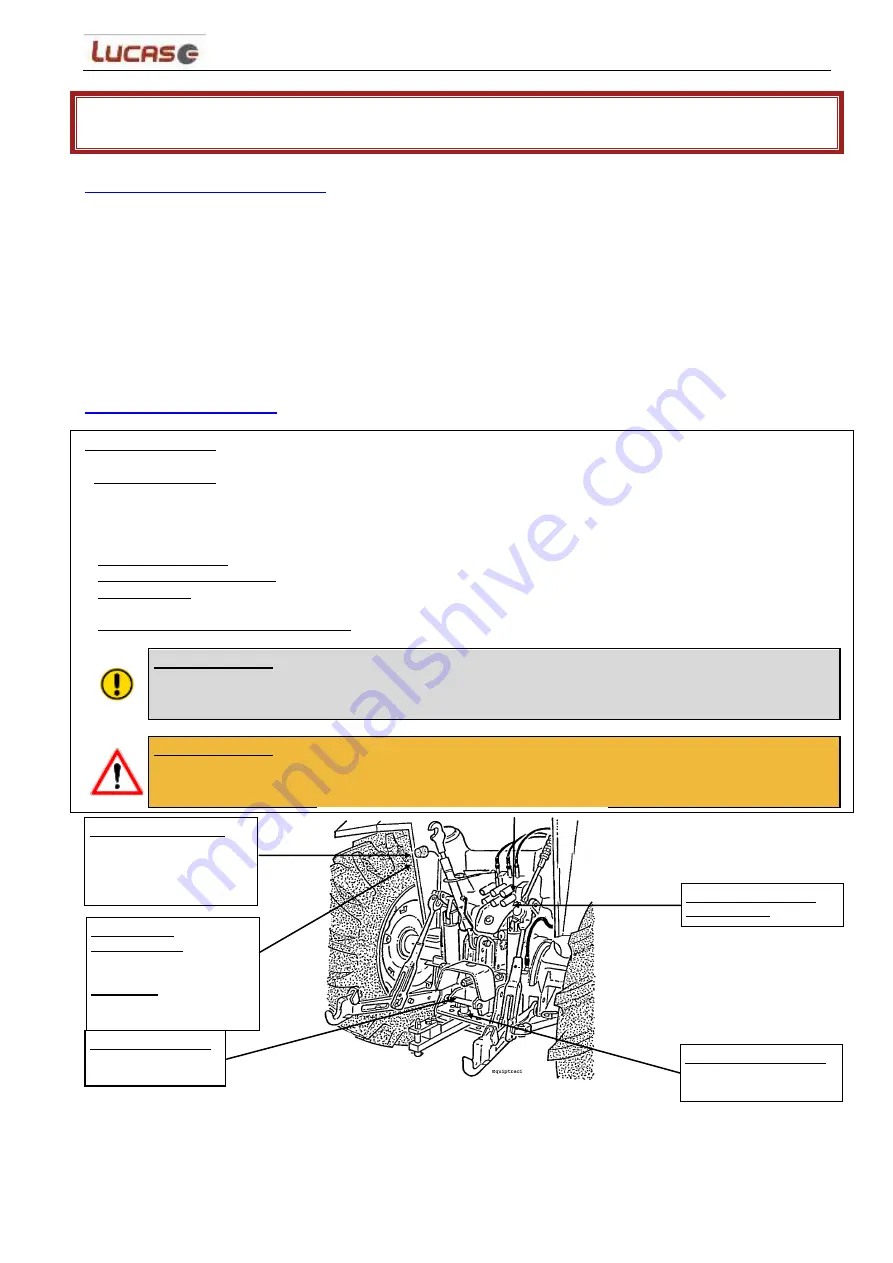
- 9 -
D370-019
1 - START-UP
1.1.
H
ANDLING AND
S
TORAGE
The machine must be stored taking a minimum of precautions :
- Machine on the ground, stable
- Rear door closed and chute in the low position.
- Ensure stems on all actuators are greased when kept in storage. Prior to operation,
these same rods should be cleaned with a cloth moistened with diesel fuel and then
dried with a clean, dry cloth.
- Once uncoupled, the transmission must not be laid on the ground, but must rest on the
mounting provided for the purpose.
- The parking brake on.
1.2.
T
RACTOR FITTINGS
Hydraulic fittings
* Hydraulic source
. A single-acting hydraulic distributor (+ return) or a double-acting one (two female ½ clack valves).
. Distributor maintained in continuous pumping.
. Direct return to the tank recommended so as to reduce oil heating.
. For self-regulating pumps, compulsory return to the bowl.
* Nominal flow rate : L8: 30 l - M8: 40 l - H8: 50 l (L - Low, M - Medium, H - High)
* Maximum pressure (bar) : 160.
* Circuit tape :
. The machines are factory set for open centre hydraulics.
* Closed centre hydraulics adaptation : Consult us
The machine is capable of handling flows of up to 100 l/min. However, in order to save fuel, it is
recommended that you adapt the flow to the belt advance rate being used (L, M, H). Above 55
l/min, the additional flow will be unusable and will use up energy.
In order for the controls to work in the right direction, make sure never to connect the hoses blue
and red mark on the tractor the wrong way around.
OIL POLLUTION IS NOT COVERED BY THE WARRANTY, KEEP THE VALVES CLEAN
ELECTRIC FITTINGS
Standard 12V 7 contact
connector (European
code)
POWER TAKE-OFF
6 straight 1"3/8
splines
EYE BOLT COUPLING
with safety pin or fork
joint coupling
ELECTRICAL
CONNECTION
3 pin 12 volt DIN 9680 for
power supply
CAUTION
: Current
required 25 A
HYDRAULIC BRAKE
CONNECTOR