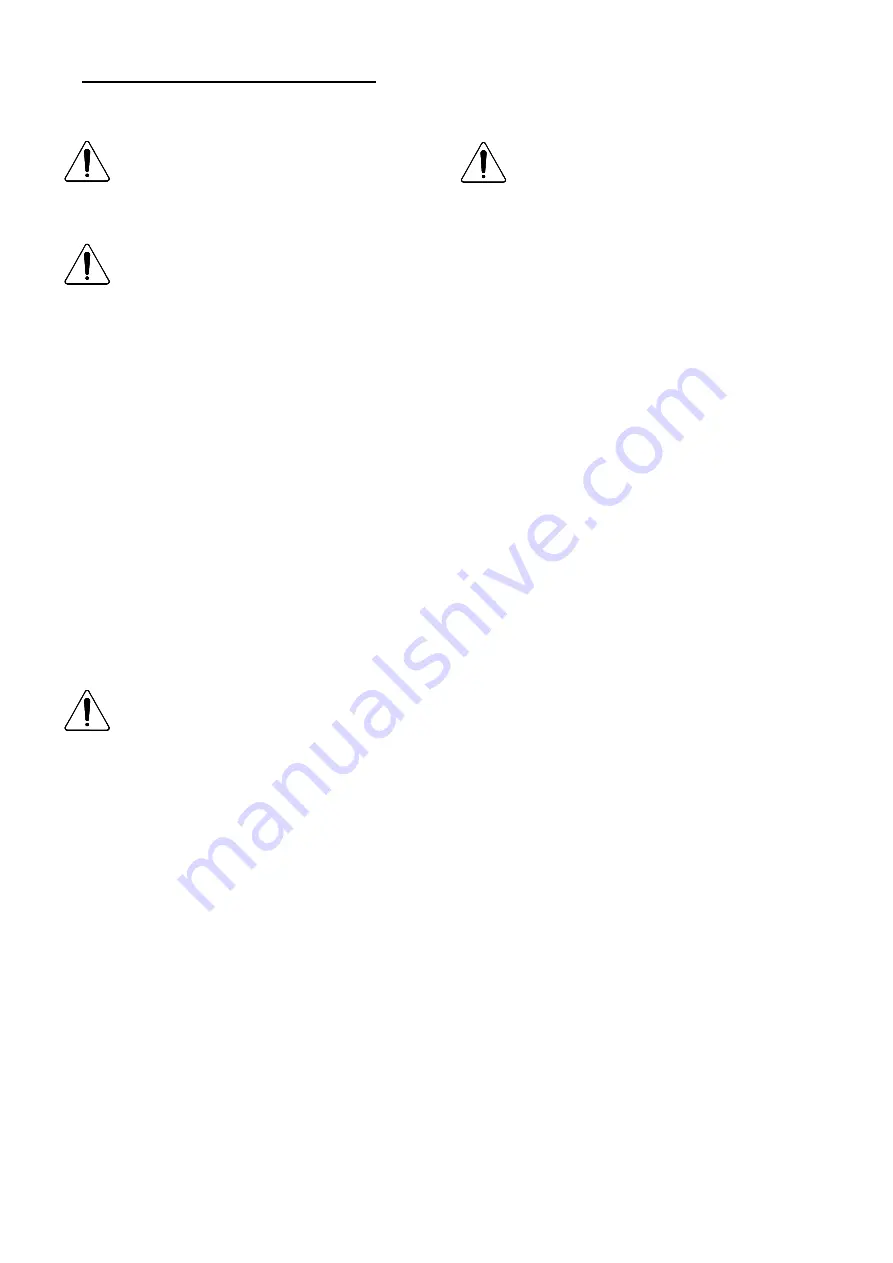
TRACTOR PREPARATION
Rear Counterweight
Rear Counterweight
Rear Counterweight
Rear Counterweight
CAUTION:
CAUTION:
CAUTION:
CAUTION:
CAUTION:
CAUTION:
CAUTION:
CAUTION:
CAUTION:
CAUTION:
CAUTION:
CAUTION:
▶ ROPS System
▶ ROPS System
▶ ROPS System
▶ ROPS System
▶ Tractor Hydraulic System
▶ Tractor Hydraulic System
▶ Tractor Hydraulic System
▶ Tractor Hydraulic System
Certain specific conditions may not
permit safe use of loader at loader
rating or may require more careful
restricted operation at the rated load.
Add recommended rear tire liquid
weight, rear wheel or rear ballast for
increased stability.
Refer to Tractor Operator's Manual for
specific recommendations on counterweight
The tractor must be equipped with an
approved ROPS System to ensure adequate
operator's protection.
The use of adequate counterweight to counter
balance for maximum loader capacity is
required for safe loader operation.
Weight added to rear of the tractor provides
better traction and easier, more efficient loader
operation. The tractor can be counter weighted
by filling rear tires with liquid calcium solution
and/or by the installation of rear wheel weights.
Tractor operation in a loader application
significantly increase demands on the tractor
Hydraulic System. Check the tractor Hydraulic
system fluid level daily. Refer to your tractor
Operator's Manual maintenance section for
instructions regarding tractor hydraulic system
maintenance.
Additional counterweight requirements will vary
Do not exceed the manufacturer's rating
for maximum gross vehicle weight. Refer
to Operator's Manual or ROPS serial
plate provided with tractor.
- 11 -
CAUTION:
CAUTION:
CAUTION:
CAUTION:
The tractor/loader must only be operated with all safety equipment properly installed.
▶ TRACTOR TIRES
▶ TRACTOR TIRES
▶ TRACTOR TIRES
▶ TRACTOR TIRES
▶ Wheel Tread Settings
▶ Wheel Tread Settings
▶ Wheel Tread Settings
▶ Wheel Tread Settings
▶ Tire Inflation
▶ Tire Inflation
▶ Tire Inflation
▶ Tire Inflation
▶ Front Counterweight
▶ Front Counterweight
▶ Front Counterweight
▶ Front Counterweight
maintenance.
Additional counterweight requirements will vary
with
loader
attachments
and
equipment
applications. Additional weight can be added by
installation of Three Point Hitch mounted
ballast.
Tractor front wheel tread setting must be
restricted
to
wheel
tread
spacing
recommended in the tractor Operator's
Manual.
Front tires must be maintained at the maximum
recommended inflation to maintain normal tire
profile with the added weight of loader/material.
Rear tires must be maintained at equal pressure
within the recommended tire inflation range.
Unequal rear tire inflation can prevent loader
attachment from contacting the ground across
its full width.
Use
of
front
counterweight
is
not
recommended when tractor is being used in a
loader application. Front counterweight adds
unnecessary front axle load in loader
applications.
Selection of tires(size, profile, tread type)
should be restricted to tire recommendations as
specified by LS Mtron
Adhere to recommendation in your Tractor
Operator's Manual concerning hydraulic fluid
and filter specifications, and change intervals.
- 11 -