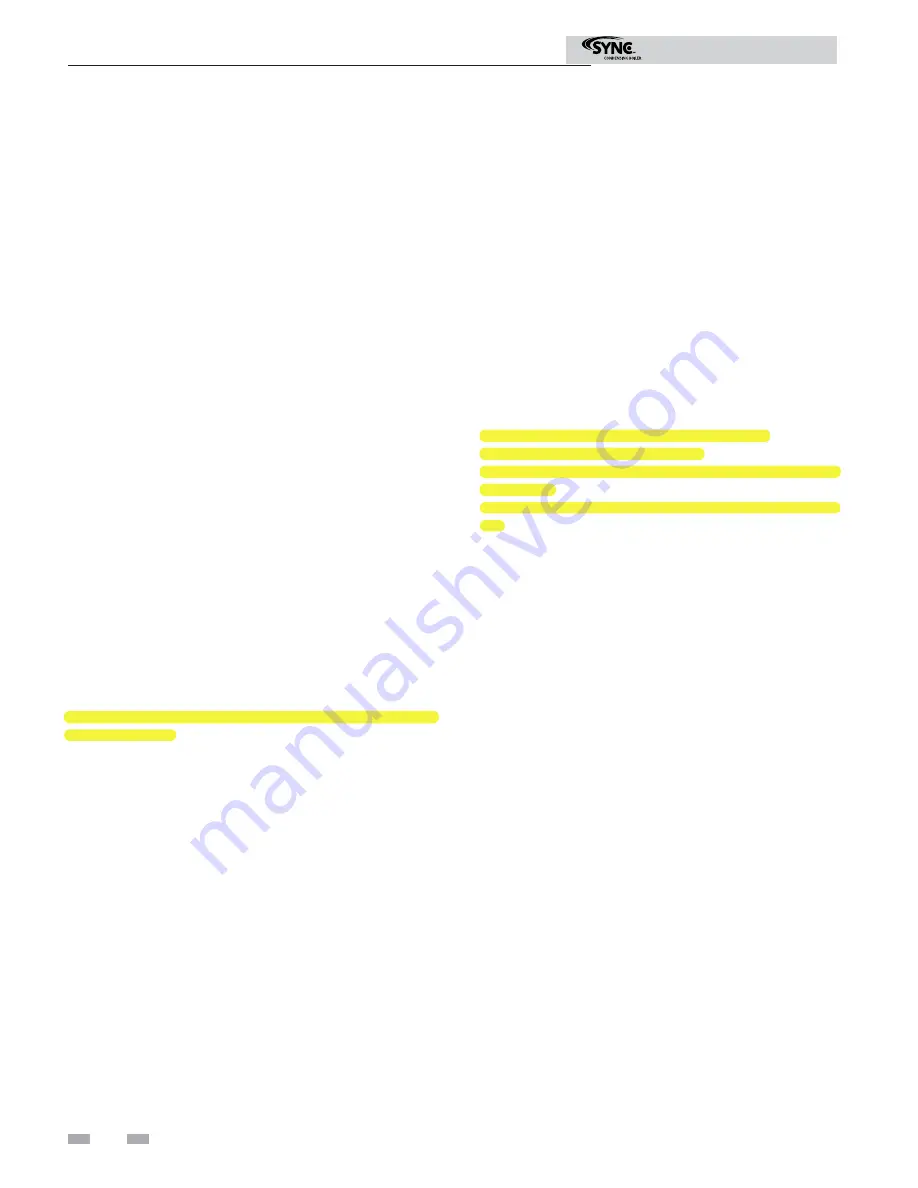
4
Modbus Instructions
2
Configuration
Timing Specifications
The baud rate for the Modbus board is selectable with Dip
switch #9.
1 = 19200 bps
0 = 9600 bps
Each message is started by at least 3.5 character times of
silence. The maximum delay between frames is 1.5 character
times.
When the system temperature and/or tank temperature is
provided by the BAS to the boiler, it is critical that the
temperature be updated every few seconds. If the boiler does
not receive updated temperatures within a timeout period
(installer adjustable), the control will revert to using its own
sensor inputs (if sensors are connected). The timeout is
programmable by pressing the MAIN>>SETUP>>BMS
buttons. The timeout is adjustable between 5 and 120
seconds. The default timeout is 10 seconds.
When the BAS is not providing either of these temperatures,
but is still controlling the boiler (such as providing a
modulation command), the BAS must refresh these
commands at least every 4 minutes. If the commands are not
refreshed, the boiler will revert to operating based on its own
inputs.
Parity
Parity is set by the position of Dip switch #10.
0 = No Parity
1 = Odd Parity
If No Parity is selected there will be two stop bits, otherwise
there will be one.
Data Transmission Mode
Many Modbus bus master devices can be configured to transmit
data in either Modbus RTU or Modbus ASCII modes. Since
RTU messages can be formatted to use fewer data bits and are
therefore more efficient, RTU has been chosen to be used with
all Lochinvar Modbus communication. Please ensure that the
master device is transmitting Modbus RTU.
Modbus Board Diagnostics
The Modbus board is equipped with three LED’s for visual
diagnostics: Two yellow LED’s and one green. One yellow LED
(D5) is used to indicate reception of data. The other yellow
LED (D6) is used to indicate transmission of data. The green
LED (D7) is used to show internal faults.
Internal Faults:
Normal Operation = 1 second on, 1 second off
Controller Fault = Continuously on
No Burner Control Communication = 0.5 seconds on, 1.5
seconds off
No Modbus Communication = 1.5 seconds on, 0.5 seconds
off
Modbus Communication
The Modbus communication commands and exception codes
that are supported by the Modbus communication board can
be found on pages 5 and 6 of this manual.