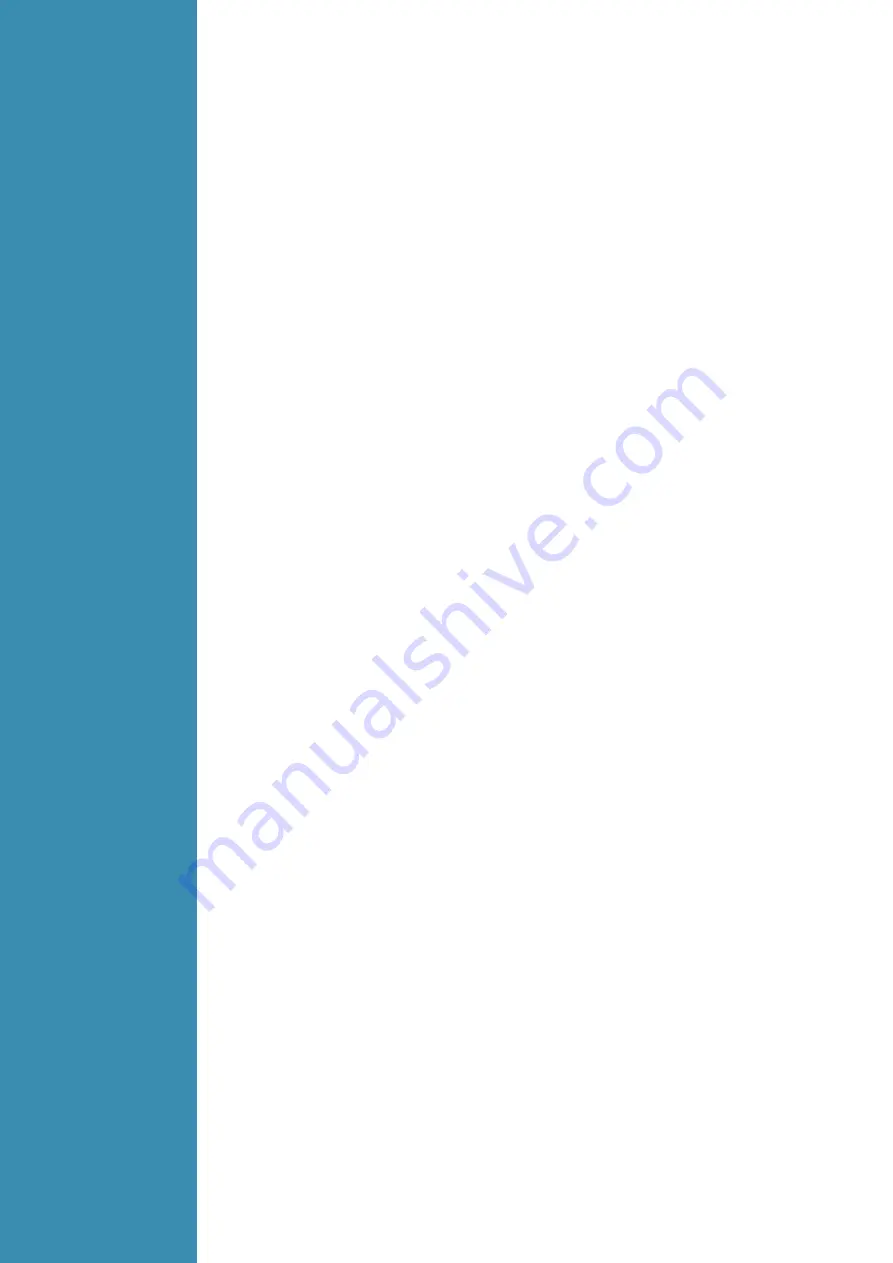
3.4
Maintenance
of MIG Gun
mechanism
1. Service the wire feed mechanism at least every time the reel is changed.
· Check the wear of the feed roll groove and change the feed roll when necessary.
· Clean the welding gun wire guide with compressed air.
2. Cleaning the wire guide
Pressure of the feed rolls remove metal dust from the filler wire’s surface which then finds its way to the
wire guide. If the wire guide is not cleaned, it gradually clogs up and causes wire feed malfunctions.
Clean the wire guide in the following manner
:
Remove the welding gun’s gas nozzle, contact tip and contact tip’s adapter.
With a pneumatic pistol, below compressed air through the wire guide.
Blow the wire feed mechanism and reel housing clean with compressed air.
Reattach the welding gun’s parts. Tighten the contact tip and contact tip’s adapter to spanner
tightness.
3. Changing the wire guide
If the wire guide is too worn or totally clogged, change it to a new one according to the following
instructions.
Open the mounting nut of the wire guide which exposes the end of the wire guide.
Straighten the welding gun’s cable and withdraw the wire guide from the gun.
Push a new wire guide in to the gun. Make sure that the wire guide enters all the way into the contact
tip’s adapter and that there is an O-ring at the machine-end of the guide.
Tighten the wire guide in place with the mounting nut.
Cut the wire guide 2mm from the mounting nut and file the sharp edges of the cut round.
Reattach the gun in place and tighten the parts to spanner tightness.
3.5
Maintenance
of the wire
feed
mechanism
Changing the feed roll groove
The feed roller is factory set for welding filler wires of 0.6-0.8mm V shape. The feed roller side must be
changed if you use 0.6mm thick filler wire.
Threading the filler wire
Threading the filler wire as the follow steps:
Open the reel housing by pressing on the opening button and install the wire reel in such a way that it
rotates counter clockwise. You can use a diameter 200mm wire reel in the machine.
Attach the reel with a reel lock.
Unfasten the wire end from the reel, but hold on it all the time.
Straighten the wire end for approximately 20 cm and cut the wire in the straightened location.
Open the pressure control level which then opens the feed gear.
Thread the wire through the wire’s rear guide to the gun’s wire guide.
Close the feed gear and fasten it with the pressure control lever. Make sure that the wire runs in the
feed roll groove.