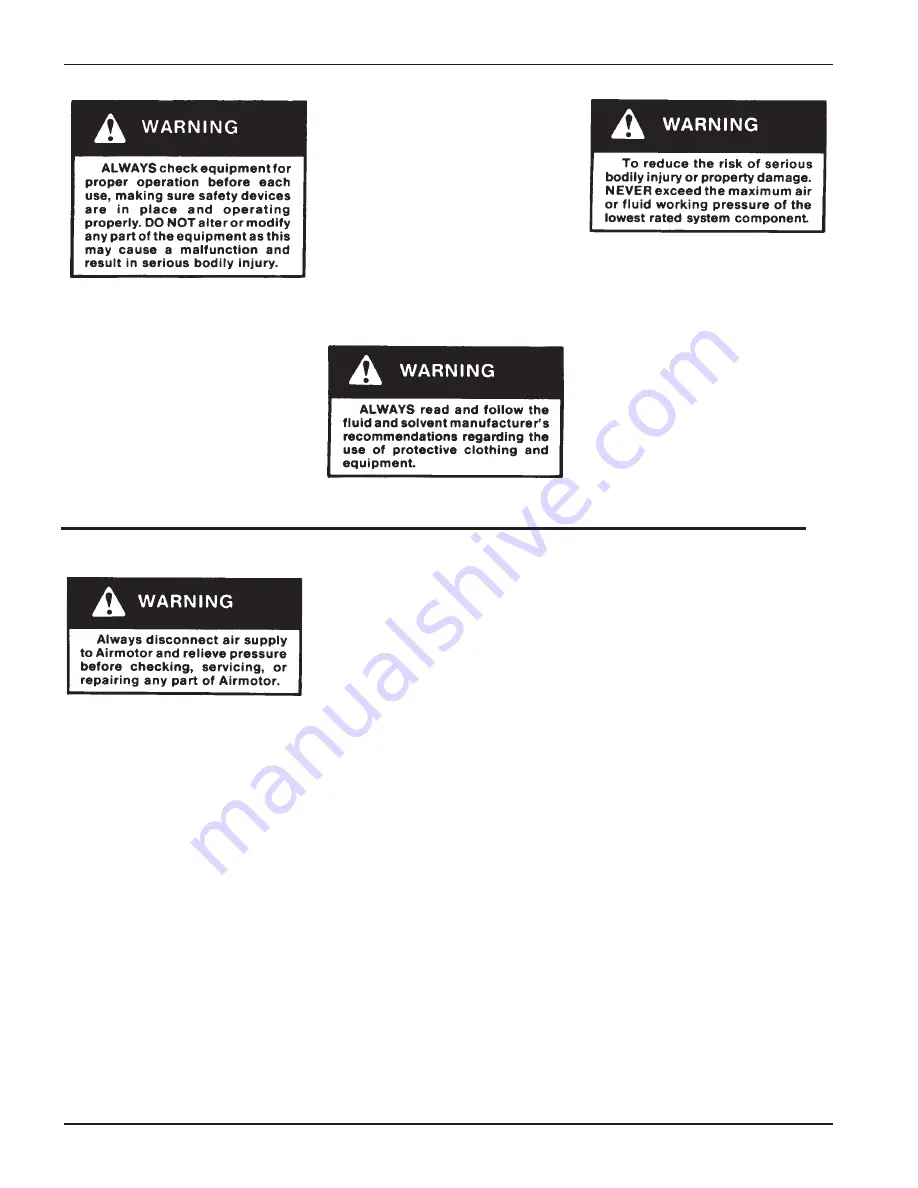
Page Number - 6
BEFORE CONNECTING AIR-
MOTOR TO AIR LINE
LOCTITE
®
AIRMOTORS are fully pneumatic
and require a minimum specified size of air
supply hose for proper operation. Check
specification for minimum ID. of the air
supply hose and select corresponding
sizes of air controls and accessories for
non-restrictive air flow.
If quick disconnect coupling should be
used, install supplied coupler to insure
proper airmotor operation.
NOTE: Whenever flammable materials
are pumped, ground Airmotor accord-
ing to Local Codes.
OPERATING PRECAUTIONS
Use Loctite
®
replacement parts to assure
compatible pressure rating.
Heed ALL warnings.
DO NOT OPERATE Airmotor in excess of
recommended pressure range.
Disconnect air line and relieve (vent)
pressure when Airmotor sits idle for long
periods of time and before servicing.
SERVICE AND DISASSEMBLY
PROCEDURE
ATTACHING AIRMOTOR TO
PUMPTUBE
1. Tightly attach the tie rods(ltem 41) to
the Airmotor lower casting. Use short
threaded end of tie rods.
2. Mount Airmotor on top of pump tube
outlet and tightly connect pump tube
coupling nut to Airmotor Piston Rod (Item
5).
3. Hand tighten tie rods to the pump tube
with four nuts (Item 42) supplied with
Airmotor.
4. Connect air supply and slowly cycle
pump several times using only enough
air pressure to operate pump without
stalling.
5. STOP pump on "UP" stroke and tighten
four nuts to securely fasten Airmotor to
pump tube.
Tools Required
1. 7/64" (.109) Allen Wrench
2. 5/32" (.156) Allen Wrench
3. 3/16" (.189) Allen Wrench
4. 1/8" (.125) Allen Wrench
5. 9/64" (.1406) Allen wrench
6. 3/4" (.750) Open End Wrench (for 6" Air-
motor)
7. #1 Phillips screwdriver
8. 1/2” (.500) Open End Wrench
9. 1/2" (.500) Box End Wrench
10. Pliers
11. 0-100 in. lb. Torque Wrench
12. 0 - 75 Ft. lb. Torque Wrench.
The modular design of the Airmotor and
accessibility of vital operation parts make
service available without taking Airmotor
out of line or without complete disassembly.
Power Valve
1. Remove four screws (Items 27 & 34)
with 3/16” hex wrench (2 on each
side).
2. Remove End Caps (Items 10 & 14).
3. Push out Valve Spool (Item 13).
4. Remove Spool Bumpers (Item 9) (One
from each end).
“Optional” Pump Stop
Subassembly
1. Remove four Screws (item 23) (two on
each end) with 3/16" Allen wrench and
pull out Pump Stop Subassembly.
2. Remove two Screws (Item 39) with
7/64" Allen wrench and lift out Valve
Body (item 17).
3. Remove four Screws (Item 32) (two on
each side of Pump Stop) with1/8" Allen
wrench and remove Signal Valve Caps
(Item 31) and Air Signal Valves (Item
20).
4. Remove four (4) screws (item 80) with
9/64" Allen wrench to remove labyrinth
sub-assembly from Pump Stop.
5. Remove four Screws (Item 24) with
3/16" Allen wrench and lift off Upper
Body (Item 50) and Upper Gasket (Item
51).
6. Remove Gasket Plate (Item 52) and
Lower Gasket (Item 53).
7. Remove Air Filter (Item 40) in two
locations.
8. Remove Pump Sleeve (Item 56) and
Piston (Item 55).
9. Remove Diaphragm Seal and Retainer,
Diaphragm, Spring and Stop Valve Assy.
(Items 61, 57, 58, 59 & 60).
10. Remove Trip Indicator (Item 48).
5. Remove “O” Ring (Item 11 )(One from
each end of valve body).
6. Remove four Screws (Item 37) with
3/16” hex wrench and lift valve body
(Item 12).
7. Remove Gasket (Item 15) to complete
valve disassembly.
8. To REASSEMBLE, REVERSE procedure.
11. To re-assemble, reverse the disassem-
bly procedure with the following
precautions
a. The upper and lower gaskets (items
51 & 53) should be coated with a
film of light oil (SAE 10) before
assembly.
b. When new umbrella valves (item 63)
are installed, note that the gasket
plate (item 52) has a circle and an
“X” stamped into both sides of the
gasket plate. The umbrella valve is
installed into the plate from the circle
side of the plate. One umbrella
valve should be installed into each
side of the plate so that the valve is
within the circle and the stub end
protrudes through the “X”.
c. After installing the umbrella valve
(item 63) the long rubber stem of the
valve is to be removed, leaving the
rubber ball end intact to secure the
valve to the plate.
d. When installing the pump sleeve,
(item 56) into the lower body, (item
54) the sleeve should be placed into
the lower body as shown in
Illustration on Page 12. When
properly installed the molded pin
protruding from the pump sleeve will
fit into a mating hole in gasket (item
53) and the gasket can then be
installed properly over pins, (item
66). If the sleeve is not properly
aligned as shown, the Pump Stop
cannot be assembled properly.
FOR AIRMOTOR WITH PUMP STOP