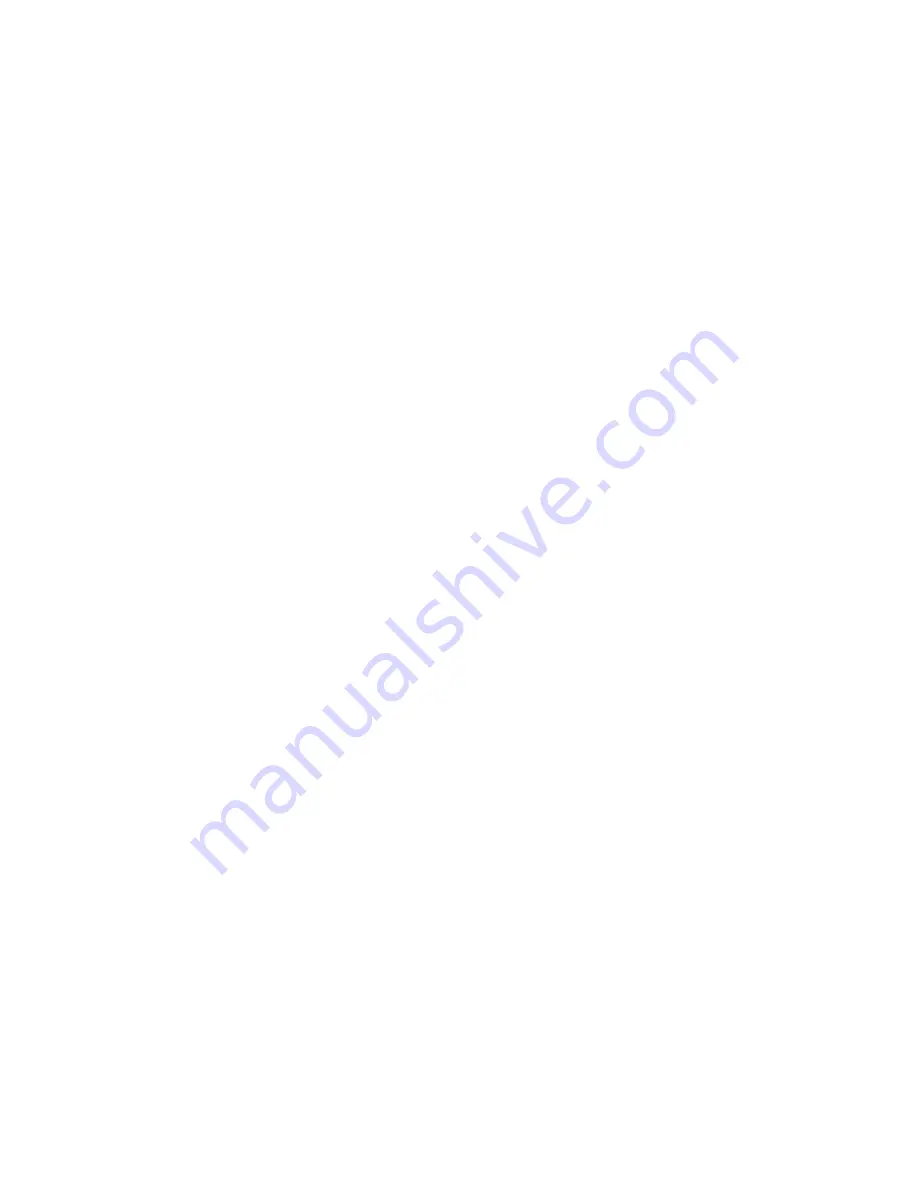
SECTION 5
LYCOMING OPERATOR’S MANUAL
MAINTENANCE PROCEDURES
IO-320 SERIES
b. Oil Suction and Oil Pressure Screens –
At each 25-hour inspection remove, inspect for metal
particles, clean and reinstall, not to exceed four (4) months between oil changes.
NOTE
On installations employing full flow oil filters, this step is not practical at this time, but
should be observed at the 50-hour inspection, not to exceed four (4) months between oil
changes.
(1)
Non-Adjustable Oil Pressure Relief Valve –
The function of the oil pressure relief valve is to
maintain engine oil pressure within specified limits. The valve, although not adjustable, may be
controlled by the addition of a maximum of nine (9) P/N STD-425 washers under the cap to
increase the pressure or the use of a spacer (Lycoming P/N 73629 or 73630) to decrease pressure.
A modification on later models has eliminated the need for the spacers. Particles of metal or other
foreign matter lodged between the ball and seat will result in faulty readings. It is advisable,
therefore, to disassemble, inspect and clean the valve if excessive pressure fluctuations are noted.
(2)
Oil Pressure Relief Valve (Adjustable) –
The adjustable oil relief valve enables the operator to
maintain engine oil pressure within the specified limits. If the pressure under normal operating
conditions should consistently exceed the maximum or minimum specified limits, adjust the valve
as follows:
With the engine warmed up and running approximately 2000 RPM, observe the reading on the
oil pressure gage. If the pressure is above maximum or below minimum specified limits, stop
engine and screw the adjusting screw outward to decrease pressure or inward to increase pressure.
Depending on installation, the adjusting screw may have only a screw driver slot and is turned
with a screw driver; or may have the screw driver slot plus a pinned .375-24 castellated nut and
may be turned with either a screw driver or a box wrench.
4. CYLINDERS.
It is recommended that as a field operation, cylinder maintenance be confined to
replacement of the entire assembly. For valve replacement, consult the proper overhaul manual. This should
be undertaken only as an emergency measure.
a. Removal of Cylinder Assembly.
(1) Remove exhaust manifold.
(2) Remove rocker box drain tube, intake pipe, baffle and any clips that might interfere with the
removal of the cylinder.
(3) Disconnect ignition cables and remove the bottom spark plug.
(4) Remove rocker box cover and rotate crankshaft until piston is approximately at top center of the
compression stroke. This approximate position may be located by observing top of piston through
the spark plug hole and also watching the valve action.
5-6
Summary of Contents for AIO-320
Page 9: ...LYCOMING OPERATOR S MANUAL vi ...
Page 11: ...This Page Intentionally Left Blank ...
Page 15: ...This Page Intentionally Left Blank ...
Page 17: ...This Page Intentionally Left Blank ...
Page 23: ...This Page Intentionally Left Blank ...
Page 39: ...This Page Intentionally Left Blank ...
Page 41: ...This Page Intentionally Left Blank ...
Page 47: ...This Page Intentionally Left Blank ...
Page 59: ...This Page Intentionally Left Blank ...
Page 65: ...This Page Intentionally Left Blank ...
Page 74: ...LYCOMING OPERATOR S MANUAL SECTION 7 IO 320 SERIES INSTALLATION AND STORAGE 7 9 ...
Page 75: ...SECTION 7 LYCOMING OPERATOR S MANUAL INSTALLATION AND STORAGE IO 320 SERIES 7 10 ...
Page 77: ...This Page Intentionally Left Blank ...
Page 79: ...SECTION 8 LYCOMING OPERATOR S MANUAL TABLES IO 320 SERIES 8 2 ...
Page 80: ...LYCOMING OPERATOR S MANUAL SECTION 8 IO 320 SERIES TABLES 8 3 ...