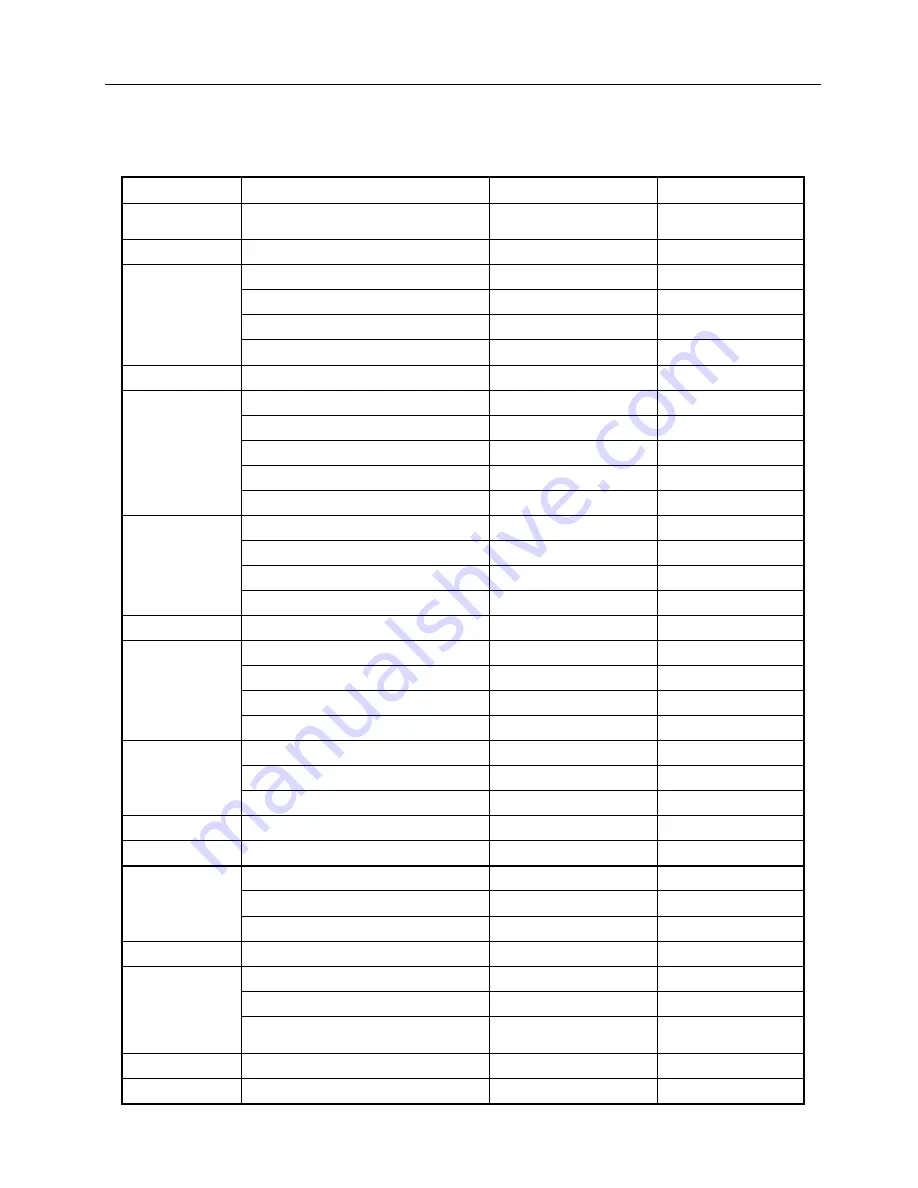
Chapter II Repair Standards
- 3 -
2-1 Standards for engine repair
Unspecified unit: mm
Part
Item
Standard
Service limit
Engine
Maximum no-load speed
Cylinder pressure
5,000 rpm
≧
1.17 Mpa (1,400 rpm)
6,000 rpm
--
Cylinder
Inner diameter of cylinder
70
70.165
Piston
Skirt O.D.
69.985
69.845
Piston-to-cylinder clearance
0.015-0.05
0.12
Piston pin bore ID
18.002
18.048
Piston -to-piston pin bore clearance
0.002-0.014
0.06
Piston pin
Outside diameter
18.0
17.954
Piston rings
Ring side clearance (Top/Second)
0.015-0.045
0.15
Ring end gap (Top/Second)
0.2-0.4
1.0
Ring end gap(Oil ring)
0.15-0.35
1.0
Ring width (Top/Second)
1.0
0.88
Ring width (Oil ring)
2.5
2.37
Connecting rod
Small end I.D.
18.002
18.07
Big end I.D.
30.02
30.066
Big end oil clearance
0.04-0.063
0.12
Big end side clearance
0.1-0.7
1.1
Crankshaft
Crankshaft O.D.
29.98
29.92
Valves
Clearance(cold) (IN)
0.10~0.15
-
Clearance(cold) (EX)
0. 10~0.15
-
Stem O.D. (IN)
5.48
5.318
Stem O.D. (EX)
5.44
5.275
Valve guide
I.D. (IN,EX)
5.50
5.572
Stem-to-guide clearance (IN)
0.02-0.044
0.10
Stem-to-guide clearance (EX)
0.06-0.087
0.12
Valve seat
Seat width
0.8
2.0
Valve spring
Free length
30.5
29.5
Camshaft
Cam height (IN)
27.7
27.45
Cam height (EX)
27.75
27.50
O.D. (bearing section)
13.984
13.916
Crankcase cover
Camshaft holder I.D.
14.0
14.048
Carburetor
Main nozzle
0.65
-
Float height
13.7±1.5
-
Number of turning circles of mixture
adjusting screw
2-1/8 circles
-
Spark plug
Gap
0.7-0.8
-
Ignition coil
Air gap (at flywheel)
0.4±0.05
-