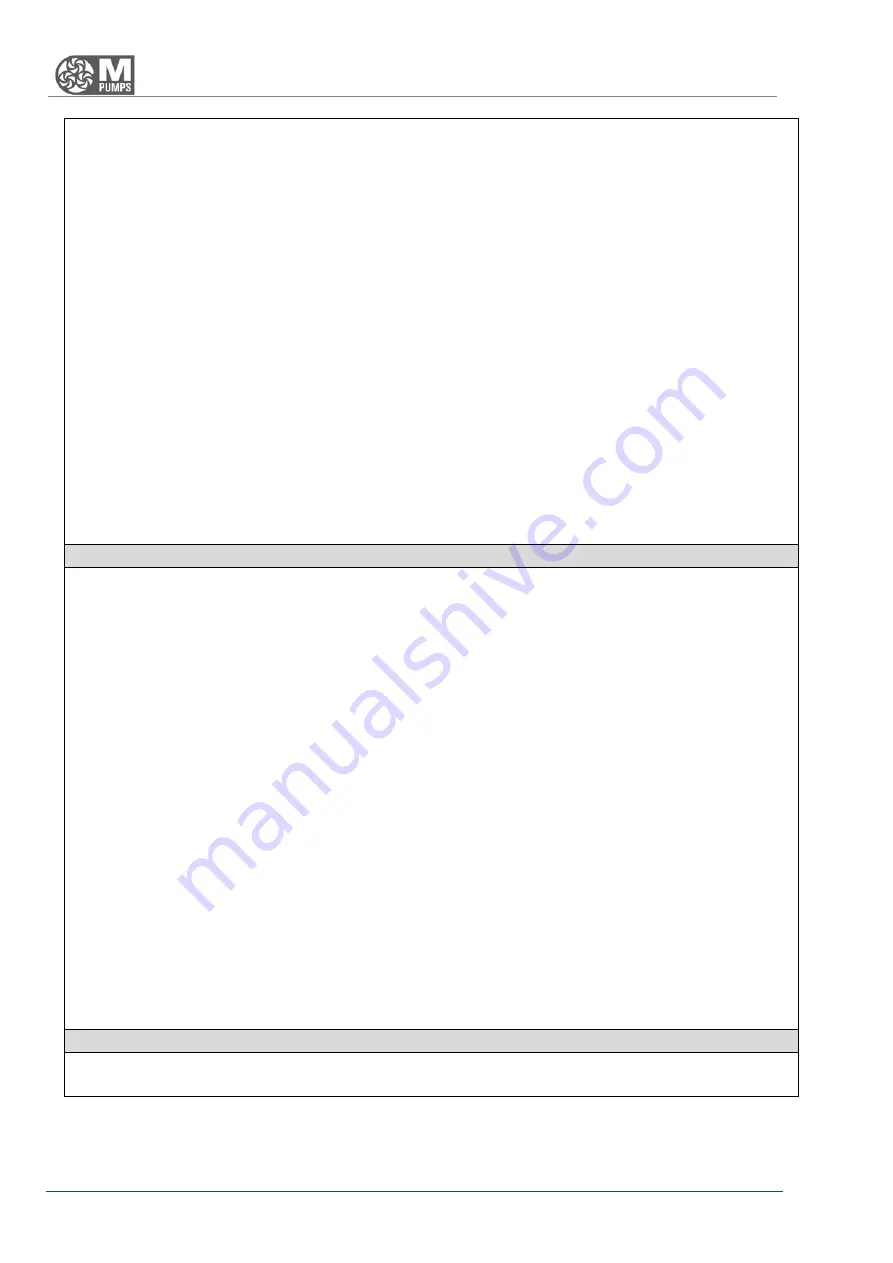
Pag. 18/33
ISM0210 Instruction Manual of series SCE - Rev.03
The liquid contains air or steam. The liquid
produces foam.
Check the presence of vortices in the suction line. Enter
some in the fuel tank to prevent the formation of vortices.
Install a tank of sufficient capacity in the suction line to allow
gas to drag
.
Insufficient inlet pressure, with the
generation of cavitation and loss of
efficiency
.
Increase the static height at the suction
.
Check that the intake is not blocked or are no bottlenecks.
Reduce the liquid temperature. Increase the diameter of the
intake pipes.
Reduce the length of inlet pipes. Open completely the inlet
valve. Check the viscosity of the liquid; refer to "technical
data" section of this manual, increase the temperature of the
liquid if necessary.
Wear ring, wear pump casing or impeller.
Check the condition of rotating ring wear and collar. Replace
if worn; refer to Chapter 10 of this manual
.
The temperature of the liquid is close to
boiling point
Reduce the liquid temperature
.
NO FLOW
Causes
Remedies / actions
The pump is defused
Re-prime the pump. Refer to section 3.5.1 of this manual.
Check for air leaks in the suction line
Suction line blocked
Ensure that there are no blind pipes, obstructed or valves
closed
.
The magnetic coupling decouples
Reduce the flow: partially close the discharge valve. Reduce
the density of the liquid, if possible. Reduce the prevalence
of the pump (check in advance with your distributor
M PUMPS PROCESS
). Make sure the pump turns freely;
inspect the inside in case this does not happen. Reduce the
engine power installed (check in advance with your
distributor
M PUMPS PROCESS
). Adopt star-delta starting
.
The motor stopped
Check the power of the motor. Check the status of the
motor.
EXCESSIVE FLOW
Causes
Remedies / actions