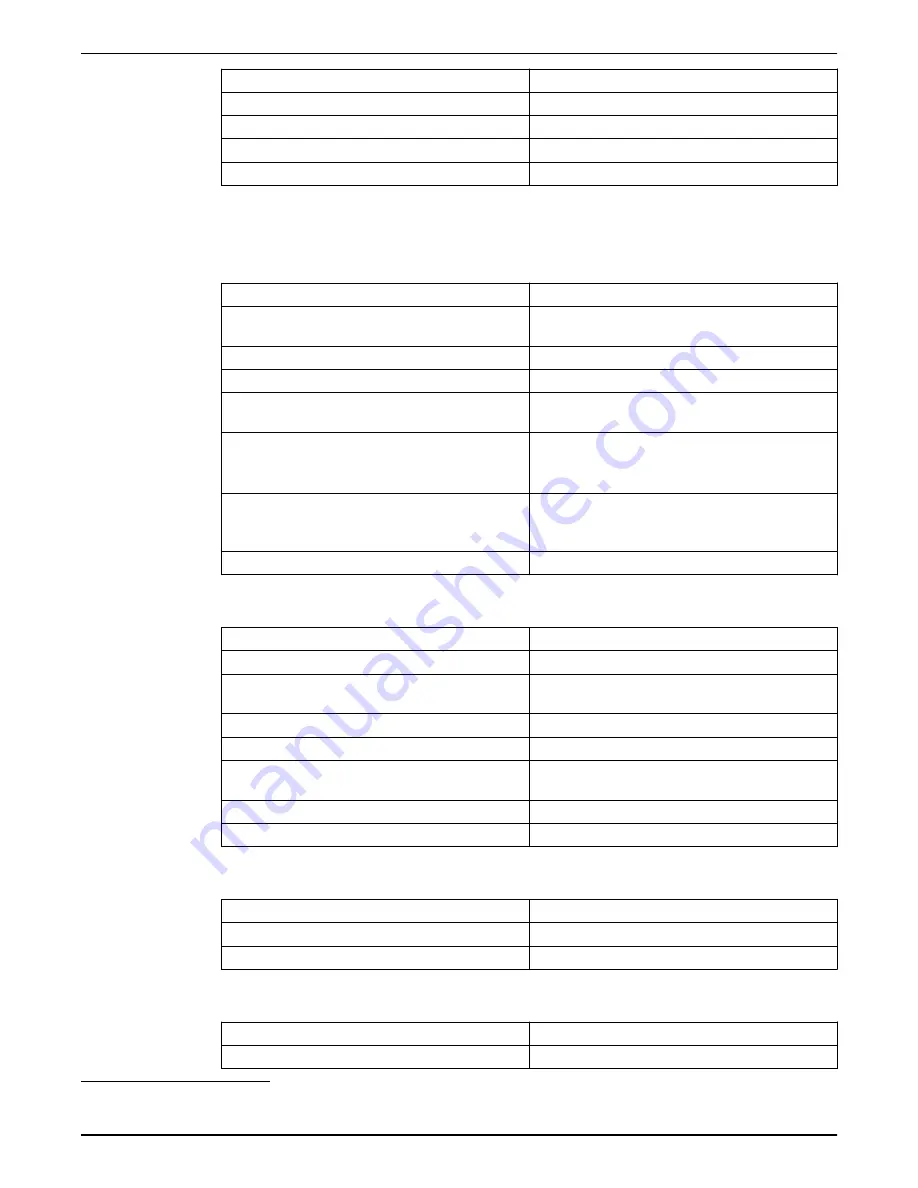
Cause
Remedy
Pump unit mechanically seized up
Check and repair the unit
Power supply cable is damaged
Replace the power supply cable
Check valve faulty
Replace the check valve
Foot check valve faulty
Replace the foot check valve
7.5 The thermal motor protection trips
The motor thermal overload protection triggers occasionally, or after the unit has been
running for a few minutes
Cause
Remedy
It is calibrated at a value too low in relation to the rated
current of the motor
Recalibrate
Input voltage outside the rated limits
Make sure the voltage values are correct
Unbalanced input voltage
Make sure the voltage of the three phases is balanced
Incorrect working curve (flow rate greater than the
maximum permitted flow rate)
Reduce the required flow rate
Liquid too dense, presence of solid or fibrous substances
(unit overloaded)
• Reduce the density of the liquid and/or
• Remove the solid substances and/or
• Increase the size of the motor
Room temperature too high, exposure to sunlight
• Lower the temperature at the point of the thermal
overload protection and/or
• Protect against direct sunlight
Unit faulty
Send the unit to an authorised workshop for testing
7.6 The unit runs but there is little or no flow rate
Cause
Remedy
Motor turns in the wrong direction
Check the direction of rotation and change it if necessary
Incorrect priming (there are air bubbles in the suction
pipe or in the unit)
Repeat the priming procedure
Cavitation
Increase the NPSH
7
available in the system
Check valve locked in closed or partially closed position
Replace the check valve
Foot check valve locked in closed or partially closed
position
Replace the foot check valve
Discharge pipe throttled
Remove the throttling
Piping and/or unit clogged
Remove the clogging
7.7 When turned off, the unit turns in the opposite direction
Cause
Remedy
Check valve faulty
Replace the check valve
Foot check valve faulty
Replace the foot check valve
7.8 The unit produces excessive noise and/or vibrations
Cause
Remedy
Cavitation
Increase the NPSH
8
available in the system
7
Net Positive Suction Head
8
Net Positive Suction Head
7 Troubleshooting
e-HM Series Installation, Operation and Maintenance Manual
31
Summary of Contents for e-HM series
Page 1: ...Installation Operation and Maintenance Manual e HM Series Multistage Horizontal Pump Unit...
Page 2: ......
Page 42: ......
Page 43: ......