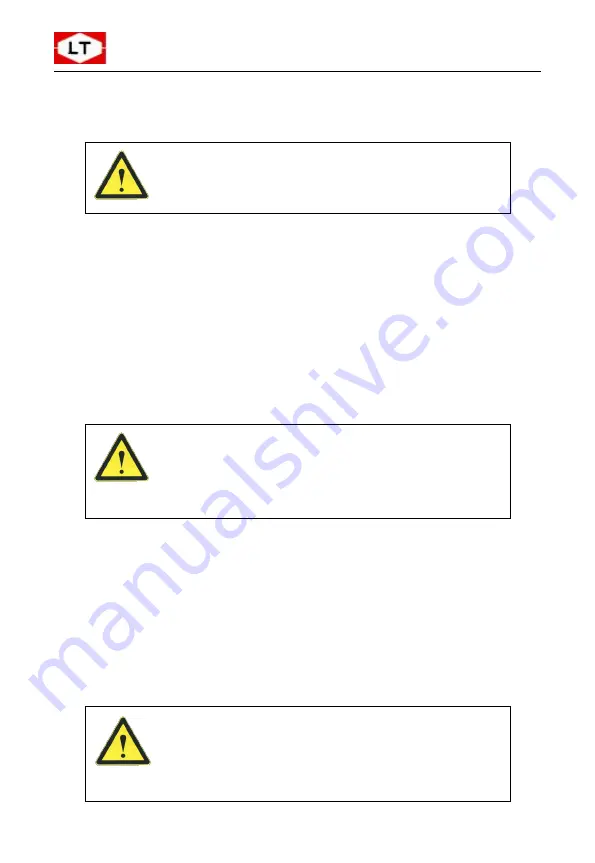
Zhengzhou Linghang Robot Co.,Ltd
19
4.1 Locking sequence
Note: The locking mechanism must be in the unlocking position when
attempting to connect the tool quick-change device. Failure to comply
with this condition may damage tool changer or robot.
1.Please place the master plate right above the tool plate and supply
compressed air to the unlock port.
2.Move the master plate toward to the tool plate so that the positioning pin
enters the positioning hole on the tool plate, program the robot so that the master
plate and the tool plate are aligned axially and parallel to each other (as close as
possible). This will minimize movement and abrasion of the tool changers during
locking process.
Note: Clearance locking technology allows the device to maintain
some distance between the master plate and the tool plate. Do not
touch the mating surface of the tool before connecting the
masterplate. Contact may damage the unit or robot.
3.
When the combination surface between the master plate and the tool plate
is within the specified gap, the pressure is released from the unlock port and air is
supplied to the locked port. The tool plate is pulled towards the master plate and
locked. During operation, air pressure must be maintained on the locking ports to
ensure a rigid connection.
4.
A sufficient delay must be set between the solenoid valve action and the
robot movement so that the locking process can be completed before the robot is
moved.
Note: If air pressure is lost during operation, the fail-safe design
prevents the tool plate from being droped. Do not use quick tool
change device in self-locking condition. Before resuming normal
operation, refill the air pressure and ensure that the quick tool change device is in a