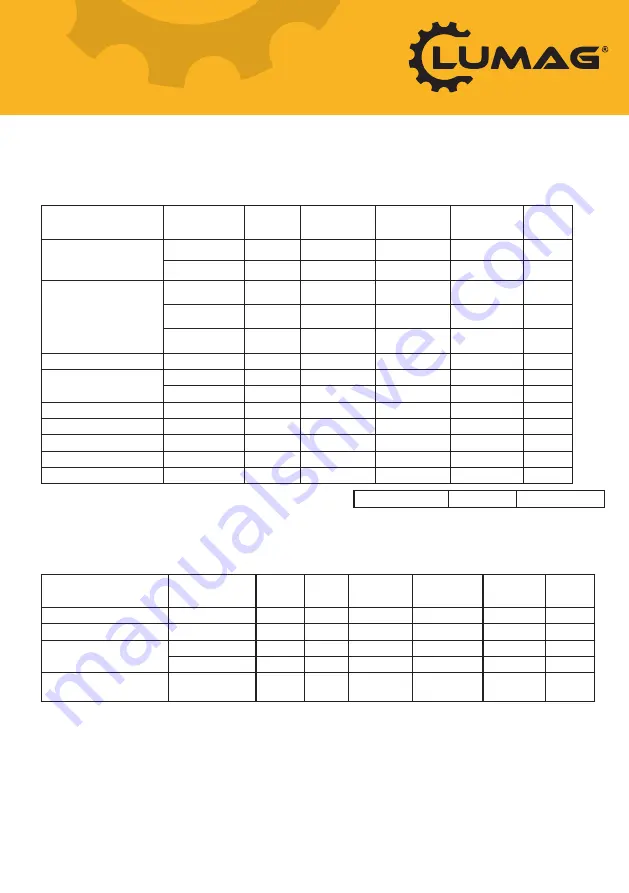
Lumag Servicing and
Maintenance Schedules
Engine Service & Maintenance Schedule
Machine Service & Maintenance Schedule
Item
Checks/Work
Each Use
20hrs
(1st Month)
50hrs
(2nd Month)
100hrs
(6th Month)
300hrs
(Yearly)
Engine Oil
Check Level
X
Change
X (1)
X
Air Filter
Check
X
Clean
X (3)
Replace
X (4)
Sediment Cup
Clean
X
Spark Plug
Check/Clean
X
Replace
X
Idle Speed
Check/Adjust
X (2)
Valve Clearance
Check/Adjust
X (2)
Fuel Tank Strainer
Check/Clean
X (2)
Combuster Chamber
Inspect/Clean
X (2)
Fuel Lines
Check
X (2)
Item
Checks/Work
Each Use Weekly 20hrs
(1st Month)
50hrs
(2nd Month)
100hrs
(6th Month)
300hrs
(Yearly)
Fasteners Tension
Check
X
Clean Machine
Clean
X
Drive Belt
Check/Adjust
X
Replace
X (2)
All Other Moving Parts &
Cables
Lubricate
X
X (2)
Engine Oil
600ml
Lumag Engine 1
1 – First service only, 2 = Should be carried out by your Lumag Dealer, 3 = May need to be done more often in dusty areas &
4 = Replace paper element only
To maximise the life of your Lumag machine it needs to be serviced and maintained at every indicated month or
operating hour interval, whichever comes first, in accordance with the below Schedules. Please note that failure to
service your machine on schedule or use genuine Lumag parts and consumables will result in your warranty being void.