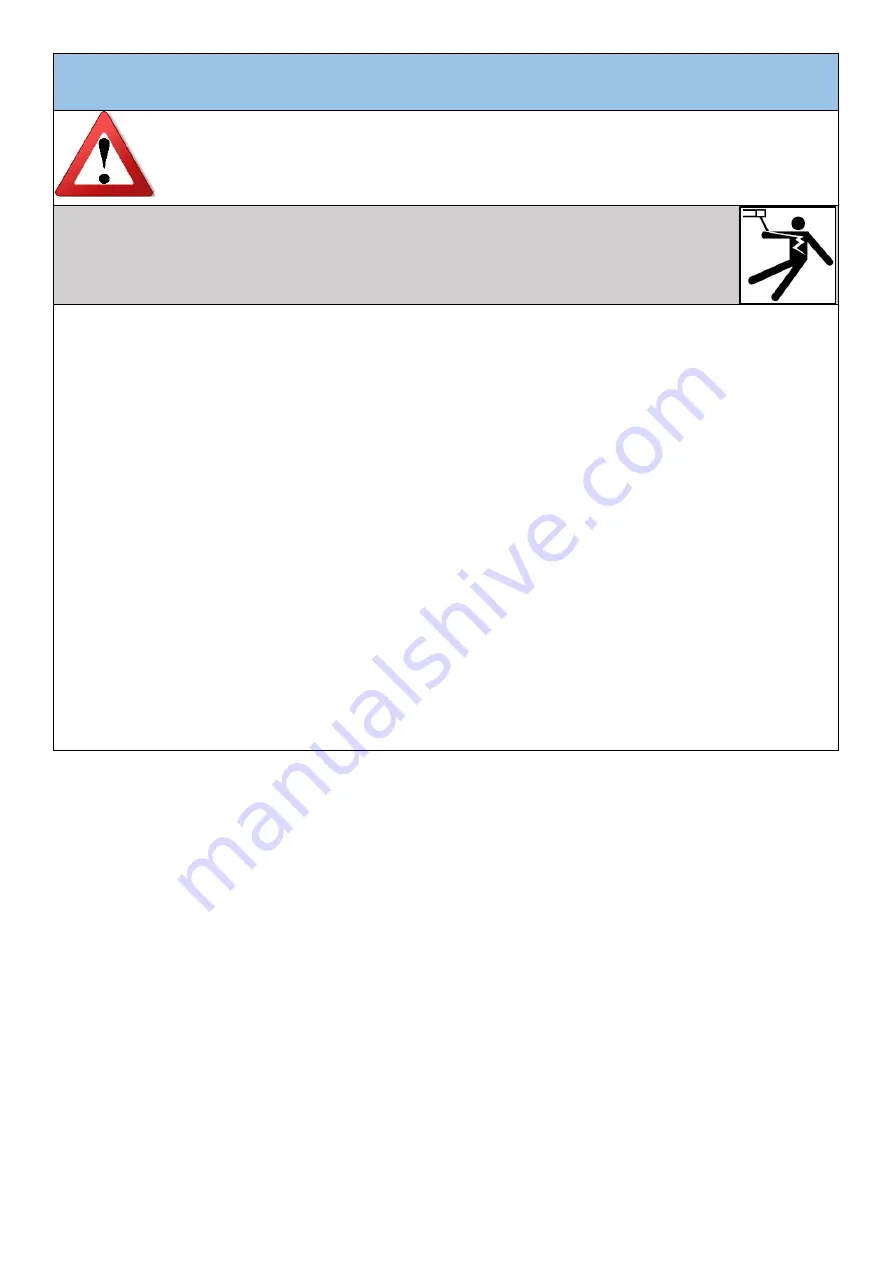
19
/
21
TROUBLESHOOTING
PLEASE READ AND UNDERSTAND THIS ENTIRE SECTION BEFORE
OPERATING YOUR MACHINE. ONLY QUALIFIED PERSONNEL SHOULD
OPERATE THIS EQUIPMENT. OBSERVE ALL SAFETY INFORMATION
THROUGHOUT THIS MANUAL.
ELECTRIC SHOCK can be fatal
Service and Repair should only be performed by Trained Personnel. Have a
qualified electrician install and service this equipment.
HOW TO USE TROUBLESHOOTING GUIDE
This Troubleshooting Guide is provided to help you locate and repair possible machine
malfunctions. Simply follow the three-step procedure listed below.
Step 1. LOCATE PROBLEM (SYMPTOM).
Look under the column labeled “PROBLEM (SYMPTOMS)”. This column describes
possible symptoms that the machine may exhibit. Find the listing that best describes the
symptom that the machine is exhibiting.
Step 2. POSSIBLE CAUSE.
The second column labeled “POSSIBLE CAUSE” lists the obvious external possibilities
that may contribute to the machine symptom.
Step 3. RECOMMENDED ACTION.
This column provides a course of action for the Possible Cause.
If you do not understand or are unable to perform the Recommended Course of Action
safely, contact your sales agency.