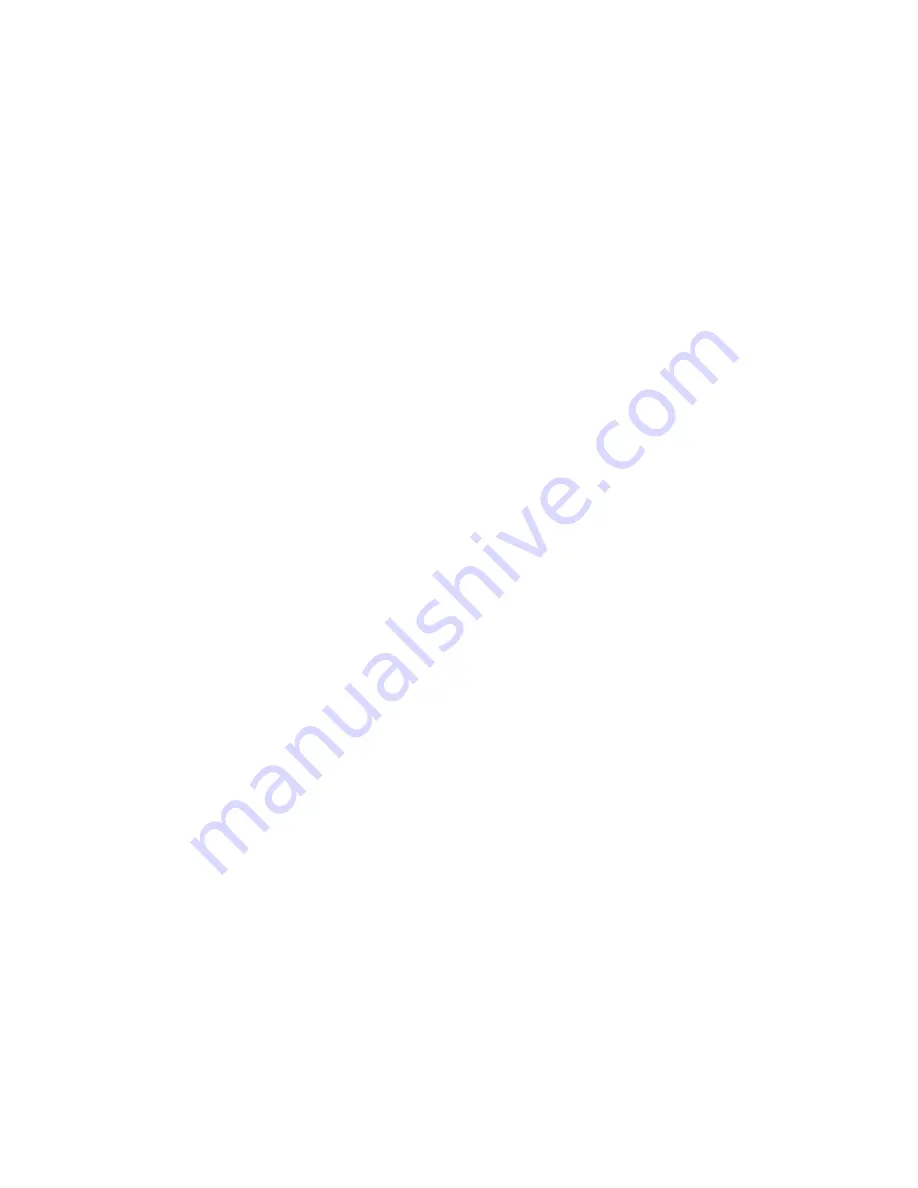
12
WHAT YOU NEED TO OPERATE THIS MACHINE?
A properly grounded 110-120 VAC 50/60 hz. Circuit or a 220-240 VAC 50/60 hz. 30-50 amp
Circuit.
Remember: Machine must be grounded to work properly and safely!
A clean and well-ventilated working place
Heavy Duty Welding Gloves
An Auto-Darkening Welding Mask to provide eye protection
A compressed gas cylinder containing pure Argon
Stainless steel wire welding brushes for each material to be welded
A stone grinding wheel or a Tungsten Sharpener to sharpen the tungsten electrode
Control Panel Information
1.
Power switch 1 is located on the back of the machine.
2.
Downslope adjustment knob 2: In order to reduce the current gradually before the welding
stops.
a.
This knob is to adjust the current descending time.
b.
Note: If you are using the “foot pedal” control; you should turn this knob
counter-clockwise to “0”.
3.
Post-flow time adjustment (knob 3): To prevent the work piece from becoming oxidized, let
the argon flow for few seconds after stopping the welding arc. This knob is for adjusting the
post-flow time.
4.
Foot pedal switch 4: When the switch is on the “OFF” position, the current is adjusted by
using the Current adjustment knob 5; when it is on the “PEDAL” position, the current is
adjusted dynamically by foot pedal.
5.
Current adjustment knob 5. Note: it only works when switch 4 (pedal/off) is on the “OFF”
position. If switch 4 is set on the “PEDAL” mode, the current would be fully controlled by
using the foot pedal instead.
6.
Pulse duty knob 6: During AC aluminum Tig welding, Note: For an increased welding
voltage of more than 150A, use pulse duty below 30% (or less than -1). For medium voltage
(from 100A to 150A), use pulse 50% (0 on knob); For voltages less than 100A, use pulse duty
more than 50% (+1 to +5).
7.
Pre-flow time adjustment (knob 7): For better welding results, argon gas should come earlier
than the current. This knob is to adjust the time between argon start and electric arc start.
8.
Stick welding/Tig Welding Switch 8. For Tig welding, please switch to “Tig Mode”, For Stick
Welding, please switch to “MMA mode”.
9.
AC/DC Switch 9: For Aluminum welding, please switch to AC, for non-aluminum welding,
please switch to DC.
Overheat protection indicator (OC light): This is to protect the machine if it overheats. If the light is
on, please stop the machine for 4 to 10 minutes before turning it on again.