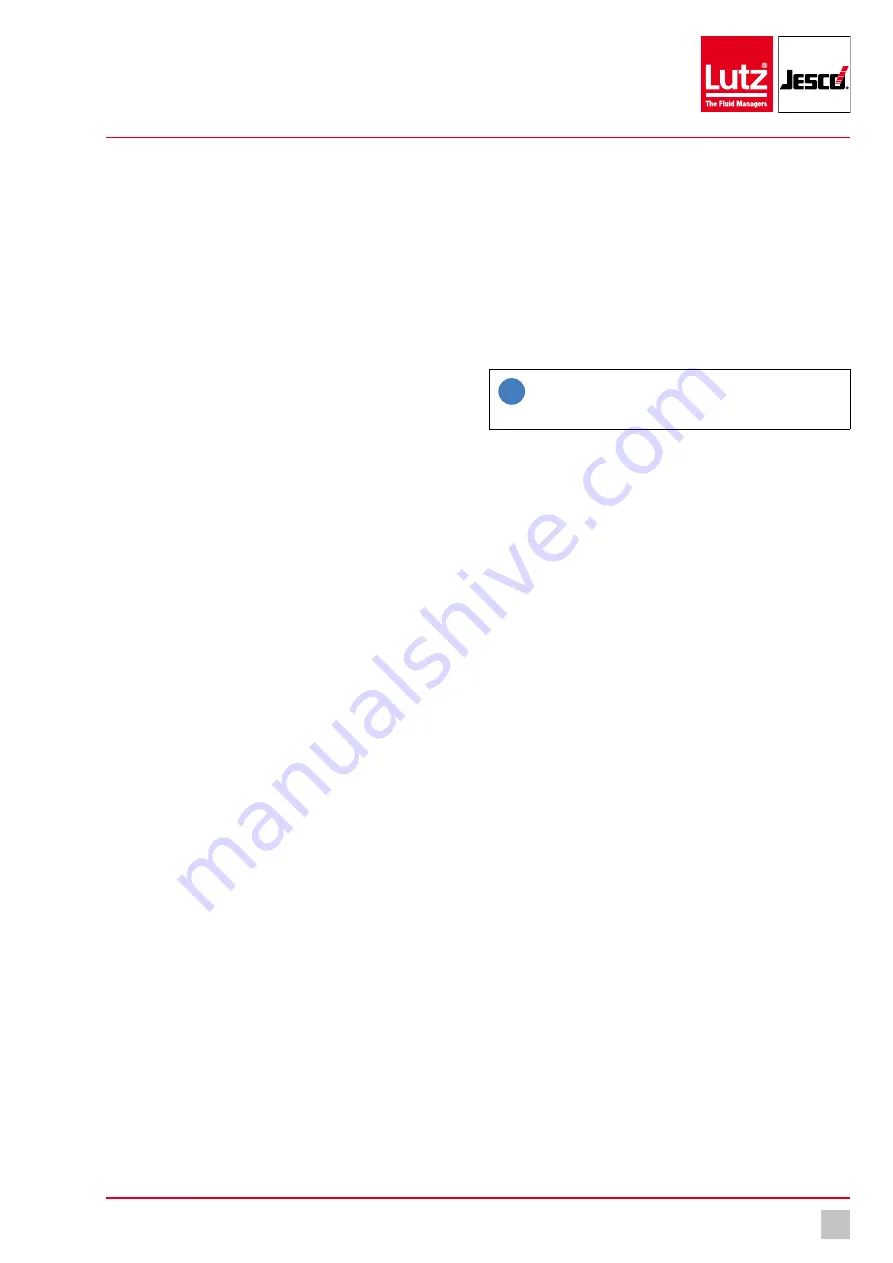
Maintenance
Maintenance on the electrical regulation valve
27
© Lutz-Jesco GmbH 2016
Subject to technical changes.
160520
BA-20901-02-V01
Chlorinator C 2526
Operating instructions
12.5.1 Dismantling the flow meter
Perform the following working steps:
1.
Dismantle the complete flow meter including the mounting angle (1)
from the dosing device.
2.
Remove the four screws (6) and remove the spacer rods (11).
3.
Loosen the screws (7) on the upper and lower limits (14, 19).
4.
Holding onto the measuring glass (16), remove the screws and the
limits, and remove the inlet block (12) and the outlet block (8) from
the flow meter.
5.
Carefully remove the limits from the measuring glass whilst twisting
them slightly.
6.
Unscrew in the valve spindle (10).
7.
Remove the O-ring (9) with a blunt tool.
ü
Flow meter dismantled.
12.5.2 Cleaning the flow meter:
Perform the following working steps:
1.
Clean all parts thoroughly with a soft cloth. Warm water or alcohol is
suitable for this purpose.
2.
Clean the glass tube with e.g. warm water and a flat brush.
3.
Perform a visual check on all parts. Pay especial attention to the
drillhole for the manual dosing valve and the sealing surfaces for the
flat gaskets. Replace the damaged parts.
ü
Flow meter cleaned.
12.5.3 Mounting the flow meter
Precondition for action:
ü
All parts have been dried well after cleaning.
ü
All parts are in a good condition.
Perform the following working steps:
1.
Place the O-ring (13) between the lower limit (14) and the inlet block
(12). Secure the lower limit with the two screws (7).
2.
Mount the O-ring (15) in the groove of the lower limit. Rub it with
silicone grease lightly.
3.
Repeat steps 1 and 2 with the upper limit (19) and the outlet block
(8).
4.
Mount the small thick O-ring (18) on the taps of the upper limit.
5.
Slide the measuring glass (16) onto the lower limit rotating it a little.
6.
Place the float (17) in the measuring glass and slide the upper limit in
the measuring glass.
7.
Place this units on a level surface so that the PVC blocks are aligned
well.
8.
Hold the spacer rods (11) between the inlet and outlet blocks (12, 8)
and mount the screws (6).
9.
Mount the new O-ring (9) on the valve spindle (10). Rub the O-ring
with a little silicone grease. The thread is not greased.
10.
Screw the valve spindle into the outlet block until you feel clear
resistance.
11.
Unscrew in the valve spindle by 10 revolutions.
ü
Flow meter mounted.
12.6 Maintenance on the electrical regulation valve
The electrical regulation valve is optional. Comply with the instructions in
the operating manual of the regulation valve during maintenance.
12.7 Maintenance of the back-pressure regulator
i
For an overview of the components of the back-pressure
regulator, see section 14.5 „Back-pressure regulator“ on page
38.
The back-pressure regulator is cleaned and all elastomers are replaced.
Precondition for action:
ü
The system is prepared in accordance with section 12.3 „Preparing
the system for maintenance“ on page 25.
ü
The fitting maintenance set is available.
@
Cleaning alcohol
@
2 wrenches for mounting the diaphragm
@
Silicone grease
12.7.1 Dismantling the back-pressure regulator
Perform the following working steps:
1.
Dismantle the complete back-pressure regulator including the
mounting angle (7) from the dosing device.
2.
With cabinets, the vacuum meter remains in the device. With wall
devices, dismantle the pressure gauge. Seal the entry of the pressure
gauge to prevent the penetration of air moisture. Further information
about the vacuum meter can be found in section 12.8 „Cleaning the
vacuum meter“ on page 28.
3.
Mark the direction of installation of all housing sections and the
mounting angle with a waterproof marker.
4.
Remove the eight threaded rods (17, 18).
5.
The spring force presses the housing sections apart. Remove the
diaphragm disc (13) and the spring (12).
6.
Loosen the clamping ring (15) on the diaphragm (14). Use the key for
mounting the diaphragm.
7.
Unscrew the reduction (1) from the upper housing section.
ü
Back-pressure regulator dismantled.
12.7.2 Cleaning the back-pressure regulator
Perform the following working steps:
1.
Clean all parts thoroughly with a soft cloth. Warm water or alcohol is
suitable for this purpose.
2.
Allow all components to dry well.
Summary of Contents for C 2526
Page 2: ......
Page 46: ...Index 46 Lutz Jesco GmbH 2016 BA 20901 02 V01 Chlorinator C 2526 Operating instructions...
Page 48: ......