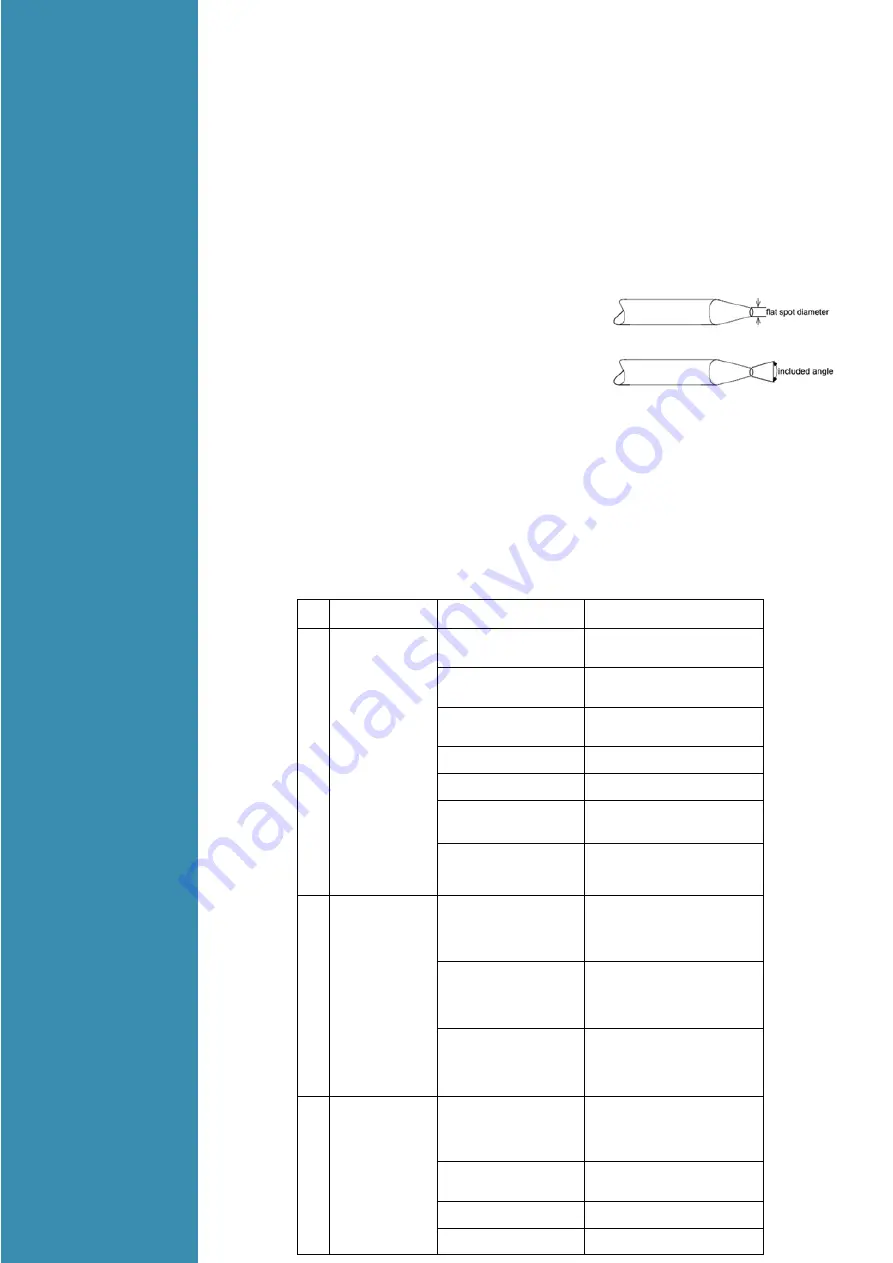
3.4.6
TIG Welding
trouble
shooting
The following chart addresses some of the common problems of TIG welding. In all cases of
equipment malfunction, the manufacturer’s recommendations should be strictly adhered
to and followed.
NO. Trouble
Possible Reason
Suggested Remedy
1
T
ungsten burning
away quickly
Incorrect Gas or No Gas
Use pure Argon. Check cylinder has
gas, connected, turned on and torch
valve is open
Inadequate gas flo w
Check the gas is connected, check
hoses, gas valve and torch are not
restricted.
Back cap not fitted correctly
Make sure the torch back cap is
fitted so that the o -ring is inside the
torch body
Torch connected to DC +
Connect the torch to the DC - output
terminal
Incorrect tungsten being used Check and change the tungsten type
if necessary
Tungsten being oxidised after
weld is finishe d
Keep shielding gas flowing 10–15
seconds after arc stoppage. 1 second
for each 10amps of weld current.
Tungsten melting
back
into the nozzle on AC
welding
Check that correct type of tungsten is
being used. Check the balance
control is not set too high on the
balance-reduce to lower setting
2
Contaminated
tungsten
Touching tungsten into the
weld pool
Keep tungsten from contacting weld
puddle. Raise the torch so that the
tungsten is off of the work piece 2 -
5mm
Touching the filler wire to the
tungsten
Keep the filler wire from touching
the tungsten during welding, feed the
filler wire into th e leading edge of
the weld pool in front of the tungsten
Tungsten melting into the
weld pool
Check that correct type of tungsten is
being used. Too much current for the
tungsten size so reduce the amps or
change to a larger tungsten
3
Porosity - poor
weld appearance
and colour
Wrong gas / poor gas flow
/gas leak
Use pure argon. Gas is connected,
check hoses, gas valve and torch are
not restricted. Set the gas flow
between 6-12 l/min. Check hoses
and fittings for holes, leaks et
Contaminated base metal
Remove moisture and materials like
paint, grease, oil, and dirt from base
metal
Contaminated filler wir e
Remove all grease, oil, or moisture
from filler metal
Incorrect filler wir e
Check the filler wire and change if
necessary
Electrode Included Angle/Taper
DC Welding Tungsten electrodes for DC welding should be ground longitudinally and concentrically
with diamond wheels to a specific included angle in conjunction with the tip/flat preparation. Different
angles produce different arc shapes and offer different weld penetration capabilities. In general,
blunter electrodes that have a larger included angle provide the following benefits
:
• Last Longer
• Have better weld penetration
• Have a narrower arc shape
• Can handle more amperage without eroding.
Sharper electrodes with smaller included angle provide:
• Offer less arc weld
• Have a wider arc
• Have a more consistent arc
The included angle determines weld bead shape and size. Generally, as the included angle
increases, penetration increases and bead width decreases.