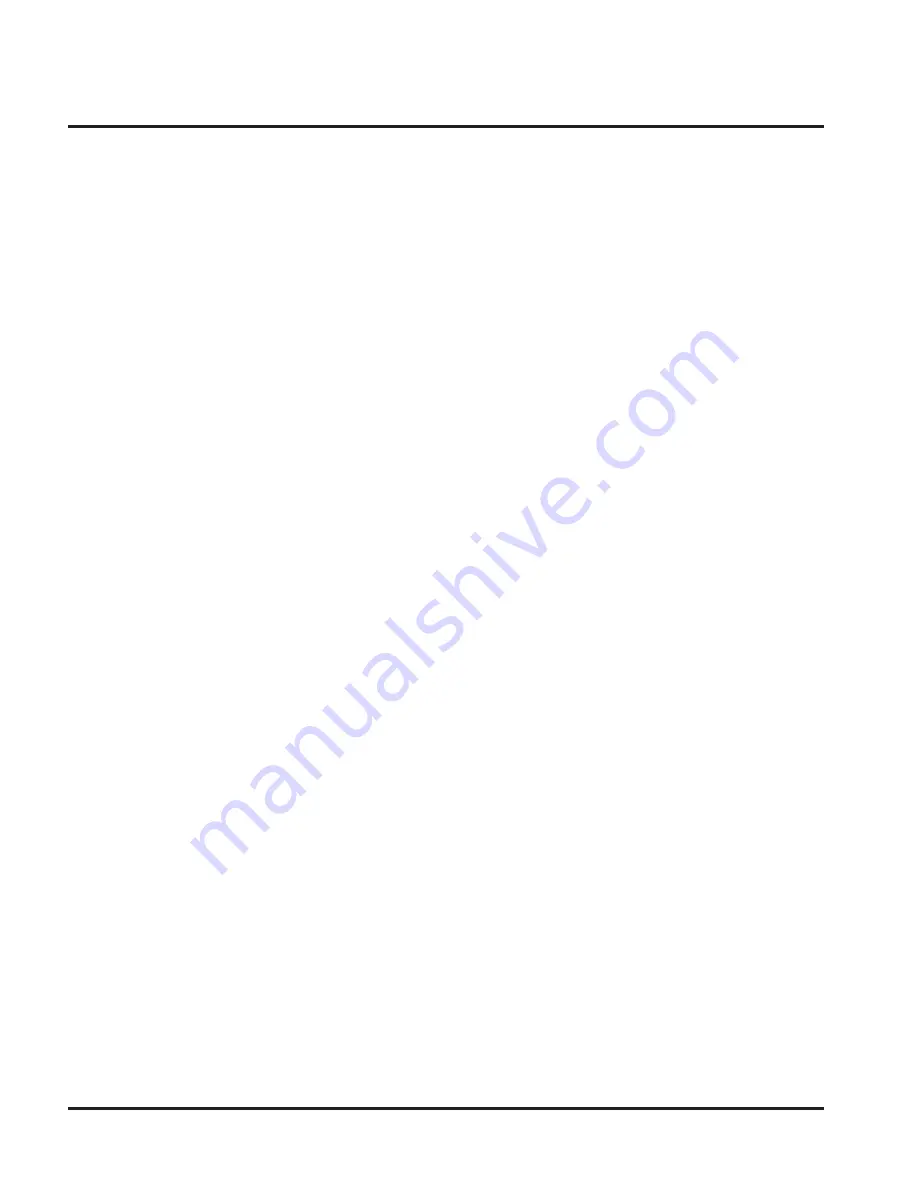
4
Carbide Cutter OM
Mandatory Shut-Down Procedure
• Stop the machine and attachment on a level surface
and lower the attachment to the ground.
• Move throttle to idle position.
• Disengage all power to the attachment.
• Shut off engine and remove the key.
Wait until the rotor has stopped completely before
inspecting the attachment.
Safety Rules
These are general safety considerations. Additional
precautions may be necessary to operate your
machine in a safe manner. Be certain you are operating
your machine in accordance with all safety codes,
OSHA rules and regulations, insurance requirements
and local, state, and federal laws.
•
Read and observe all warnings decals on the machine
before attempting to operate the attachment. Do not
attempt to operate this attachment unless all factory
devices and decals are in place. Keep safety decals
clean of dirt and grime. Keep all guards, shields and
decals in place.
• Remove from area of operation all foreign objects
such as bottles, rocks, wire, etc., that might become
tangled in the rotor, causing damage to the machine
or be thrown striking other objects.
• Do not allow any people and animals within 300 feet
of the machine and attachment during operation.
• Do not allow anyone to operate the attachment
until he or she has read the owner’s manual and is
completely familiar with all safety precautions. Keep
the work area clear of all unauthorized personnel.
• Do not allow persons under the influence of alcohol,
medications, or other drugs that can impair judgment
or cause drowsiness to operate or maintain the
machine.
• Always use an approved roll bar and seat belt for
safe operation. Overturning a machine without a roll
bar and seat belt can result in injury or death.
• Use the handholds and step plates when getting on
and off the machine to prevent falls. Keep steps and
platform cleared of mud and debris.
• Always have an operator in the machine while the
attachment is in operation. Never leave the machine
and attachment running and unattended.
• Operate the attachment only from the operator’s
seat.
• Keep your feet on the pedals, (floor plates) seat belt
fastened snuggly and seat bar lowered, (if equipped),
when operating the attachment.
• The adjustable push bar could contact the machine
in some positions. Before starting the power unit,
set the push bar in the most forward position, then
slowly rotate the attachment back while an assistant
checks for clearance. Repeat this process in the
other settings to determine which positions are
usable with your machine.
• Never attempt to make any adjustments while the
attachment is running or the key is in the “ON”
position in the machine. Before leaving the operator’s
position, disengage power to the attachment, shut
off engine and remove ignition key.
• Disengage auxiliary hydraulics and place all machine
controls in neutral and engage the parking brake
before starting the engine.
• Become familiar with and know how to operate all
safety devices and controls on the machine and
attachment before attempting to operate. Know how
to stop the machine and attachment before starting
it.
• Repeated impact of the knives with hard objects can
cause excessive wear and damage to the skid-steer
or attachment. Be sure to maintain recommended
ground clearance as specified in this manual.
• Should excessive vibration occur, disengage the
auxiliary hydraulics immediately and shut off engine.
Do not continue to operate the attachment until the
problem has been determined and corrected.
•
Do not start, operate, or work on this attachment until
you have carefully read and thoroughly understand
the contents of this manual and the operator’s
manual for your machine.
Safety Instructions
Summary of Contents for 61G4 Series
Page 2: ......
Page 10: ...6 Carbide Cutter OM Safety Instructions Carbide Cutter Identification ...
Page 14: ...10 Carbide Cutter OM ...
Page 29: ...25 Carbide Cutter OM PARTS IDENTIFICATION Parts Identification ...
Page 50: ...46 Carbide Cutter OM ...
Page 55: ......